The Role of Automation in Modern Packaging: Insights from Indian Manufacturers
About The Role of Automation in Modern Packaging: Insights from Indian Manufacturers

Automation is reshaping the landscape of the packaging industry, particularly in India, where manufacturers are increasingly adopting advanced technologies to enhance productivity and efficiency. This blog explores the role of automation in modern packaging, focusing on insights from Indian manufacturers through nine key points.
Understanding Automation in Packaging
Automation in packaging refers to the use of technology to perform tasks with minimal human intervention. This includes processes such as filling, sealing, labeling, and palletizing. By integrating robotics and artificial intelligence (AI), packaging operations can be streamlined, leading to faster production times and reduced labor costs.The shift towards automation allows manufacturers to meet increasing consumer demands for speed and efficiency. With automated systems, companies can achieve consistent quality in their packaging processes while minimizing the risk of human error. This is particularly important in industries like food and beverages, pharmaceuticals, and cosmetics, where precision is crucial.
Furthermore, automation not only increases production speed but also enhances safety in the workplace. By taking over repetitive and physically demanding tasks, automated systems reduce the risk of injuries associated with manual labor. As a result, employees can focus on more strategic roles within the organization, contributing to overall productivity while maintaining a safer work environment. Additionally, automated systems can operate continuously without breaks, further maximizing output and minimizing downtime during production cycles.
Key Components of Automated Packaging Systems
Automated packaging systems consist of several key components that work together to enhance efficiency. These include filling machines, sealing machines, labeling machines, wrapping machines, and palletizing systems. Each component plays a vital role in ensuring that products are packaged quickly and accurately.
For instance, automated fillers can dispense liquids or powders into containers with precise measurements, reducing waste and improving product quality. Similarly, automated labelling machines apply labels consistently across products, ensuring compliance with regulations and enhancing brand visibility. By investing in these components, Indian packaging machine manufacturers can significantly improve their operational capabilities.
Increased Efficiency and Speed
One of the most significant benefits of automation in packaging is the increase in efficiency and speed. Automated systems can operate at a much faster pace than manual processes, allowing manufacturers to handle larger volumes of products without bottlenecks.
According to industry reports, automation can lead to productivity increases of up to 30%. This heightened efficiency not only accelerates production but also enables companies to respond more quickly to market demands. As a result, businesses can reduce lead times and improve customer satisfaction by delivering products faster.
Cost Savings Through Automation
While the initial investment in automated packaging systems may be substantial, the long-term cost savings are substantial. Automation reduces operational costs by minimizing labor expenses and decreasing material waste through precise handling.
Automated systems are designed to optimize resource usage, ensuring that every aspect of the packaging process is as efficient as possible. For example, accurate filling machines prevent overfilling or spillage, which can lead to significant savings over time. As Indian manufacturers adopt these technologies, they find that automation not only enhances their bottom line but also allows them to remain competitive in a rapidly evolving market.
Improved Accuracy and Quality Control
Automation enhances accuracy and quality control throughout the packaging process. Automated systems are programmed to follow exact specifications, which reduces errors during filling, sealing, and labelling. Incorporating automated inspection systems ensures that any defects or inconsistencies are identified in real-time. This proactive approach to quality control helps maintain high standards for products while reducing the likelihood of costly recalls or rework. By prioritizing accuracy through automation, Indian packaging machine manufacturers can build trust with their clients and consumers alike.
Enhanced Safety for Workers
The implementation of automation in packaging not only boosts productivity but also enhances workplace safety. By taking over repetitive and potentially hazardous tasks, automated systems reduce the risk of injury among workers.
For example, robotic arms can handle heavy lifting or intricate assembly tasks that would otherwise pose risks to human operators. This shift allows employees to focus on more strategic roles within the organization while ensuring a safer work environment overall. As safety becomes a priority for many companies, automation serves as a valuable tool for improving employee well-being.
Scalability and Flexibility
Modern automated packaging systems offer scalability and flexibility that traditional methods cannot match. As businesses grow or change their product lines, automated systems can often be reconfigured or upgraded without significant downtime.
This adaptability is crucial for manufacturers looking to respond quickly to market trends or consumer preferences. For instance, Indian packaging machine manufacturers can easily adjust their operations to accommodate seasonal demands or new product launches by leveraging automated technologies effectively.
The Role of Data Analytics
Data analytics plays an increasingly important role in modern packaging automation. Automated systems equipped with sensors collect vast amounts of data during production processes, providing valuable insights into performance metrics.
By analyzing this data, manufacturers can identify trends and inefficiencies within their operations. This information enables them to make informed decisions about process improvements and resource allocation. As data-driven decision-making becomes more prevalent in the industry, Indian manufacturers are better positioned to optimize their operations through continuous improvement initiatives.
Future Trends in Packaging Automation
Looking ahead, several trends are likely to shape the future of packaging automation in India. The integration of advanced technologies such as artificial intelligence (AI), machine learning (ML), and the Internet of Things (IoT) will further enhance automation capabilities.
These technologies will enable smarter packaging solutions that adapt to real-time conditions and consumer preferences while providing greater connectivity across supply chains. As these trends continue to evolve, packaging machine manufacturers in India will need to stay ahead by investing in innovative solutions that meet changing market demands.
Conclusion
In conclusion, automation is playing a transformative role in modern packaging processes across India. By understanding its significance—from increased efficiency and cost savings to improved safety and scalability—manufacturers can leverage these advancements effectively. Embracing automation not only enhances operational capabilities but also positions Indian companies as leaders in a competitive global market for packaging machinery.
What's Your Reaction?
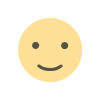
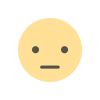
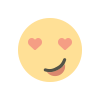
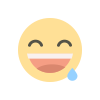
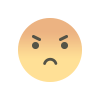
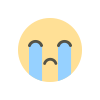
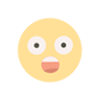