Standardisation Testing and Quality Certification
Discover Standardisation Testing and Quality Certification (STQC) services ensuring product reliability, compliance, and quality assurance. We offer testing, calibration, IT & e-Governance support to meet global standards. Enhance trust with certified excellence
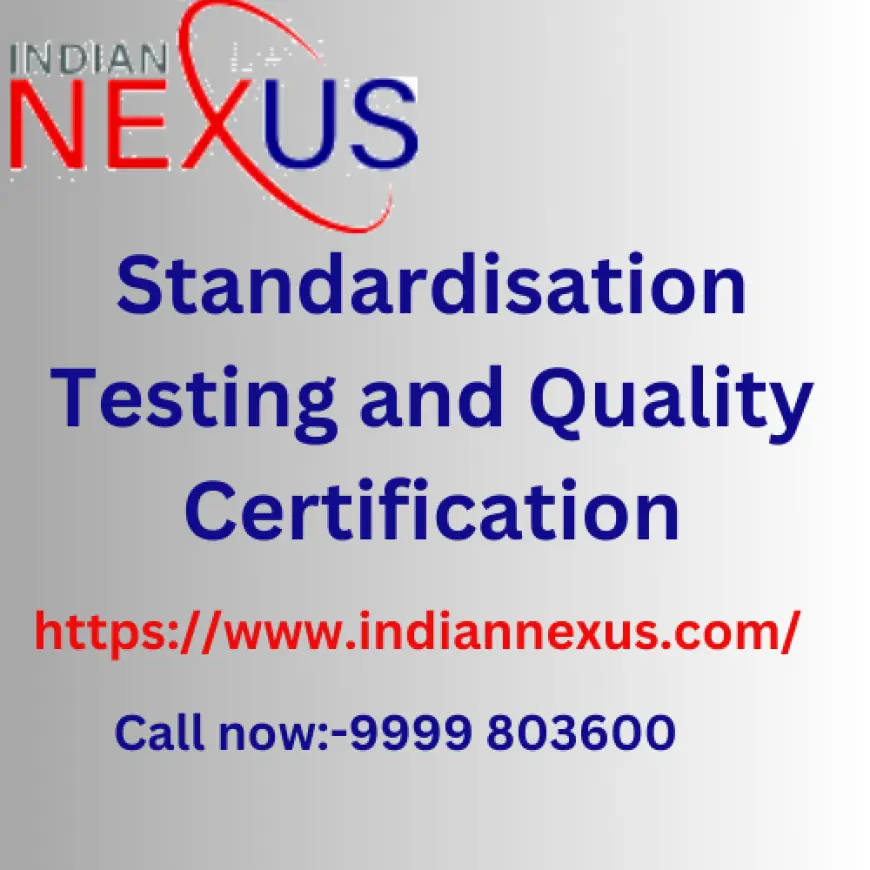
Standardisation Testing and Quality Certification
Standardisation is the process of developing and implementing technical standards to ensure consistency, safety, and efficiency in products, services, and systems. These standards can be established at various levels, including international, national, and industry-specific guidelines. Organizations such as the International Organization for Standardization (ISO), Bureau of Indian Standards (BIS), and American National Standards Institute (ANSI) play a pivotal role in setting these standards.
The primary objectives of Standardisation, Testing, and Quality Certification include:
-
Enhancing interoperability between products and services.
-
Ensuring consumer safety and environmental sustainability.
-
Facilitating global trade by eliminating technical barriers.
-
Encouraging innovation and best practices within industries.
Standardisation provides a uniform benchmark that businesses and consumers can rely on. It ensures that a product or service meets a specific set of guidelines, reducing variability and increasing predictability in various industries, including manufacturing, healthcare, electronics, and more.
The Role of Testing in Quality Assurance
It involves the systematic examination of products, materials, or services to determine whether they meet predefined standards and requirements. Various testing methodologies are employed depending on the nature of the product and the industry it serves.
Types of Testing
-
Performance Testing – Evaluates the functionality and efficiency of a product under different conditions.
-
Safety Testing – Ensures that a product does not pose any harm to consumers or the environment.
-
Durability Testing – Determines the lifespan and robustness of a product under stress conditions.
-
Compliance Testing – Verifies that a product adheres to regulatory standards and guidelines.
