PE Film: The Versatile Solution Transforming Packaging Across Industries
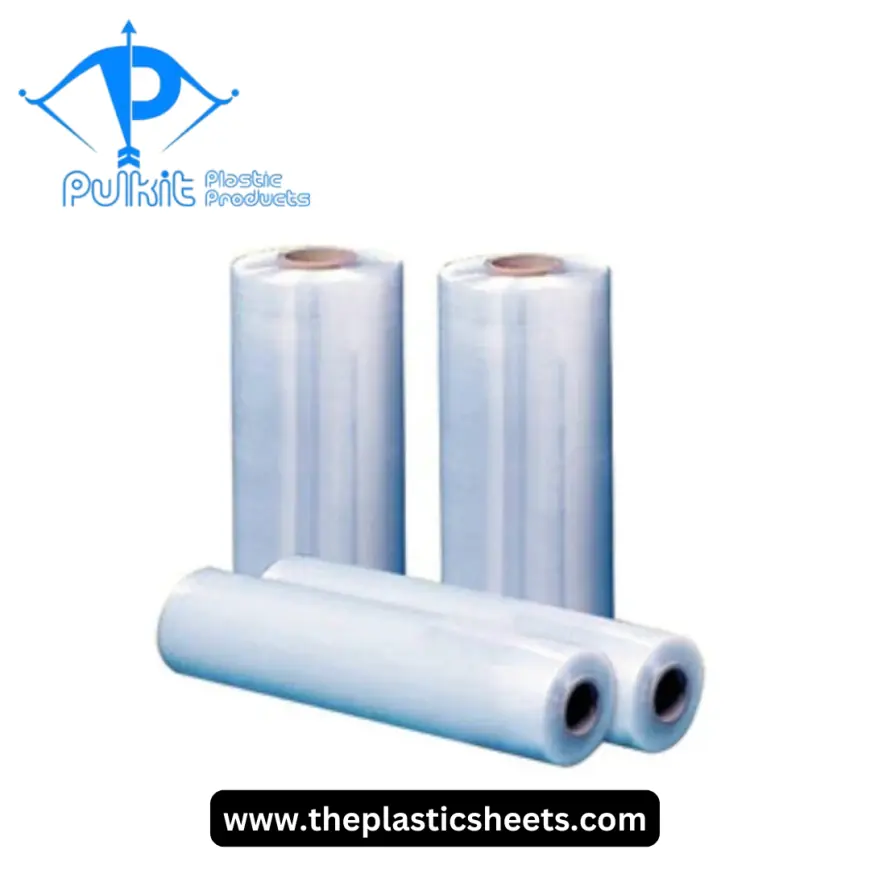
Polyethylene (PE) film has transformed the packaging industry and multiple sectors due to its unique properties and versatility. As one of the most commonly used plastics, PE film is known for its lightweight nature, durability, and resistance to moisture, making it suitable for a variety of applications. From agriculture to food packaging, the importance of high-quality PE films cannot be overstated. In this Pulkit Plastic Products, we will explore the characteristics, types, manufacturing processes, and applications of PE films, shedding light on the role of PE film suppliers and PE film manufacturers in various industries.
The Composition and Types of PE Film
PE film is composed primarily of polyethylene, a thermoplastic polymer made from the polymerization of ethylene. This polymer can be processed into films of varying thicknesses and characteristics to meet specific needs. There are primarily three types of polyethylene films: low-density polyethylene (LDPE), linear low-density polyethylene (LLDPE), and high-density polyethylene (HDPE). Each of these types has distinct properties that make them suitable for different applications.
LDPE is known for its flexibility and softness, making it ideal for applications like grocery bags, shrink wraps, and food packaging. LLDPE, on the other hand, offers enhanced strength and puncture resistance compared to LDPE, making it a popular choice for stretch films and industrial packaging. HDPE is notable for its high tensile strength and rigidity, often used in applications such as containers, bottles, and heavier-duty packaging materials. Understanding the differences among these types is crucial for manufacturers and buyers when choosing the right PE film for their specific requirements.
The Manufacturing Process of PE Film
The PE film manufacturer typically involves several steps, including extrusion, blowing, and cooling. The first step is the extrusion process, where plastic resin is melted down and forced through a die to form a continuous sheet or film. This film can be either cast or blown, depending on the desired thickness and properties.
In blown film extrusion, the molten PE is extruded through a circular die and then inflated to form a bubble that is cooled as it expands. This method allows for a more uniform wall thickness and greater control over the physical characteristics of the film. In contrast, cast film extrusion involves extruding the molten plastic onto a flat surface, where it solidifies into a thin sheet. While both methods are widely used, blown film is often preferred for applications requiring superior barrier properties.
Once the film is formed, it undergoes a cooling process, which helps in solidifying the structure. Subsequent processes like cutting, slitting, or printing can be applied to add functionalities, branding, or other attributes to the final product. The involvement of specialized PE film manufacturers ensures that stringent quality control measures are implemented, resulting in high-quality films.
