A Deep Dive into PP Jumbo Bags: Versatile Solutions for Bulk Packaging
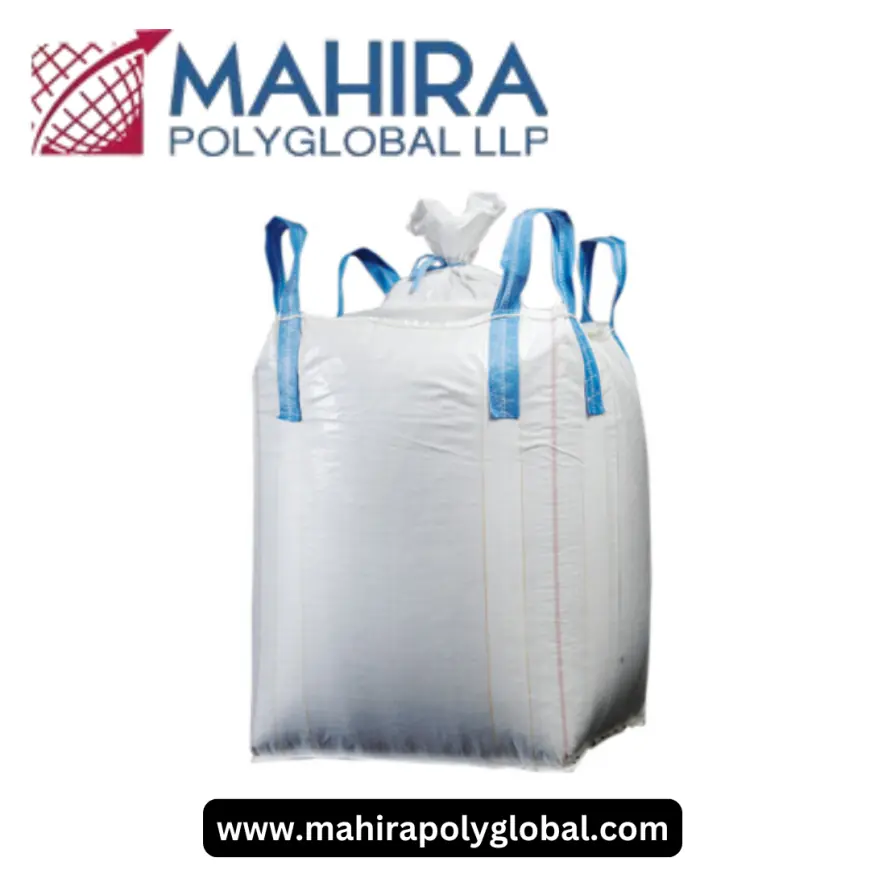
Introduction to PP Jumbo Bags
PP (polypropylene) jumbo bags have revolutionized the way industries approach bulk packaging and storage. These versatile bags, also known as big bags or flexible intermediate bulk containers (FIBCs), are primarily used for transporting and storing a wide range of materials, from agricultural products to construction materials. Often capable of carrying loads ranging from 500 kg to 2,000 kg, PP jumbo bags are designed to provide robust protection while being lightweight and cost-effective. Their durable construction makes them a preferred choice for many sectors, such as agriculture, food processing, chemicals, and manufacturing, where bulk handling is essential.
One of the leading players in the production of these bags are jumbo bag manufacturers in India. India’s vast agricultural landscape and growing industrial sector significantly contribute to the rising demand for Mahira Polyglobal LLP leading to an expansion in local manufacturing capabilities. As businesses seek efficient solutions to manage large quantities of materials, the role of these manufacturers becomes increasingly important in facilitating trade and enhancing operational efficiency.
Key Features and Benefits of PP Jumbo Bags
PP jumbo bags are engineered to address the specific needs of bulk transport and storage. Their notable features start with their exceptional strength. Made from woven polypropylene, these bags can withstand significant stress without breaking, unlike traditional packaging materials. This inherent strength is crucial when loading heavy materials, as it reduces the risk of tears or leaks during transit.
Another significant advantage lies in their weight-to-strength ratio. While providing remarkable durability, PP jumbo bags remain lightweight, helping to minimize shipping costs. Their design often includes features such as spouts for easy filling, discharge openings, and various base styles (like flat or cone-shaped), enhancing their versatility. Additionally, the bags can be customized in terms of size, color, and printing, allowing companies to tailor their packaging solutions to fit their branding and operational needs.
Importantly, PP jumbo bags are resistant to moisture and chemicals, which is particularly beneficial when storing items that may be affected by environmental factors. Waterproofing and UV stabilization can be integrated into the production process, making these bags suitable for diverse applications, from storing grains in agricultural settings to transporting hazardous materials in industrial environments.
Applications Across Diverse Industries
The applicability of Plastic big bag spans a multitude of industries. In agriculture, these bags are widely utilized for bulk storage of grains, seeds, fertilizers, and animal feed. Their breathable properties help to maintain product quality by allowing necessary ventilation while preventing moisture damage. This is vital for farmers and agricultural businesses aiming to store products for extended periods without spoilage.