-
Environmental Testing – Assesses how a product performs under extreme environmental conditions.
-
Material Testing – Examines the chemical, physical, and mechanical properties of materials used in manufacturing.
Testing laboratories play a significant role in the Standardisation, Testing, and Quality Certification process. These laboratories are often accredited by recognized bodies such as the International Laboratory Accreditation Cooperation (ILAC) and National Accreditation Board for Testing and Calibration Laboratories (NABL), ensuring that testing procedures adhere to globally accepted methodologies.
The Importance of Quality Certification
Quality Certification is the formal recognition that a product, process, or service meets established quality standards. It is granted by certification bodies after a thorough evaluation and testing process. Some of the most recognized quality certifications worldwide include:
-
ISO 9001 – Quality Management Systems
-
ISO 14001 – Environmental Management Systems
-
ISO 45001 – Occupational Health and Safety Management Systems
-
CE Marking – Compliance with European safety and health regulations
-
BIS Certification – Indian quality certification for various products
-
FDA Approval – U.S. Food and Drug Administration certification for medical and food products
Quality certification provides numerous benefits to businesses, including:
-
Increased Consumer Trust: Consumers are more likely to purchase products that carry recognized quality certification marks.
-
Market Competitiveness: Certified products have an edge in global and domestic markets.
-
Regulatory Compliance: Helps businesses adhere to legal and industry-specific regulations.
-
Operational Efficiency: Encourages companies to adopt best practices and optimize processes.
-
Reduction in Defects and Recalls: Ensures that products meet quality benchmarks, minimizing defects and potential recalls.
The Process of Standardisation, Testing, and Quality Certification
The Standardisation, Testing, and Quality Certification process typically follows these key steps:
1. Development of Standards
Industry experts, regulatory bodies, and stakeholders collaborate to develop standards based on research, technological advancements, and industry needs. These standards are then published by recognized organizations such as ISO, BIS, or ASTM International.
2. Product Testing and Evaluation
Manufacturers submit their products to accredited testing laboratories, where they undergo rigorous evaluations based on predefined criteria. The testing phase ensures that the product meets safety, performance, and compliance standards.
3. Certification Process
Once the product successfully passes testing, a certification body reviews the test reports and compliance documentation. If all requirements are met, the certification is granted, allowing the product to be labeled with the relevant certification mark.
4. Continuous Monitoring and Auditing
Quality certification is not a one-time process. Regular audits and inspections are conducted to ensure continued compliance with standards. Companies must consistently uphold quality assurance practices to maintain their certifications.
The Impact of Standardisation, Testing, and Quality Certification on Industries
Various industries rely on Standardisation, Testing, and Quality Certification to ensure product integrity and consumer safety. Some of the key sectors that benefit from these processes include:
1. Manufacturing
Standardised manufacturing processes ensure uniformity and quality across production lines. Testing helps detect defects early, and certification adds credibility to products, improving marketability.
2. Healthcare and Pharmaceuticals
In the healthcare industry, medical devices and pharmaceutical products must undergo stringent testing and certification to meet safety and efficacy standards. Regulatory bodies such as the FDA and WHO oversee these processes.
3. Electronics and Telecommunications
Electronics and telecommunication equipment must adhere to electromagnetic compatibility (EMC) and safety standards. Certification ensures that devices function properly and do not interfere with other systems.
4. Automotive
Vehicle components and safety systems undergo extensive testing to meet regulatory requirements. Certification ensures that automobiles meet fuel efficiency, emissions, and crash safety standards.
5. Food and Agriculture
Food safety is paramount, and certification programs such as HACCP (Hazard Analysis and Critical Control Points) and FSSAI (Food Safety and Standards Authority of India) help ensure that food products are safe for consumption.
6. Construction and Infrastructure
Building materials and structural components must meet quality and safety standards to ensure the durability and safety of infrastructure projects. Certification bodies assess compliance with industry regulations.
Conclusion
Standardisation, Testing, and Quality Certification are integral to modern industry and commerce. These processes ensure that products and services meet established quality and safety benchmarks, fostering consumer trust and enabling businesses to compete in the global market. By adhering to these frameworks, industries can enhance efficiency, minimize risks, and contribute to overall economic growth.