Properties and Advantages of PE Film
PE films exhibit several advantageous properties that contribute to their widespread use across various industries. Key attributes include excellent chemical resistance, high tensile strength, flexibility, and moisture barrier capabilities. These properties make PE films ideal for applications that require protection against harsh environmental conditions or contamination.
Furthermore, PE films are lightweight, which simplifies handling and helps reduce transportation costs. The flexibility inherent in these films allows for easy conformability to various shapes and surfaces, making them versatile for different packaging needs. Additionally, they can be manufactured to be UV resistant, anti-static, or biodegradable, depending on the specific requirements of the end client.
One of the most significant advantages of PE films is their recyclability. Many PE films can be recycled and reprocessed into new products, contributing to a more sustainable approach in packaging solutions. As environmental concerns continue to rise, the ability to offer recyclable options makes PE film manufacturers increasingly attractive to industry partners seeking green alternatives.
Applications of PE Film Across Industries
The applications of PE film manufacturers are vast and varied, encompassing diverse industries. In the packaging sector, PE films are used for food packaging, shrink wrapping, and palletizing products. The ability to create airtight seals helps preserve freshness and extends shelf life, which is crucial for food-based industries. In agricultural settings, PE films are utilized for greenhouse covers, mulch films, and silage bags, protecting crops and enhancing agricultural productivity.
The automotive and aerospace industries incorporate PE films in protective covers for components during manufacturing and transportation, safeguarding them from damage. Additionally, in medical and pharmaceutical sectors, PE films are utilized for packaging medical devices and products to ensure sterility and safety.
The construction industry has also embraced PE films for moisture barriers in roofing and flooring applications. Their lightweight nature and effective moisture resistance contribute to greater durability in building structures. With such a range of applications, it is evident that PE film suppliers must be well-versed in the needs of different sectors to provide tailored solutions.
The Role of PE Film Suppliers and Manufacturers
The supply chain for PE films is crucial, and it primarily consists of manufacturers who produce the films and suppliers who distribute them. PE film manufacturers play a significant role in ensuring that high-quality films are produced according to industry standards. This involves raw material sourcing, rigorous quality control, and continuous innovation to meet changing market demands.
On the other hand, PE film suppliers act as intermediaries between manufacturers and end-users. They ensure that films are readily available to clients across different industries and provide valuable insights on the latest products or trends in the market. Moreover, suppliers are often responsible for inventory management and logistics, helping businesses minimize lead times for acquiring necessary materials.
As industries evolve and new applications for PE films arise, the collaboration between manufacturers and suppliers will remain vital to meeting customer demands and ensuring quality standards. The growth of e-commerce and online distributions has further shaped how suppliers interact with clients, allowing for streamlined ordering and delivery processes.
Challenges Facing the PE Film Industry
Despite its advantages, the PE film industry also faces challenges that impact manufacturers and suppliers. One of the most pressing concerns is the environmental impact of plastic waste. Although PE films boast recyclability, a significant portion still ends up in landfills or oceans, contributing to plastic pollution and posing risks to ecosystems.
In response, many manufacturers are investing in research and development to create more sustainable alternatives, such as biodegradable films or those made from renewable resources. Additionally, increasing regulations concerning plastic usage and recycling present challenges for manufacturers in meeting compliance and adapting to consumer preferences.
Another challenge is the fluctuating prices of raw materials, often influenced by global oil prices, as polyethylene is derived from petroleum. These fluctuations can affect production costs and, ultimately, the pricing of PE films for consumers. Manufacturers and suppliers must navigate these challenges while remaining competitive in the market.
Conclusion
PE films are a cornerstone of the packaging and manufacturing industries, offering a wide range of applications and functionalities. Their unique properties make them highly desirable for various sectors, contributing to the demand for PE film suppliers and PE film manufacturers. As awareness of sustainability and environmental responsibility grows, the industry is adapting to meet these expectations through innovation and research.
Ultimately, PE film suppliers represents more than just a material; it symbolizes an essential component of modern industrial practices. From agriculture to medical applications, the role of PE films will only continue to expand as technologies develop and consumer preferences evolve, paving the way for a resilient and sustainable future.
Frequently Asked Questions
1. What are the main types of PE films and their applications?
The main types of PE films are low-density polyethylene (LDPE), linear low-density polyethylene (LLDPE), and high-density polyethylene (HDPE). LDPE is often used for grocery bags, LLDPE for stretch films, and HDPE for robust containers and packaging solutions.
2. How are PE films manufactured?
PE films are manufactured through processes such as extrusion, which can be done in blown or cast forms. The molten polyethylene is shaped into films, cooled, and cut to specifications, ensuring high-quality output.
3. Are PE films environmentally friendly?
Many PE films can be recycled, and advancements are being made to create biodegradable options, reducing their environmental impact. However, challenges remain in managing plastic waste and promoting recycling initiatives.
4. What industries benefit from PE film applications?
Industries such as food packaging, agriculture, automotive, medical, and construction utilize PE films. Their versatility and protective qualities make them suitable for a wide range of applications across various sectors.