Mastering the Art of Precision: A Comprehensive Guide to Laser Welding Systems
At the core of a laser welding system is the laser source, which generates the intense, focused beam of light that melts and fuses the materials being joined.
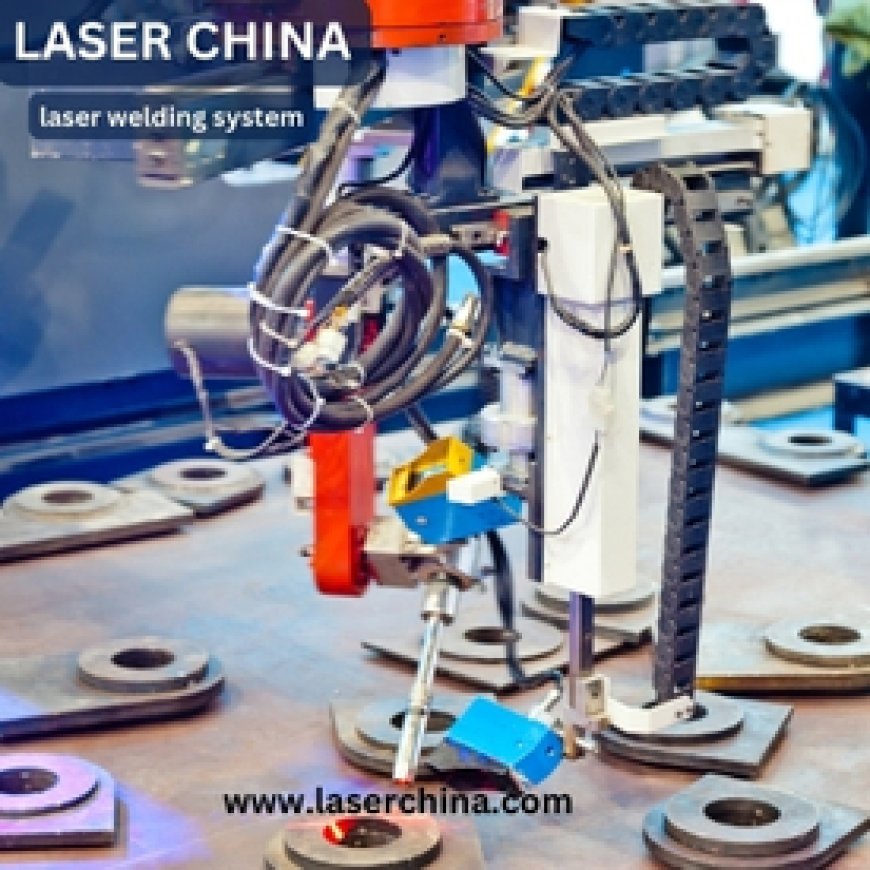
Laser welding systems have revolutionized the manufacturing industry, offering unparalleled precision, efficiency, and versatility. These high-tech tools have become essential for a wide range of applications, from automotive and aerospace to medical and electronics. In this comprehensive guide, we'll explore the key components, principles, and practical considerations of laser welding system, empowering you to harness the power of this cutting-edge technology.
At the core of a laser welding system is the laser source, which generates the intense, focused beam of light that melts and fuses the materials being joined. Common laser types used in welding include CO2, Nd:YAG, and fiber lasers, each with its own unique characteristics and applications. Understanding the specific properties and capabilities of these laser sources is crucial in selecting the right system for your needs.
The laser beam is then directed and controlled using a series of mirrors, lenses, and other optical components, collectively known as the beam delivery system. This system ensures the laser beam is precisely focused and aimed at the desired location on the workpiece. The type of beam delivery system, along with factors like spot size and power density, directly impact the quality and depth of the weld.
Another critical component is the motion control system, which precisely positions the workpiece or the laser beam itself. This enables the creation of complex weld patterns and the ability to weld along intricate paths. Sophisticated computer numerical control (CNC) systems are often integrated into laser welding setups, allowing for automated, repeatable, and highly accurate welds.
Proper shielding and gas supply systems are also essential in laser welding. Inert gases, such as argon or helium, are used to protect the weld pool from atmospheric contamination, ensuring high-quality, defect-free joints. The gas flow rate, composition, and nozzle design all play a role in optimizing the welding process.
When setting up a laser welding system, careful consideration must be given to the workpiece materials, thickness, and joint design. Different materials, such as steel, aluminum, or titanium, may require unique welding parameters, including laser power, beam size, and travel speed. Joint preparation, including proper fit-up and edge preparation, can also significantly impact the weld quality and integrity.
Safety is of paramount importance when working with laser welding systems. Proper personal protective equipment (PPE), including laser-safe goggles and clothing, must be used to mitigate the risks of high-intensity laser radiation. Additionally, the work area should be shielded and ventilated to protect operators from potentially hazardous fumes and spatter.
In conclusion, laser welding system offer a multitude of benefits, including high-speed, high-quality welds, minimal distortion, and the ability to weld dissimilar materials. By understanding the key components, principles, and best practices outlined in this guide, you'll be well-equipped to harness the power of this transformative technology and elevate your manufacturing capabilities.
What's Your Reaction?
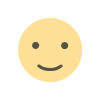
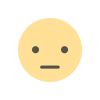
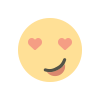
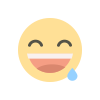
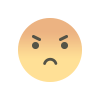
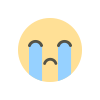
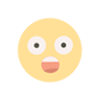