Manufacturing Process of EN 10217-1 P235TR1 Pipe
The manufacturing process of EN 10217-1 P235TR1 pipes involves a combination of precision engineering, rigorous quality control, and advanced technology.
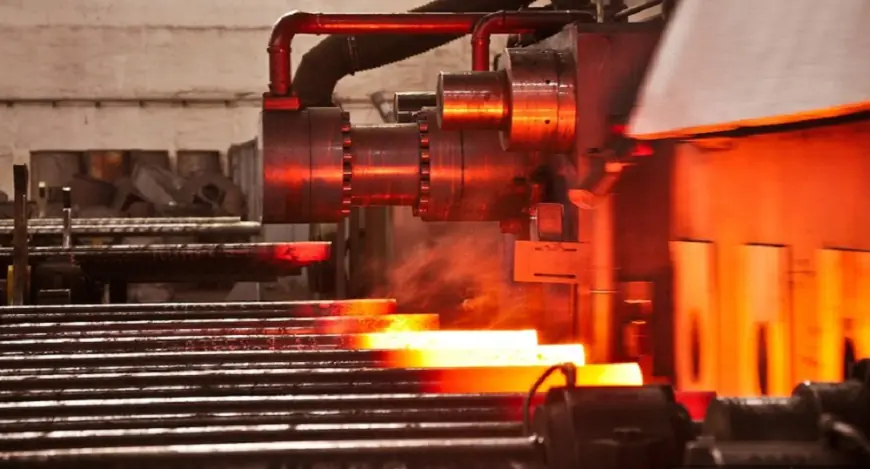
The manufacturing process of EN 10217-1 P235TR1 pipes begins with carefully selecting high-quality raw materials. Non-alloy steel billets or slabs are the base material chosen for their uniform chemical composition and mechanical properties. The materials comply with stringent standards to ensure the final pipes meet the desired pressure-bearing and corrosion resistance specifications.
Heating and Forming
The selected steel undergoes a heating process in a furnace to achieve the required malleability for forming. Once heated to the appropriate temperature, the steel is shaped into a cylindrical form. In most cases, this is achieved using a rolling mill or forming dies, which convert the flat steel into a tubular shape. The forming method depends on the pipe's desired dimensions and application.
The steel is rolled into a cylindrical shape for longitudinally welded pipes, and the edges are prepared for welding. This stage ensures the pipe maintains uniform wall thickness and proper dimensional accuracy.
Welding Process
Welding plays a critical role in manufacturing EN 10217-1 P235TR1 pipe. The edges of the formed steel are welded together using a high-frequency induction welding (HFIW) or electric resistance welding (ERW) process. These methods create a strong, seamless joint along the pipe's longitudinal axis.
To ensure the integrity of the weld, manufacturers subject the pipe to non-destructive testing (NDT), such as ultrasonic testing or radiography. These tests confirm the absence of defects like cracks, voids, or inclusions in the weld seam.
Heat Treatment
After welding, the pipes undergo heat treatment to enhance their mechanical properties and relieve internal stresses. Depending on the application requirements, the heat treatment process typically involves normalizing or stress relieving. During normalizing, the pipe is heated to a specific temperature and then cooled in air, ensuring a uniform microstructure and improved toughness.
This step ensures that the pipes comply with the requirements of the EN 10217-1 standard, particularly in terms of tensile strength, impact resistance, and flexibility.
Sizing and Shaping
Once heat treatment is complete, the pipe is passed through a series of sizing and shaping rollers to achieve the desired dimensions. This step ensures that the outer diameter, wall thickness, and length are consistent with the specifications for P235TR1 pipes. Additionally, the edges and ends of the pipe are trimmed to achieve a smooth finish, facilitating ease of installation in pressure systems.
Testing and Inspection
Every EN 10217-1 P235TR1 pipe undergoes rigorous testing to verify its quality and performance. Hydrostatic pressure testing ensures the pipe can withstand the specified internal pressure without leaks or deformations. Mechanical tests, such as tensile and impact testing, verify that the pipe meets the required strength and toughness standards.
Dimensional checks and visual inspections are also conducted to confirm that the pipe meets the required tolerances and has no surface defects. These inspections ensure that the pipes adhere to both customer and regulatory requirements.
Surface Treatment and Coating
After inspection, the pipes are subjected to surface treatments to enhance their resistance to corrosion and environmental damage. That may include picking, phosphating, or coating with a protective layer. The choice of surface treatment depends on the pipe's intended application and operating environment.
Final Packaging and Dispatch
The finished EN 10217-1 P235TR1 pipes are marked with essential details such as material grade, size, and manufacturer information. They are then packaged securely to prevent damage during transportation. Pipes are bundled or placed in protective wrappings for delivery to industries such as oil and gas, construction, and power generation.
What's Your Reaction?
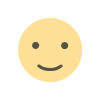
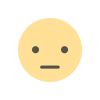
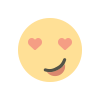
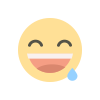
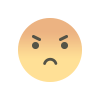
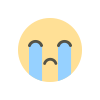
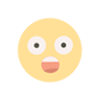