Turned Parts: A Comprehensive Guide to Precision Manufacturing
Turned parts are components that have been shaped and machined through the process of turning, which involves rotating a workpiece on a lathe while a cutting tool shapes it. This process is crucial in many industries, including aerospace,Turned Parts , and manufacturing, for producing parts with high precision, complex geometries, and smooth finishes. The versatility and accuracy of turned parts make them essential in a variety of applications.
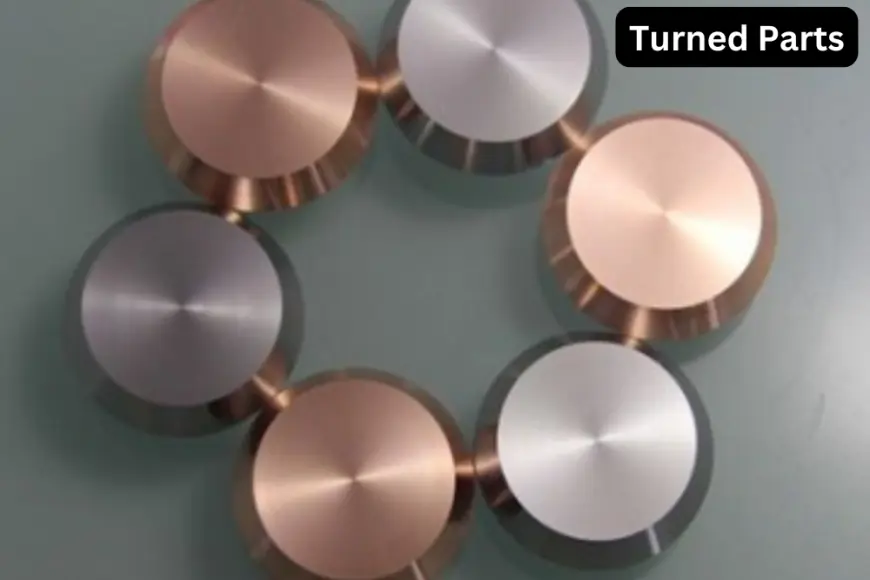
Turned parts are components that have been shaped and machined through the process of turning, which involves rotating a workpiece on a lathe while a cutting tool shapes it. This process is crucial in many industries, including aerospace,Turned Parts , and manufacturing, for producing parts with high precision, complex geometries, and smooth finishes. The versatility and accuracy of turned parts make them essential in a variety of applications.
This guide will cover everything you need to know about turned parts, including the turning process, types of turned parts, materials used, advantages, applications, and how to choose the right turned parts for your needs.
What Are Turned Parts?
Turned parts are components that have been produced through a machining process known as turning, which is typically carried out using a lathe machine. The lathe rotates the workpiece while a cutting tool is applied to shape it, removing material to achieve the desired form. Turned parts are characterized by their cylindrical or rotational symmetry, but they can be produced in a variety of shapes and sizes, from simple rods and shafts to complex, highly detailed components.
Key Characteristics of Turned Parts:
- Rotational Symmetry: Most turned parts are cylindrical, but they can also have conical, spherical, or other forms of rotation-based geometries.
- High Precision: Turning offers a high degree of precision and accuracy, allowing for the creation of components with tight tolerances.
- Smooth Surface Finish: The turning process often results in a smooth, high-quality surface finish, which is ideal for parts that require minimal post-processing.
The Turning Process Explained
The turning process involves the use of a lathe, a machine tool that rotates the workpiece while a stationary cutting tool removes material from it. Here's how the process works:
- Setup: The workpiece is securely clamped onto the lathe’s spindle, and the cutting tool is set at the desired position.
- Rotation: As the lathe turns the workpiece, the cutting tool is applied to remove material in a precise, controlled manner. The tool may move along multiple axes to create different shapes and profiles.
- Cutting: The cutting tool progressively removes material in the form of chips, shaping the workpiece to the desired dimensions.
- Finishing: After the primary cutting operation, additional steps like polishing, deburring, or coating may be done to improve the part's finish and functionality.
The process can be adjusted to create different geometries, surface finishes, and tolerances depending on the complexity of the part and the capabilities of the lathe machine.
Types of Turned Parts
Turned parts can vary in terms of their design, function, and application. Some of the most common types include:
1. Shafts
Shafts are cylindrical parts that transmit power or motion within machinery and mechanical systems. They are often turned to specific tolerances to ensure they fit precisely into bearings, gears, or other components.
- Applications: Automotive drive shafts, motor shafts, conveyor shafts.
2. Bushings
Bushings are cylindrical sleeves used to reduce friction and wear between two parts. They are often turned to tight tolerances to fit snugly into housings or bores.
- Applications: Bearings, suspension systems, automotive components.
