How Powder Metallurgy Is Transforming Automotive, Aerospace and Medical Sectors
Powder metallurgy is transforming manufacturing across industries like automotive, aerospace, and medical technology. This innovative process enables the production of complex components with greater precision and efficiency than traditional methods. From lightweight, durable engine parts to biocompatible medical implants, powder metallurgy is solving critical challenges and driving advancements in modern technology.
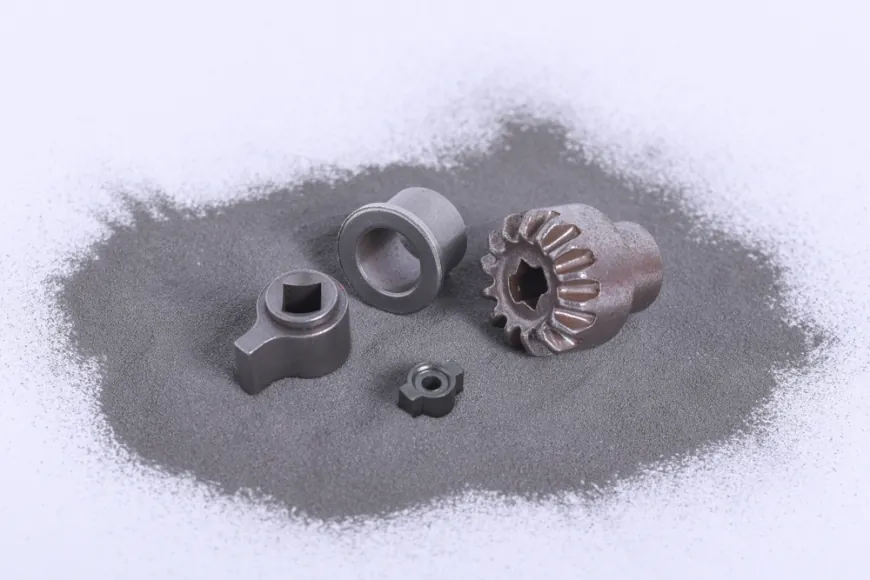
A thousand-year-old metalworking technique is now reinventing manufacturing across automotive, aerospace, medical technology, and electronics. Powder metallurgy is enabling these industries to create complex alloys and micro-precision components unmatched by conventional methods. This press release explores how modern powder metallurgy is solving previously insurmountable challenges.
Powder Metallurgy combines fine metallic powders into three-dimensional shapes through molding and low-temperature heat treatment. This green approach consumes just 3% of raw materials versus metalcasting's 70% loss rate. It also skips energy-intensive melting and machining steps. The result is high-performance engine parts, space-grade alloys, biocompatible implants and micro-scale electronics produced at a fraction of standard costs.
Though the basic principles date back to ancient Mesopotamia, Egypt and China, recent innovations have unlocked game-changing applications. For instance, vacuum sintering now creates complex gears with minimal distortion. Advanced pneumatic presses generate compacting pressures over 4 tons per square inch to form intricate shapes. This enables miniaturized biomedical components and electronics previously impossible through metalworking or 3D printing.
Automakers extensively use powder metallurgy for quieter, lighter and stronger engine parts.The excellent dimensional precision reduces gear backlash and transmission noises. Iron-copper powders form high-strength bearings that withstand extreme heat and loads. Powder steel valve guides resist corrosion and wear from high-speed exhaust gases.
In aerospace applications, specialized nickel and titanium alloys resist intense aeroengine stresses. Turbine discs made from these powders withstand blistering temperatures exceeding 1,600°F. Powder metallurgy also produces landing gear gears and bearings with the impact resistance needed for heavy commercial jets. Even high-performance Formula 1 brakes leverage powder metals for rapid heat dissipation during intense braking.
Powder metallurgy further enables personalized medical implants like replacement hip joints. Biocompatible cobalt-chromium powders are compressed into complex porous structures. This allows living bone and tissue to integrate with the implant for natural-feeling joints. Additive manufacturing takes this further by using powders to 3D print titanium knee replacements tailored to a patient's anatomy.
For electronics, powder metallurgy creates intricately shaped copper and silver conductors for smartphones and computers. Miniature iron antenna cores are manufactured with thin walls impossible through machining. Soft magnetic composites made from iron-silicon powders are now replacing heavy transformer cores. This allows smaller, lighter power adapters and chargers.
While metal 3D printing has its niche uses, powder metallurgy dominates industrial production volumes thanks to lower costs and higher performance. Parts combining a dozen exotic alloys are feasible. Short-runs as low as 10,000 units are economical. With costs dropping and capabilities rising, powder metallurgy will disrupt casting and machining processes that dominated manufacturing for over a century.
The future potential is great since powder metallurgy integrates with additive manufacturing, automation and advanced materials. Previously unattainable applications are now within reach. Advances in powder production allow more alloys previously restricted by solubility issues or segregation. Mechanical alloying techniques now synthesize a wider range of metal, intermetallic, and composite powders.
Materials like magnesium, aluminum, and titanium alloys become more accessible for powder metallurgy applications through such methods. Industries that harness these advances will gain decisive competitive advantages. Otherwise, they will not adapt.
What's Your Reaction?
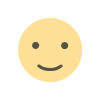
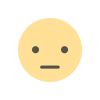
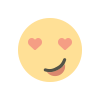
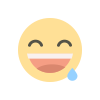
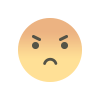
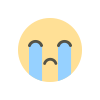
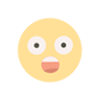