Different Types of Modern Warehousing Storage Solutions
Storage solutions offer a wide range of options to suit different industries and operational needs. From high-density pallet racking to advanced automation systems

In today's fast-paced world of logistics and supply chain management, the need for efficient and scalable warehousing storage solutions has never been greater. With businesses managing larger inventories and more complex distribution channels, traditional storage methods often fall short. Modern warehousing solutions offer an array of innovative storage options designed to meet the diverse needs of industries. From automation to high-density storage systems, these technologies help businesses optimize their space, reduce costs, and improve operational efficiency.
In this article, we will explore the different types of modern warehousing storage solutions, explaining how each contributes to the overall efficiency of a warehouse.
Importance of Modern Storage Solutions in Warehousing
Effective storage solutions are the backbone of efficient warehouse operations. The right system not only maximizes available space but also ensures that products are easy to access, organize, and track. With the rise of e-commerce and just-in-time inventory models, companies are under immense pressure to store and retrieve products quickly and accurately. This demand has driven the development of advanced storage technologies designed to reduce human error, improve organization, and speed up order fulfillment.
1. Pallet Racking Systems
a) Selective Pallet Racking
Selective pallet racking is one of the most common storage systems found in modern warehouses. It provides direct access to every pallet, making it ideal for businesses that require frequent picking of goods. The system consists of vertical frames and horizontal beams that hold pallets, offering flexibility in both height and width.
Advantages:
-
Easy to install and adjust according to storage needs.
-
Suitable for warehouses that store a variety of products.
Disadvantages:
-
Lower storage density compared to other racking systems.
b) Double-Deep Pallet Racking
Double-deep racking involves placing two rows of pallet racks back-to-back. This allows for higher storage density than selective racking, although it limits direct access to some pallets, requiring forklifts with extended reach capabilities.
Advantages:
-
Higher storage density.
-
More cost-effective for large volumes of products.
Disadvantages:
-
Limited direct access to pallets at the back.
2. Drive-In and Drive-Through Racking
Drive-in and drive-through racking systems are designed for high-density storage where forklifts can drive directly into the racking system to retrieve or store pallets. The key difference between the two is that drive-in racking has only one entry/exit point, while drive-through racking has entry/exit points at both ends.
Drive-In Racking:
-
Best suited for warehouses storing large volumes of the same product (ideal for cold storage).
-
Operates on a last-in, first-out (LIFO) basis.
Drive-Through Racking:
-
Allows for first-in, first-out (FIFO) inventory management.
Advantages:
-
High storage density.
-
Ideal for bulk storage.
Disadvantages:
-
Limited access to pallets in deeper racks.
-
May require careful forklift operation to avoid damaging racks.
3. Automated Storage and Retrieval Systems (AS/RS)
Automated Storage and Retrieval Systems (AS/RS) represent the cutting edge of warehouse automation. These systems use computer-controlled robots or shuttles to retrieve and store goods with minimal human intervention. AS/RS can be used in combination with racking systems and conveyor belts to transport goods within the warehouse.
Advantages:
-
Highly efficient and reduces labor costs.
-
Optimizes space by allowing vertical storage.
-
Increases accuracy in picking and inventory management.
Disadvantages:
-
High upfront investment costs.
-
Requires maintenance and specialized technical support.
Example: Amazon's Use of AS/RS
Amazon’s large-scale fulfillment centers utilize AS/RS robots to manage inventory and automate order picking. This system allows the company to handle millions of orders daily with remarkable speed and accuracy, highlighting how AS/RS can revolutionize warehouse operations.
4. Mobile Shelving Systems
Mobile shelving systems consist of movable racks mounted on tracks. These shelves can be compressed or expanded based on needs, maximizing storage space in smaller warehouses. Unlike fixed racking systems, mobile shelving reduces unused aisle space by allowing shelves to slide together when access is not needed.
Advantages:
-
Space-saving solution.
-
Provides flexibility in small or medium-sized warehouses.
Disadvantages:
-
Limited weight capacity compared to fixed racking systems.
-
May require manual or semi-automated control to operate the shelving.
5. Mezzanine Flooring
Mezzanine floors are raised platforms installed above the warehouse floor, effectively doubling the storage space without expanding the building’s footprint. These floors can be used for storing goods, creating additional work areas, or installing office spaces within the warehouse.
Advantages:
-
Maximizes vertical storage space.
-
Cost-effective solution for expanding storage without relocation.
Disadvantages:
-
Requires structural support, increasing installation complexity.
-
May not be suitable for heavy loads without reinforcement.
6. Vertical Lift Modules (VLMs)
Vertical Lift Modules (VLMs) are automated storage systems that use vertical space to store goods in trays. When an item is needed, the system retrieves the tray and delivers it to the operator at a pick station, reducing the need for workers to move through the warehouse. VLMs are ideal for storing small to medium-sized items.
Advantages:
-
Reduces the warehouse footprint by utilizing vertical space.
-
Increases picking accuracy and speed.
Disadvantages:
-
Limited to smaller or medium-sized products.
-
High upfront investment costs.
7. Multi-Tier Racking Systems
Multi-tier racking is a high-density storage solution that uses multiple levels of shelving to maximize vertical storage space. This system is particularly effective in warehouses with high ceilings, as it allows workers to access different levels using stairs or lifts.
Advantages:
-
Excellent for maximizing storage in tall warehouses.
-
Ideal for manual picking operations.
Disadvantages:
-
May be less efficient for large, heavy items.
-
Requires additional safety measures for workers operating at heights.
8. Temperature-Controlled Storage Solutions
Temperature-controlled storage is essential for industries that handle perishable goods, such as food, pharmaceuticals, and chemicals. These warehouses are equipped with refrigeration, freezing, or climate control systems to maintain the integrity of the stored products.
Advantages:
-
Maintains the quality and safety of temperature-sensitive products.
-
Essential for meeting regulatory standards in industries like food and healthcare.
Disadvantages:
-
High operational costs due to energy consumption.
-
Requires specialized equipment and monitoring systems.
Conclusion
Modern warehousing storage solutions offer a wide range of options to suit different industries and operational needs. From high-density pallet racking to advanced automation systems, these technologies help warehouses improve efficiency, optimize space, and reduce costs. Choosing the right solution depends on factors like the type of goods being stored, the warehouse layout, and the business’s long-term operational goals.
As technology continues to evolve, warehouses are becoming smarter, faster, and more efficient, allowing businesses to meet growing consumer demands while maintaining control over their supply chain. By investing in the right warehousing solutions, companies can future-proof their operations and stay competitive in today’s dynamic market.
What's Your Reaction?
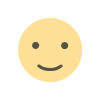
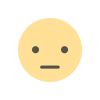
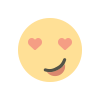
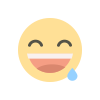
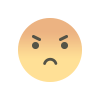
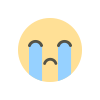
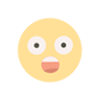