3. Spindles
Spindles are rotating components used in machinery, typically for driving or supporting cutting tools or workpieces. They require high precision and stability, making turning an ideal method for their production.
- Applications: CNC machines, turbines, pumps.
4. Valves and Fittings
Valves and fittings, such as ball valves, check valves, and pipe fittings, often require turning to create their precise, functional components.
- Applications: Plumbing, industrial machinery, HVAC systems.
5. Precision Screws and Bolts
Turned screws and bolts are common in precision applications, where the thread profile, diameter, and surface finish are critical for performance.
- Applications: Aerospace, medical devices, electronics.
6. Connectors
Turned connectors, which often include pins, plugs, and sockets, are integral to electrical systems. These parts often need to have extremely precise dimensions for proper function and connectivity.
- Applications: Electronics, automotive, industrial machinery.
Materials Used for Turned Parts
The materials used for making turned parts are typically selected based on their mechanical properties, corrosion resistance, and the intended application. Some common materials include:
1. Stainless Steel
Stainless steel is a popular material for turned parts due to its excellent strength, durability, and resistance to corrosion. It’s widely used in medical, automotive, and food industries.
- Benefits: Corrosion-resistant, strong, durable.
- Applications: Medical implants, automotive components, industrial equipment.
2. Aluminum
Aluminum is a lightweight material that is easy to machine and offers good corrosion resistance. It is often used for parts that need to be light but strong.
- Benefits: Lightweight, easy to machine, corrosion-resistant.
- Applications: Aerospace, automotive, electronics.
3. Brass
Brass is often used for precision components that require a smooth surface finish and good electrical conductivity. It is easy to machine and provides excellent corrosion resistance.
- Benefits: Excellent machinability, corrosion resistance, good conductivity.
- Applications: Plumbing, electrical connectors, decorative items.
4. Carbon Steel
Carbon steel is known for its strength and is commonly used in applications where toughness is required. It is a versatile material used for making a variety of turned parts.
- Benefits: Strong, versatile, cost-effective.
- Applications: Automotive parts, industrial machinery, gears.
5. Titanium
Titanium is known for its lightweight, strength, and resistance to extreme temperatures and corrosion. While it is more difficult to machine, it is used in industries where these properties are essential.
- Benefits: Strong, lightweight, corrosion-resistant.
- Applications: Aerospace, medical implants, military.
Advantages of Turned Parts
Turned parts offer several benefits, making them an attractive option for many industries:
1. Precision and Accuracy
Turned parts can be made to extremely tight tolerances, ensuring that each part fits precisely within its designated application.
2. High Surface Quality
The turning process often results in a smooth surface finish, which is ideal for parts that need to perform well without additional coatings or treatments.
3. Versatility
Turned parts can be produced in a wide variety of shapes, sizes, and materials, making them suitable for use in many different industries and applications.
4. Cost-Effective
Turning is often a more cost-effective option for producing small to medium batches of parts, as it requires less material waste and can be completed more quickly than other manufacturing methods.
5. Shorter Lead Times
The turning process typically has shorter lead times compared to other machining processes, making it ideal for rapid prototyping or orders requiring quick turnaround times.
Applications of Turned Parts
Turned parts are used in a wide range of industries and applications due to their versatility and precision. Some key industries where turned parts are crucial include:
1. Automotive Industry
In the automotive industry, turned parts like shafts, pistons, and connectors are essential for vehicle performance, reliability, and safety.
2. Aerospace
Aerospace applications require high-performance components, such as fasteners, valves, and connectors, that are often made using turning.
3. Medical Devices
Turned parts are used in medical devices, from surgical tools to implants, where precision and reliability are critical for patient safety.
4. Electronics
The electronics industry relies on turned components such as connectors, switches, and housings to ensure electrical systems function properly.
5. Industrial Equipment
In industrial manufacturing, turned parts like bearings, gears, and valves are fundamental to machinery and production lines.
How to Choose the Right Turned Parts
Selecting the right turned parts for your application involves several factors. Here are some important considerations:
- Material Requirements: Ensure that the material used for the turned parts meets the mechanical and environmental conditions of your application.
- Tolerances and Specifications: Check if the part requires precise tolerances and if the chosen manufacturing process can meet these requirements.
- Volume and Lead Time: Consider whether the part needs to be produced in large quantities or as a one-off prototype and factor in lead time.
- Budget: Compare the cost of turning with other manufacturing processes and determine if turning provides the best value for your project.
Conclusion
Turned parts play a vital role in many industries due to their precision, versatility, and efficiency in manufacturing. Whether you are looking for shafts, bushings, valves, or connectors, the turning process provides a reliable solution for creating high-quality components. By understanding the types of turned parts, materials, and manufacturing processes, you can make informed decisions to meet the needs of your specific application. With continued advancements in technology, the capabilities of turning will only expand, further solidifying its place as a cornerstone of modern manufacturing