How to Make Polyurethane Wheels: A Comprehensive Overview
Learn how polyurethane wheels are made, from material selection to molding and curing, ensuring durability, strength, and efficiency for various industrial applications.
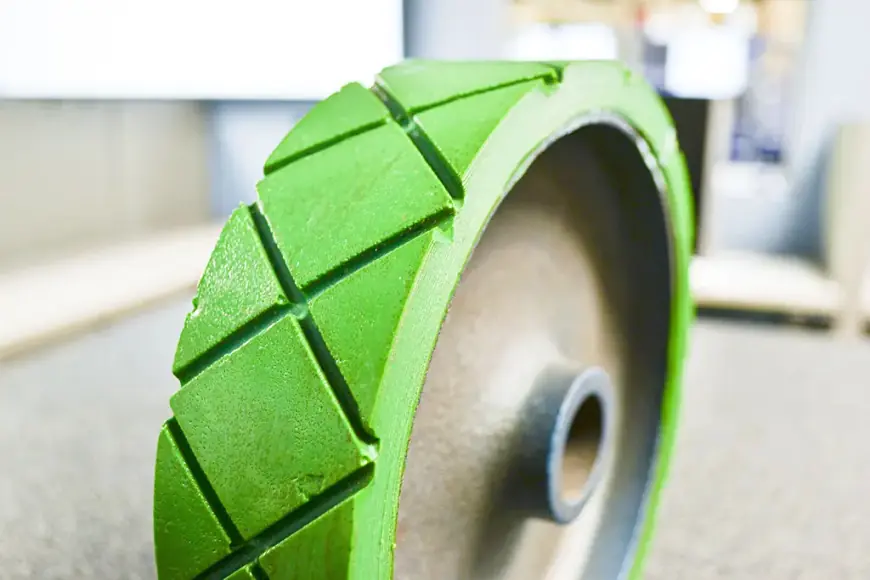
As a writer and researcher specializing in industrial materials and manufacturing processes, I have explored numerous advancements that contribute to efficiency and durability in various industries. One such innovation is polyurethane wheels manufacturers, widely used in industrial, automotive, medical, and commercial applications due to their superior durability, load-bearing capacity, and resistance to wear and tear. Understanding how these wheels are made provides insight into their quality and performance. This article offers a comprehensive overview of the manufacturing process, covering materials, methods, and key considerations in production.
Understanding Polyurethane Wheels
Polyurethane wheels are crafted from a synthetic polymer that combines the elasticity of rubber with the toughness of plastic. This unique combination results in wheels that are durable, resilient, and capable of handling heavy loads. They are commonly found in material handling equipment, hospital carts, roller coasters, and robotics due to their ability to reduce noise, resist chemicals, and provide smooth operation.
Materials Required for Manufacturing
The production of polyurethane wheels involves various raw materials and components, each contributing to the wheel’s overall performance. The primary materials used include:
-
Polyurethane Resins: These serve as the primary ingredient, offering flexibility, strength, and chemical resistance.
-
Catalysts and Additives: Used to control curing time, hardness, and other properties.
-
Metal or Plastic Cores: Provide structural support, especially in heavy-duty applications.
-
Mold Release Agents: Ensure the polyurethane does not stick to the molds during the curing process.
-
Color Pigments: Added to achieve specific aesthetic or branding requirements.
The Manufacturing Process
1. Designing the Mold
Before manufacturing begins, a mold must be designed to create the desired wheel shape. The mold is typically made of metal and precisely engineered to ensure consistency and accuracy in production. Factors such as wheel diameter, tread pattern, and core material must be considered in the mold design.
2. Preparing the Core
Many polyurethane wheels include a core, often made of metal or high-strength plastic, to enhance structural integrity. The core must be pre-treated to ensure proper adhesion with the polyurethane material. This involves:
-
Cleaning: Removing dirt, grease, and contaminants.
-
Surface Roughening: Sandblasting or chemical etching to improve adhesion.
-
Priming: Applying a bonding agent to facilitate a strong connection between the core and polyurethane.
3. Mixing and Preparing the Polyurethane Compound
Polyurethane is formed by mixing liquid components, including resins, catalysts, and additives, in precise proportions. The mixture must be carefully controlled to achieve the desired properties, such as hardness, flexibility, and wear resistance.
-
The components are combined in a mixing chamber under controlled temperatures.
-
Pigments or reinforcements are added as needed.
-
The mixture is degassed to remove air bubbles that could weaken the final product.
4. Pouring or Injecting the Polyurethane
Once the polyurethane mixture is prepared, it is poured or injected into the pre-designed molds. Depending on the wheel type, manufacturers use different methods:
-
Gravity Casting: The liquid polyurethane is poured into molds and allowed to settle naturally.
-
Centrifugal Casting: The mold spins at high speed to distribute the material evenly.
-
Injection Molding: The polyurethane is injected under pressure for high-precision wheels.
5. Curing and Hardening
After the material is introduced into the mold, it undergoes a curing process where heat and pressure are applied to solidify the polyurethane. This process can take anywhere from a few hours to several days, depending on the formulation and required hardness.
-
The molds are placed in an oven or a temperature-controlled environment.
-
Curing time and temperature settings vary based on the wheel's intended application.
6. Demolding and Trimming
Once the curing process is complete, the wheels are removed from the molds. Excess polyurethane material, also known as flash, is trimmed to ensure a smooth and uniform finish. This step ensures that the wheels meet precise specifications and quality standards.
7. Post-Processing and Quality Control
To ensure the highest quality, polyurethane wheels undergo several post-processing steps and inspections:
-
Machining: Fine adjustments to dimensions and surface texture.
-
Coating: Additional layers for UV protection or enhanced durability.
-
Quality Testing: Checking hardness, load capacity, and resistance to chemicals and abrasion.
Key Considerations in Manufacturing
Several factors influence the final quality and performance of polyurethane wheels:
-
Shore Hardness: Determines the softness or firmness of the wheel, affecting grip and shock absorption.
-
Load Capacity: Different applications require varying weight capacities, influencing the core material and polyurethane formulation.
-
Environmental Resistance: Wheels used in harsh environments require additives for UV, chemical, and moisture resistance.
-
Customization: Some industries require unique designs, colors, or embedded branding.
Applications of Polyurethane Wheels
Due to their versatility, these wheels are used in numerous industries, including:
-
Material Handling: Found in forklifts, carts, and conveyor systems for efficient movement.
-
Medical Equipment: Used in hospital beds, stretchers, and wheelchairs for smooth mobility.
-
Manufacturing and Automation: Essential in robotic systems and production lines.
-
Retail and Commercial Use: Shopping carts, display racks, and other mobile units benefit from their durability.
-
Automotive and Aerospace: Applied in specialized machinery and transport systems.
Conclusion
The process of making polyurethane wheels involves precision, expertise, and attention to material selection, mold design, and curing techniques. Their widespread applications across industries stem from their durability, resilience, and ability to withstand demanding conditions. As a writer and researcher, I find the evolution of industrial materials fascinating, and polyurethane continues to prove itself as a high-performance solution for mobility and transportation. Understanding the manufacturing process allows businesses to make informed choices and select the best wheels for their specific needs.