In the construction industry, big bags plastic serve a vital role in safe transportation and storage. Materials such as sand, gravel, and cement are typically loaded into these bags, which are engineered to withstand harsh handling during transport. Their robust design minimizes the risk of ruptures or spills on construction sites, thereby facilitating smoother operations.
Furthermore, the food processing industry increasingly relies on PP jumbo bags for bulk transportation of food items like sugar, flour, and rice. Food-grade ratings ensure compliance with health regulations, making them a safe option for food handling. The chemical industry also benefits from these bags, using them to package various powders and granular materials while maintaining stringent safety standards.
The Growing Presence of Jumbo Bag Manufacturers in India
As the demand for PP jumbo bags continues to rise, India has emerged as a prominent hub for bags manufacturers in India. The country's manufacturing ecosystem is robust, characterized by skilled labor, competitive pricing, and a growing focus on quality and sustainability. Major manufacturers are constantly optimizing their production methods to ensure that their bags meet international standards while remaining affordable for local and global markets.
These manufacturers have begun to embrace innovative technologies to enhance production efficiency. Automation and advanced weaving techniques enable them to manufacture high-quality bags at a larger scale, reducing costs and time. Additionally, many manufacturers are focusing on sustainability by incorporating recycled materials into their production processes. This dedication to environmental responsibility aligns with global trends favoring eco-friendly practices, thus ensuring market relevance.
Moreover, the customization offerings of these manufacturers are expanding, with businesses able to specify sizes, colors, and other unique features according to their specific needs. This ability to personalize the product enhances brand recognition and provides logistical advantages as businesses navigate complex supply chains.
Ensuring Quality and Compliance in Production
Quality control is paramount for Jumbo bag weight, particularly because these bags are used across industries where safety is critical. Reputable manufacturers implement stringent quality assurance protocols to ensure every bag produced meets necessary safety and performance standards before reaching the market. These protocols often include rigorous testing for strength, durability, and load-bearing capacity.
Certification and compliance with international standards are also crucial for manufacturers seeking to expand their market reach. Obtaining certifications such as ISO ensures that the production processes align with global quality benchmarks, fostering trust among consumers and businesses alike. Regulations surrounding packaging materials, particularly for food safety, require bags to meet strict criteria. Manufacturers often collaborate closely with clients to ensure they meet all necessary guidelines and specifications.
In addition to traditional quality checks, manufacturers are employing new technologies, such as real-time monitoring systems, to track the quality of their products throughout the production process. This not only enhances product safety but also bolsters the overall efficiency of production lines.
Emerging Trends Transforming the PP Jumbo Bag Market
As the packaging industry continues to evolve, several key trends are emerging that will reshape the future of PP jumbo bags. One of the most notable trends is the increasing adoption of automation in manufacturing processes. Automating production lines not only improves efficiency but also enhances precision and reduces human error, translating to consistent product quality.
Sustainability remains a pivotal theme in the industry. With rising awareness of environmental issues, bag manufacturers are investing in research to develop biodegradable and compostable alternatives to traditional polypropylene. This shift is essential in meeting growing consumer demands for sustainable products and complying with tightening regulations regarding plastic use.
Technological advancements also play a significant role in the integration of the Internet of Things (IoT) into packaging solutions. Smart packaging systems are emerging, incorporating features like QR codes or RFID tags to enable real-time tracking of shipments. This trend is particularly beneficial in the logistics and supply chain sectors, enhancing transparency and boosting efficiency.
Finally, the increasing interplay between packaging and e-commerce is transforming how PP jumbo bags are utilized. As online shopping continues to rise, manufacturers must adapt their products to accommodate the logistical challenges associated with shipping large quantities of goods to individual consumers.
Conclusion
The PP woven jumbo bags have become indispensable in bulk packaging, offering unique solutions for various industries dealing with large quantities of materials. Their robust design, customization options, and cost-effectiveness make them an appealing choice for agricultural, industrial, and commercial applications. As jumbo bag manufacturers in India continue to innovate and prioritize sustainable practices, the future of these packaging solutions looks promising. The capacity for further development in quality control, automation, and eco-friendly alternatives ensures that PP jumbo bags will remain integral to efficient supply chains and logistics for years to come.
Frequently Asked Questions
1. What materials are PP jumbo bags made from?
PP jumbo bags are primarily made from woven polypropylene, a strong and lightweight plastic. This material provides durability and resistance to many chemicals and environmental factors, making these bags suitable for diverse applications.
2. How can I determine the appropriate size of a jumbo bag for my needs?
The size of a jumbo bag depends on the volume and weight of the materials you need to store or transport. Manufacturers offer various sizes, so it's best to consult with them to choose a bag that meets your specific requirements.
3. Are there biodegradable options available in the market?
Yes, many manufacturers are exploring and developing biodegradable and compostable alternatives to traditional polypropylene jumbo bags. This effort aligns with growing consumer demand for sustainable packaging solutions.
4. How do I maintain the quality of PP jumbo bags during storage?
To maintain the quality of PP jumbo bags during storage, keep them in a dry, cool place away from direct sunlight and extreme temperatures. Ensure they’re stored away from sharp objects or potential hazards that could cause tears or punctures.