Inconel 825 FillerWire: Composition, Properties, and Applications
Discover the exceptional properties of Inconel 825 filler wire, offering corrosion resistance, strength, and reliability for welding in demanding industries.
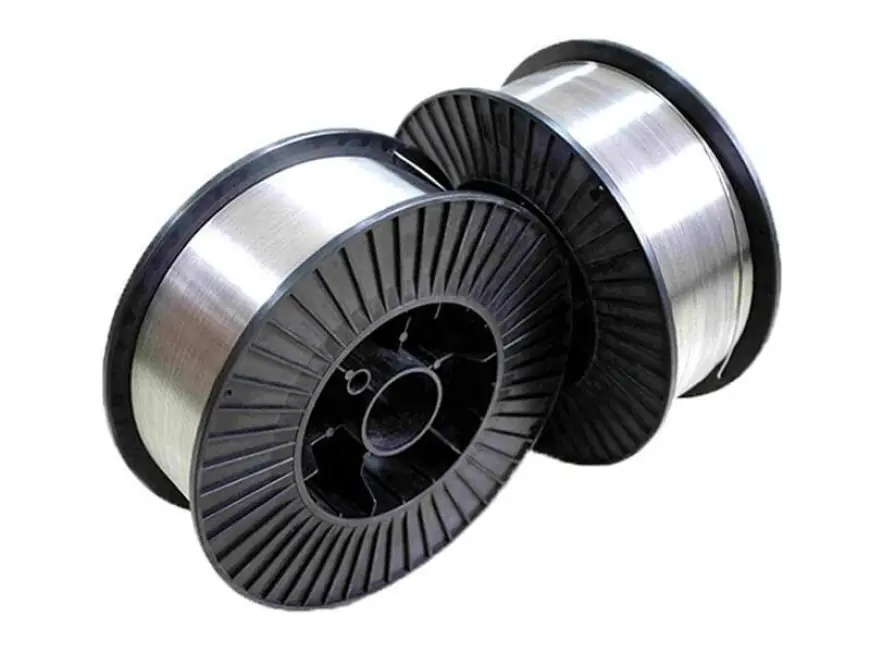
Inconel 825 filler wire is an alloy that is made of nickel, iron, and chromium and is renowned for its high resistance to corrosion and oxidation. The variety is utilized in welding at all industrial levels and is well known for its excellent endurance to harsh environmental conditions, including acid and seawater applications. In this blog, we will discuss the composition, properties, and key applications of Inconel 825 filler wire and why it is important for producing strong, long-lasting welds.
Composition of Inconel 825 Filler Wire
The excellent performance of the Inconel 825 filler wire is attributed to its accurate alloy composition. It mainly has:
Nickel (38-46%): Offers corrosion resistance and strength.
Iron (22-38%): Contributes to the structural integrity of the alloy.
Chromium (19.5-23.5%): Improves oxidation and pitting resistance.
Molybdenum (2.5-3.5%): Enhances resistance to localized corrosion, such as pitting and crevice corrosion.
Copper (1.5-3%): Provides additional protection against sulfuric and phosphoric acids.
Titanium (0.6-1.2%): Improves mechanical properties and avoids intergranular corrosion.
Such a balanced composition makes
sure that the Inconel 825 filler wire acts efficiently in extreme temperatures, pressure, and corrosive environments.
Properties of Inconel 825 Filler Wire
Inconel 825 filler wire enjoys wider usage as it has unique properties that make it fantastic for tough welding operations. Some are as follows:
Corrosion Resistance
This wire resists various corrosion agents, such as sulfuric, phosphoric, and nitric acids, as well as seawater and oxidizing agents. For this reason, it can be used in marine, chemical, and oil and gas applications.
High-Temperature Stability
It keeps strength and stability even in high temperatures, so it can be used in furnaces and heat exchangers.
Oxidation Resisting Capabilities
Inconel 825 does not experience oxidation, even for long periods under conditions that expose it to high temperatures and corrosive environments.
Welding Capabilities
It is welding that, through standard techniques, results in tight and strong welds with few defects.
Mechanical Strength
The filler wire can provide excellent tensile and yield strength, which ensures that high-stress applications are reliable.
Application of Inconel 825 Filler Wire
Inconel 825 filler wire is one of the robust filling wires adopted for welding applications in many organizations. Its main applications include:
Chemical Processing
Welding of components exposed to highly corrosive chemicals, such as tanks and reactors and piping systems in chemical plants, are often performed with Inconel 825 filler wire.
Marine Industry
The alloy is also useful for welding marine equipment like seawater heat exchangers, pipelines, and offshore platforms because it protects against seawater corrosion.
Oil and Gas Industry
The filler wire is used in welding pipelines, separators, and other pieces that are exposed to strong conditions in processes used within oil and gas extraction and refinement operations.
Pollution Control
The Inconel 825 filler wire is utilized in scrubbers, units of flue gas desulfurization, and other equipment designed for the management and mitigation of environmental pollution.
Aerospace Applications
The high-temperature and corrosion-resistant qualities of the wire make it ideal for welding components within jet engines, exhaust ducts, and fuel systems.
Nuclear Industry
Components in nuclear reactors and associated systems that require strength at high temperatures and also resist corrosion caused by radiation are welded using Inconel 825.
The benefits of using Inconel 825 filler wire for welding are as follows:
It ensures the long-lasting performance of welded structures due to superior corrosion resistance and mechanical strength. Its acceptance makes it suitable for widespread application in various industries, especially under high-stress and corrosive conditions.
Easy Weldability: Easy welding with no defects.
Cost-Effective: It eliminates maintenance and repair costs through durable and reliable joints.
Limitation of Inconel 825 Filler Wire
Although Inconel 825 filler wire possesses numerous advantages, it is also accompanied by certain limitations:
It is Costlier: Since the product has some specialized properties with unique composition, it is rather costly than standard filler wires.
Specialized Handling: It requires specific techniques with skilled welders to attain optimal results.
Why Choose Reliable Inconel 825 Filler Wire Supplier?
To obtain the best welding performance, it is important to procure high-quality Inconel 825 filler wire from companies with a reliable reputation. A reliable supplier ensures:
Consistent Composition: Right alloy formulation leads to predictable performance.
Tough Quality Standards: Adherence to industry certifications and stringent testing procedures.
Expert Services: Recommendations on the right wire for your job.
Inconel 825 filler wire is a preferred choice for demanding welding applications in industries ranging from chemical processing to aerospace. Its outstanding properties, including corrosion resistance, high-temperature strength, and weldability, make it indispensable for creating strong and reliable welded joints. Businesses can ensure the success and longevity of their projects by partnering with a trusted supplier of Inconel 825 filler wire.
If you’re looking to invest in premium-quality Inconel 825 filler wire, connect with a reputable supplier to enhance your welding efficiency and application reliability.