Exploring the Manufacturing Process Behind High-Quality Plywood Products
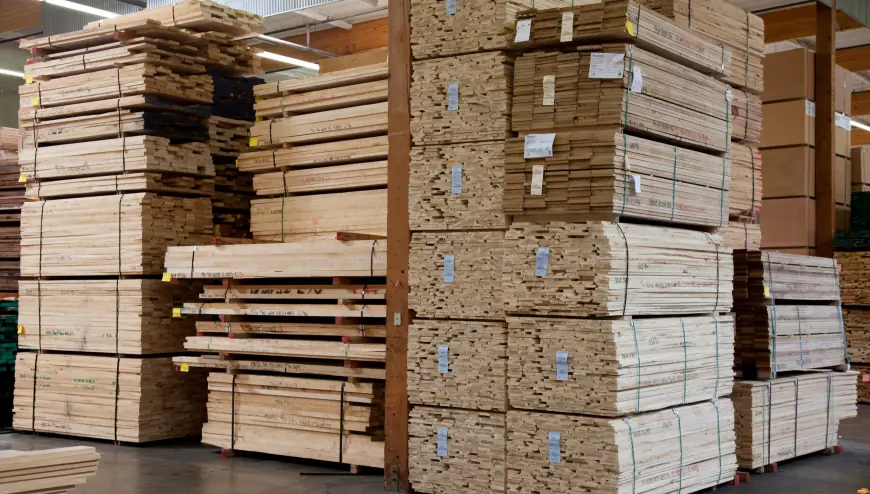
Plywood is a versatile and indispensable material used in various industries, including construction, furniture, and interior design. The production of high-quality plywood requires precision, advanced techniques, and adherence to industry standards.
This blog will take you through the essential steps of the plywood manufacturing process, highlighting the methods that ensure top-notch quality and durability.
Selecting the Right Timber
The foundation of any plywood manufacturing process begins with selecting the appropriate wood species. High-quality plywood requires durable and defect-free timber. Manufacturers commonly use hardwoods like birch, eucalyptus, and teak for premium plywood and softwoods like pine and spruce for general use.
The selection process involves analyzing the wood’s strength, moisture content, and resistance to decay. Plywood manufacturers in Chennai, for instance, prioritize sourcing timber from reliable suppliers to ensure consistency in quality. This meticulous selection process helps produce plywood that meets diverse consumer needs.
Peeling and Slicing the Logs
Once the timber is selected, it undergoes a peeling or slicing process to create thin veneers. The logs are debarked and conditioned in hot water or steam to make them pliable for slicing. They are then fed into a lathe machine, which peels them into continuous sheets of veneer.
This process is crucial because the veneers form the structural layers of the plywood. Uniform thickness and smoothness are essential to ensure that the layers bond effectively. Leading plywood suppliers in Chennai use advanced machinery to produce veneers with minimal waste, maximizing efficiency.
Drying and Grading the Veneers
After peeling, the veneers contain high moisture levels that need to be reduced. The sheets are passed through drying machines or kilns to achieve the desired moisture content, which is critical for strong adhesion during the bonding process.
Once dried, the veneers are graded based on quality. Defects like knots, cracks, or discoloration are identified, and the sheets are sorted accordingly. Plywood manufacturers in Chennai emphasize stringent grading to ensure only the best veneers are used for premium-grade plywood, ensuring durability and aesthetic appeal.
Applying Adhesives
The bonding process involves applying adhesive to the veneers. High-quality plywood requires durable adhesives that ensure strong bonds between the layers. Commonly used adhesives include phenol-formaldehyde and urea-formaldehyde resins, known for their water resistance and strength.
The adhesive is evenly spread over the veneer surfaces to create uniform bonding. Ensuring precision at this stage is critical to avoid delamination. Top plywood suppliers in Chennai use advanced adhesive application techniques to produce plywood that meets international standards for strength and durability.
Assembling the Veneers
The next step is layering the veneers to form a plywood sheet. The veneers are stacked alternately, with their grains oriented at right angles to each other. This cross-graining technique enhances the plywood’s strength, stability, and resistance to warping.
Manufacturers carefully align the veneers during assembly to ensure uniform thickness and structural integrity. This meticulous attention to detail is what sets high-quality plywood apart, ensuring it meets the diverse requirements of construction and interior design projects.
Hot Pressing for Strong Bonds
After assembly, the stacked veneers are subjected to a hot press. The hot pressing process applies heat and pressure to cure the adhesive and bond the veneers together. The temperature, pressure, and pressing time are carefully controlled to ensure optimal bonding.
This step significantly impacts the plywood’s strength and durability. High-end plywood manufacturers in Chennai invest in advanced hot-pressing technology to produce sheets with consistent quality, suitable for both residential and commercial applications.
Trimming and Sanding
Once the plywood sheets are pressed and bonded, they are trimmed to the desired dimensions. The edges are cut to create uniform panels that meet standard sizing requirements. After trimming, the sheets are sanded to achieve a smooth and even surface.
Sanding is a vital step in enhancing the plywood’s finish. It removes surface irregularities, ensuring the panels are ready for further processing, such as lamination or painting. Plywood suppliers in Chennai often cater to industries that demand precision, making this step indispensable in the production of high-quality products.
Quality Inspection and Grading
Before the plywood is packaged and shipped, it undergoes rigorous quality checks. Manufacturers inspect the sheets for defects like warping, delamination, or uneven surfaces. Testing for parameters such as load-bearing capacity and water resistance is also conducted.
Based on these inspections, the plywood is graded into different categories. Premium-grade plywood is free from visible defects and meets stringent quality standards, while lower grades may have minor imperfections. These quality measures help plywood manufacturers in Chennai maintain their reputation for supplying reliable products.
Packaging and Distribution
The final step in the manufacturing process is packaging the plywood sheets for transportation. Sheets are bundled together and wrapped to protect them from moisture and damage during transit. Proper labeling ensures that customers can identify the grade and specifications of each plywood sheet.
Efficient distribution networks are vital for ensuring that plywood reaches customers promptly and in perfect condition. Many Plywood manufacturers in Chennai leverage advanced logistics solutions to meet the growing demand from industries like construction, furniture, and interiors.
Conclusion
The journey of creating high-quality plywood involves a series of meticulous steps, from timber selection to final packaging. Each stage requires precision, innovation, and a commitment to quality. By understanding the manufacturing process, customers can appreciate the value that experienced plywood manufacturers bring to the table.
If you’re seeking durable and reliable plywood, look no further than trusted plywood manufacturers in Chennai. Their expertise and dedication to quality make them a top choice for all your construction and interior needs.
What's Your Reaction?
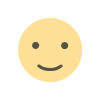
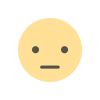
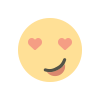
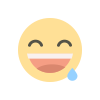
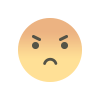
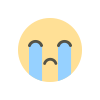
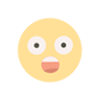