Optimizing Industrial Efficiency Exploring Outflow Heaters and Thermal Insulation Techniques
Explore how outflow heaters and thermal insulation techniques enhance industrial efficiency by optimizing temperature control and reducing energy consumption effectively.
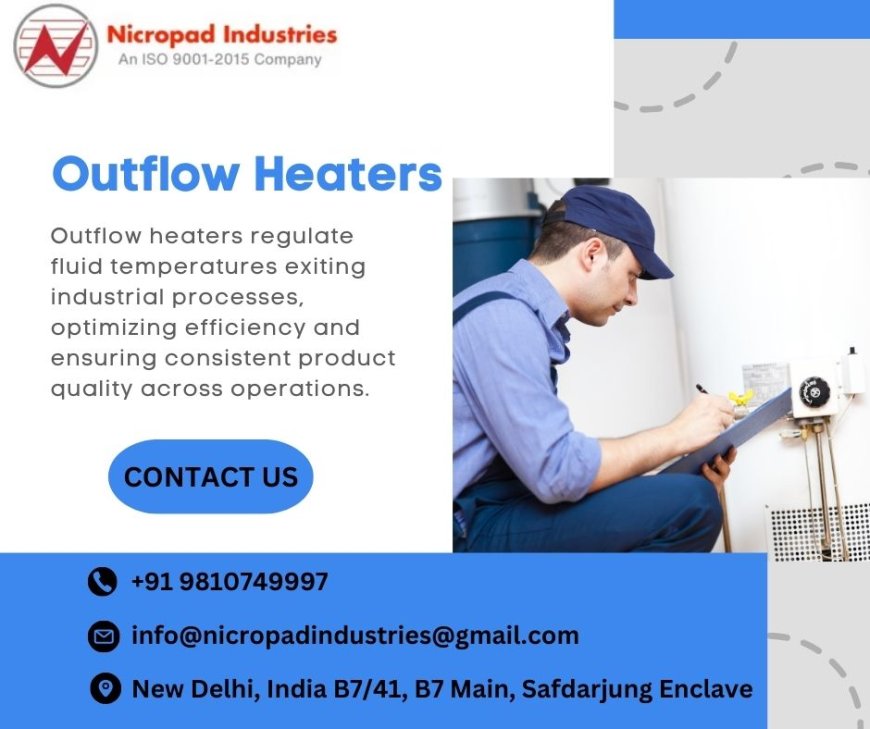
The goal of optimizing industrial efficiency is to increase productivity while decrease waste and consumption of resources. In order to maintain operational effectiveness and save energy expenses in industrial settings, this article examines techniques including outflow heaters and thermal insulation. Process reliability and environmental sustainability can be significantly increased by industries by optimizing heat management and insulation measures.
Understanding Outflow Heaters
Specialized equipment called outflow heaters is used to warm materials as they leave industrial systems or operations. Liquids are maintained at the ideal temperature by them in order to maintain product quality and process efficiency. Electric or steam-powered outflow heaters are available, and they are made to meet accurate flow rates and temperature specifications in a range of industrial settings.
Applications of Outflow Heaters in Industrial Settings
A wide range of sectors, including food manufacture, oil and gas production, and chemical processing, use outflow heaters. Liquids leaving tanks, reactors that are suitable or pipelines are heated by them in order to avoid thickness changes, crystallization, or solidification that can complicate operations. Outflow heaters improve the whole effectiveness by contributing to continuous production and decreased downtime through the maintenance of constant temperatures.
Benefits of Outflow Heaters in Process Optimization
Outflow heaters' main advantage is their capacity for optimizing Industrial Thermal Insulation processes through precision fluid temperature management. This optimization minimizes the need for unnecessary heating or reheating of fluids during processing, improving product quality, shortens production times, and uses less energy. Outflow heaters contribute to long-term cost savings and operational efficiency by increasing equipment lifespan and dependability through the maintenance of stable flow conditions.
Types and Materials of Thermal Insulation
Depending on their intended use and performance standards, thermal insulation materials differ greatly from one another. Foam, fiberglass, mineral wool, and reflective materials like aluminum foil are examples of common varieties. These materials are selected for industrial applications due to their longevity, compatibility with particular climatic conditions, and resistance to heat.
Industrial Applications of Thermal Insulation
In Industrial Thermal Insulation settings, thermal insulation is frequently used to improve energy efficiency, maintain temperature stability, and minimize heat gain or loss. Applications include protecting delicate products or processes from temperature changes outside and insulating pipes, tanks, and equipment. Thermal insulation is crucial to the industrial, HVAC, and petrochemical industries in order to meet regulatory standards and maximize operating effectiveness.
Efficiency Comparison: Outflow Heaters vs. Thermal Insulation
Thermal insulation and outflow heaters are two distinct technologies that improve Industrial Thermal Insulation efficiency. In order to guarantee consistent product quality and operational continuity, outflow heaters concentrate on maintaining fluid temperatures at particular points in the process. In contrast, thermal insulation minimizes energy loss or gain by addressing heat transfer across surfaces, increasing system efficiency overall and lowering the need for heating or cooling. Specific operating needs, such as precise temperature control, environmental factors, and energy conservation objectives, will determine which of these technologies is best.
Energy Savings and Cost Effectiveness
In industrial applications, thermal insulation and outflow heaters both provide significant cost and energy savings. Compared to continuous heating techniques, outflow heaters minimize total usage by heating liquids only when necessary. By reducing heat gain or loss, thermal insulation reduces the amount of energy needed to keep systems and processes at the proper temperature. When combined, these technologies significantly save operating costs and increase durability by lowering carbon footprints and preserving resources.
Installation Considerations for Industrial Settings
In Industrial Thermal Insulation settings, the durability and efficacy of outflow heaters are significantly improved by suitably installed thermal insulation and heaters. To achieve maximum performance, a number of factors are crucial, including material choice, compatibility with current equipment, and following manufacturer instructions. Guaranteeing smooth operation and energy efficiency during installation also involves sealing techniques, insulation thickness, and integration with control systems.
Safety Measures and Compliance
When installing and using outflow heaters and thermal insulation in industrial environments, safety precautions and regulatory compliance are essential. To avoid electrical dangers and guarantee worker safety, electrical components must be sufficiently insulated and grounded. In order to reduce the risks connected with heat management technologies, safer work environments and the avoidance of potential damage or malfunction to equipment are created when industry standards and regulations pertaining to material specifications, installation techniques, and operational guidelines are followed.
Conclusion
Process optimization using tools like thermal insulation and outflow heaters is a major component of effective Industrial Thermal Insulation operations. These solutions save energy use, lower operating costs, and increase productivity. With the help of outflow heaters, fluid temperature may be precisely maintained, improving both process effectiveness and product quality. Thermal insulation reduces heat gain or loss, increasing energy economy and maintaining steady state of operation. When combined, these technologies improve industrial productivity while helping to achieve sustainable development goals by minimizing their negative effects on the environment and maintaining resources. Industries may optimize the advantages of these technologies and create safer, more productive workplaces while attaining long-term economic and environmental benefits by following safe installation procedures, safety protocols, and regulatory compliance.
What's Your Reaction?
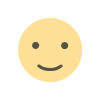
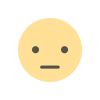
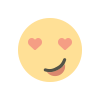
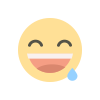
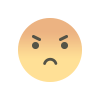
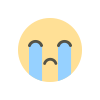
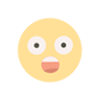