How to Use Predictive Maintenance to Maximize Equipment
In the industrial landscape, maximizing equipment uptime is essential for operational efficiency and profitability. Equipment downtime not only disrupts production schedules but also incurs significant costs in repairs, replacements, and lost revenue.
For industries such as construction, where equipment reliability directly impacts project timelines and overall success, the ability to maintain equipment in optimal condition is crucial. High uptime ensures that machinery is always available when needed, reduces the risk of delays, and supports smoother project execution.
This blog will delve into how predictive maintenance can be effectively utilized to maximize equipment uptime. We will explore the core concepts of predictive maintenance, how to implement it, and how to leverage data for creating effective maintenance schedules.
Additionally, we will discuss how predictive maintenance enhances equipment reliability and provide actionable insights to help you integrate this strategy into your operations.
Predictive Maintenance
Predictive maintenance is a maintenance strategy that uses real-time data and predictive analytics to forecast equipment failures and schedule maintenance activities accordingly.
Unlike reactive maintenance, which addresses issues only after they arise, or preventive maintenance, which follows a fixed schedule, predictive maintenance aims to identify potential problems before they result in equipment failures. This approach offers several benefits:
- Reduced Downtime: By addressing issues before they cause equipment failure, predictive maintenance minimizes unexpected downtime.
- Cost Savings: Preventative interventions reduce the need for costly emergency repairs and extend equipment lifespan.
- Increased Efficiency: Optimizing maintenance schedules based on actual equipment conditions ensures that maintenance activities are performed only when necessary, improving overall operational efficiency.
How It Works
The principles of predictive maintenance revolve around the collection, analysis, and forecasting of equipment data. Here’s how it works:
- Data Collection: Sensors and monitoring devices collect data on equipment performance, such as temperature, vibration, and wear levels.
- Data Analysis: Advanced analytics and machine learning algorithms process this data to identify patterns and predict potential failures.
- Forecasting: Based on the analyzed data, maintenance needs are forecasted, allowing for timely interventions before issues escalate.
2. Implementing Predictive Maintenance
Assessing Equipment and Needs
To effectively implement predictive maintenance, start by assessing which equipment will benefit most from this strategy. Consider the following factors:
- Criticality: Focus on equipment that is crucial to operations and has a high impact on productivity if it fails.
- Historical Data: Review historical failure data to identify patterns and equipment that frequently experiences issues.
- Usage Patterns: Evaluate how often and intensively equipment is used, as this can influence its likelihood of failure.
Selecting Tools and Technologies
Choosing the right tools and technologies is essential for successful predictive maintenance. Look for:
- Predictive Maintenance Software: Opt for software that integrates seamlessly with your existing systems and provides advanced analytics capabilities.
- Hardware Sensors: Invest in high-quality sensors that accurately measure key performance indicators, such as vibration, temperature, and pressure.
- Integration Capabilities: Ensure that the tools you select can integrate with other systems, such as your construction equipment maintenance software, to provide a unified view of equipment health.
Setting Up Data Collection Systems
Once you have selected your tools and technologies, the next step is to set up data collection systems:
- Install Sensors: Position sensors on critical equipment components to continuously monitor performance metrics.
- Integrate Data Sources: Connect sensors to a central data platform that aggregates information from various sources for comprehensive analysis.
- Establish Data Protocols: Define protocols for data collection, storage, and transmission to ensure consistency and reliability.
3. Leveraging Data for Predictive Maintenance
Collecting and Analyzing Data
Effective predictive maintenance relies on robust data collection and analysis. Follow these steps:
- Gather Data: Collect data from sensors and other monitoring tools, focusing on parameters relevant to equipment health.
- Analyze Data: Use predictive analytics tools to process the data and identify trends, anomalies, and potential failure points.
- Monitor Performance: Continuously monitor equipment performance to detect any deviations from normal operating conditions.
Predictive Analytics Techniques
Predictive analytics techniques enhance the accuracy of maintenance forecasts. Some key methods include:
- Machine Learning: Machine learning algorithms can analyze large volumes of data to identify patterns and predict equipment failures with high precision.
- Statistical Models: Statistical models use historical data to forecast future equipment behavior and maintenance needs.
- Trend Analysis: Analyze trends in equipment performance data to predict potential issues based on historical patterns.
Interpreting Predictive Insights
Once data is analyzed, it’s crucial to interpret the insights correctly:
- Identify Potential Failures: Determine which equipment components are likely to fail based on predictive analytics.
- Prioritize Actions: Prioritize maintenance activities based on the severity and likelihood of predicted failures.
- Make Informed Decisions: Use insights to schedule maintenance, order parts, and allocate resources effectively.
4. Creating Effective Maintenance Schedules
Scheduling Based on Predictions
Develop maintenance schedules that align with predictive insights:
- Use Predictive Data: Schedule maintenance tasks based on the predicted condition of equipment, ensuring interventions occur before failures.
- Optimize Timing: Align maintenance activities with equipment usage patterns to minimize disruption to operations.
Adjusting Schedules Dynamically
Maintain flexibility in your maintenance schedules:
- Real-Time Adjustments: Adjust maintenance schedules dynamically based on real-time data and changing equipment conditions.
- Respond to Anomalies: Be prepared to modify schedules if unexpected issues arise or if predictive data indicates a higher likelihood of failure.
Integrating with Existing Maintenance Plans
Seamlessly integrate predictive maintenance schedules with existing maintenance practices:
- Combine Strategies: Blend predictive maintenance with preventive and corrective maintenance approaches for a comprehensive maintenance strategy.
- Coordinate Resources: Ensure that maintenance teams, parts, and tools are coordinated effectively to support both predictive and routine maintenance activities.
5. Enhancing Equipment Reliability through Predictive Maintenance
Minimizing Unexpected Downtime
Predictive maintenance helps in avoiding unplanned equipment failures by:
- Early Detection: Identifying potential issues before they lead to equipment breakdowns.
- Timely Interventions: Performing maintenance activities at the optimal time to prevent failures and minimize downtime.
Improving Equipment Longevity
Regular, data-driven maintenance extends the lifespan of equipment by:
- Preventing Wear and Tear: Addressing issues before they cause significant damage or deterioration.
- Optimizing Performance: Ensuring equipment operates at peak efficiency, reducing strain and prolonging its useful life.
Optimizing Maintenance Resources
Predictive maintenance enables more efficient use of resources by:
- Reducing Emergency Repairs: Minimizing the need for costly and disruptive emergency repairs.
- Enhancing Resource Allocation: Allocating maintenance resources more effectively based on predictive insights.
Conclusion
In summary, predictive maintenance is a powerful strategy for maximizing equipment uptime by leveraging real-time data and advanced analytics.
By understanding and implementing predictive maintenance, analyzing data effectively, creating responsive maintenance schedules, and enhancing equipment reliability, organizations can achieve significant improvements in operational efficiency and cost savings.
Investing in predictive maintenance is a forward-thinking approach that can dramatically enhance equipment reliability and operational efficiency. Embracing this strategy will help you avoid costly downtime, extend equipment lifespan, and optimize maintenance efforts.
What's Your Reaction?
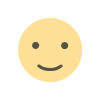
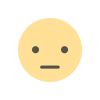
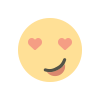
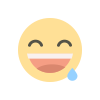
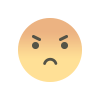
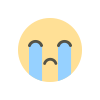
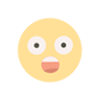