Boost Equipment Performance with Our Preventive & AMC Services
PR Power Engineers prepare and follow Industrial site-specific Preventive Maintenance, Shutdown Maintenance & Annual Maintenance for all Power plants, Substations and Process Industries routines to guarantee that your system is properly maintained and tested.
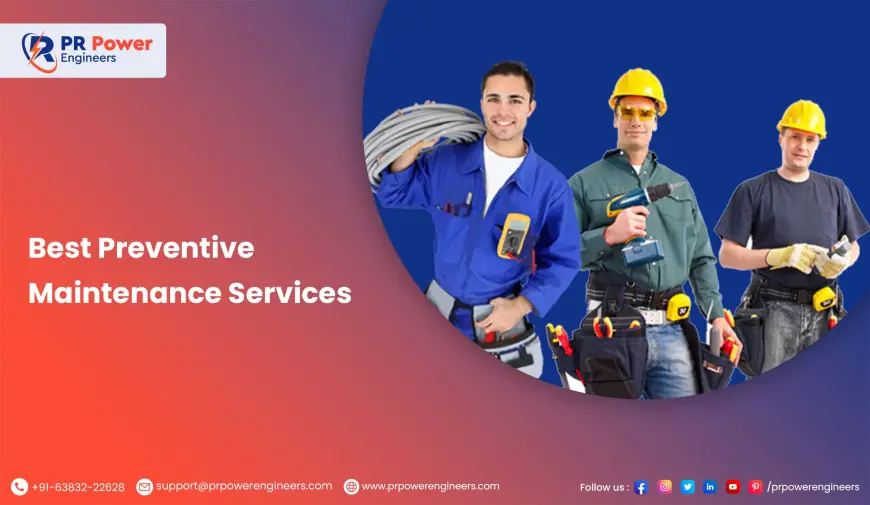
Preventive maintenance systems are crucial to ensuring the longevity and efficient operation of machinery and equipment across various industries. By adopting a proactive approach, these systems aim to prevent equipment failures before they occur, thereby reducing downtime, minimizing repair costs, and extending the lifespan of assets. This process is essential for industries that rely heavily on machinery, such as manufacturing, power generation, and transportation.
Key Components of Preventive Maintenance
-
Scheduled Inspections: Regular inspections are at the core of preventive maintenance. These are carried out according to a predetermined schedule based on the manufacturer’s recommendations, historical data, and the operational environment of the equipment. Inspections involve checking critical components for wear and tear, lubrication levels, alignment, and other potential issues that could lead to a breakdown.
-
Condition Monitoring: Condition monitoring involves continuously assessing the health of equipment using various technologies. Vibration analysis, thermography, oil analysis, and ultrasonic testing are some common techniques used to detect anomalies in the equipment's operation. By identifying deviations from normal operating conditions, maintenance teams can take corrective action before a failure occurs.
-
Routine Maintenance Tasks: These tasks include activities such as cleaning, lubricating, tightening, and adjusting components to ensure optimal performance. Routine maintenance is typically performed during scheduled downtime to avoid interrupting production processes. Ensuring that these tasks are carried out consistently helps in preventing minor issues from escalating into major problems.
-
Data Management and Analysis: Modern preventive maintenance systems rely heavily on data collection and analysis. Maintenance management software is used to track the performance of equipment, record maintenance activities, and analyze trends. This data-driven approach allows for more accurate forecasting of maintenance needs, better inventory management, and improved decision-making.
Benefits of Preventive Maintenance Systems
-
Reduced Downtime: One of the most significant benefits of preventive maintenance is the reduction in unplanned downtime. By addressing potential issues before they lead to equipment failure, businesses can maintain continuous operation, which is particularly important in industries where downtime can result in significant financial losses.
-
Cost Savings: Preventive maintenance helps in avoiding the high costs associated with emergency repairs and equipment replacement. Although there is an upfront cost associated with implementing a preventive maintenance system, the long-term savings far outweigh these initial expenses. Moreover, the extended lifespan of equipment reduces the need for frequent capital investments in new machinery.
-
Improved Safety: Regular maintenance of equipment not only ensures optimal performance but also enhances safety in the workplace. Faulty machinery can pose significant risks to employees, leading to accidents and injuries. Preventive maintenance ensures that equipment operates within safe parameters, thereby reducing the likelihood of safety incidents.
-
Increased Equipment Lifespan: Consistent maintenance ensures that equipment remains in good working condition for a longer period. This not only delays the need for replacements but also maintains the asset's value over time. In industries where equipment is a significant capital investment, prolonging its useful life is a key financial benefit.
-
Enhanced Operational Efficiency: Well-maintained equipment operates more efficiently, consuming less energy and producing higher quality outputs. This leads to lower operational costs and improved productivity, making preventive maintenance a key component of overall business strategy.
Implementing a Preventive Maintenance System
Implementing an effective preventive maintenance system requires careful planning and execution. It involves selecting the right maintenance management software, training personnel, and establishing clear protocols for inspections and repairs. Additionally, companies should ensure that there is regular communication between maintenance teams and other departments to align maintenance activities with production schedules.
In conclusion, preventive maintenance systems are an investment in the long-term success of any organization that relies on machinery. By proactively addressing potential issues, businesses can ensure smoother operations, reduce costs, and enhance overall productivity.
Contact us today to schedule our expert Preventive and AMC services and keep your operations running smoothly. - https://www.prpowerengineers.com/preventive-maintenance-systems/