How Custom Heat Seal Paper is Made: From Raw Material to Finished Product
Discover the fascinating process of creating custom heat seal paper, from raw materials to the final product, and its various applications.
Heat seal paper is widely used in today’s packaging with easy-to-open and easy-to-close functionality in several industries. In the food packaging solutions industry or when labelling cosmetics, an effective seal is vital to guarantee clients get fresh and safe products. This blog will guide you through the process of creating custom heat seal paper for your business, focusing on the materials, methods and advantages that businesses enjoy using heat seal paper. This knowledge of how this paper is made is useful in actually helping us make sense of the importance of this paper in our daily lives and the versatility of its use in packaging.
Getting to Know about Heat Seal Paper
Heat seal paper is a product type mainly for creating a seal that holds together when heat is applied. It comprises a base layer which is engraved or coated with a thermoplastic resin that makes the substrate melt when exposed to heat and pressure and can bond either with itself or with the other surfaces. This feature makes heat-sealable paper useful for making bags, pouches and all other forms of packaging that require a closure seal. Selecting appropriate substrate and coating materials plays a central role in deciding on the quality and durability of the finished product.
Choosing The Appropriate Basic Materials
The action process starts with choosing the right material to be used in the making of these products. In general, the characteristics and first categories are paper, resin, and additives. The kind of paper required during production can also be determined by the kind of paper required by the final product. For example, kraft paper is very durable as well as environmentally friendly while coated papers have good barrier features. The resin is one of the most important factors in defining the co-melt sealing point and heat seal strength of the papers.
The Coating Process
After the choice of the raw materials which will be used, the next process is the coating of the paper with the thermoplastic resin. This is achieved by the use of different methods of coating which include extrusion coating or gravure printing. In the extrusion coating step, the heat-sensitive resin is supplied at a molten state and is spread uniformly over the paper so that the future heat seal can take place. As compared with inclined printing, gravure printing is easier to handle when printing those shapes or patterns of resin that are incorporated with special patterns or designs. It also guarantees that the custom printed heat seal paper fully addresses the needs of different uses hence its importance.
Cutting and Finishing
After the coating has been put on and after the paper has dried or cured, it is then in the process of cutting to size the desired dimensions of the paper. This could include heating paper bags, sheets or rolls. The cutting is an exact process to achieve uniformity and to meet the total quality management of the product. Nevertheless, after cutting, the paper may be subjected to one or more finishing steps as required to beautify, for instance, through embossing or to facilitate use, through printing. During this stage, the manufacturers can come up with special printed heat seal bags with the manufacturers’ logo or even additional information about the product, which may influence the customers’ decision.
Quality Control Measures
The quality of custom heat seal paper has to be protected before it is manufactured. Different tests are carried out to meet specific standards and requirements of the market and the customers. These tests include tests to determine the heat seal strength, coating defects and general mechanical properties of the paper and how they relate to the intended performance. Stringent quality control measures must be embraced by the manufacturers to ensure that their heat seal paper rolls or sheets function perfectly in their operations.
Environmental Considerations
As more manufacturers pay attention to sustainable solutions, new approaches to developing custom heat seal paper are sought. These are the reclaiming of materials, the use of bio-degradable resins, and the purchase of materials from sustainable sources. Indeed, through the use of these procedures, the wax paper wholesale will give a competitive edge to producers who target consumers who consider environmental society in their purchase. Such a trend is also beneficial both for the environment and for companies’ image which treat ecological issues with great importance.
Conclusion
The making of custom heat seal paper is indeed an interesting process that needs rigorous planning and rigidity. Starting from acquiring laminate sheets up to the final paper produced, each stage is equally important so that the paper cocaneet the requirements of different industries. Over time, there may be a need for people to adopt more modern methods of packaging and therefore gaining a perception of how custom heat seal paper is produced is a noble process to ensure that the right choices are made by such firms. In terms of applicability to food packaging, retail bags or any other specific use, the future of this paper as part of the overall packaging technology cannot be overemphasized.
What's Your Reaction?
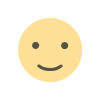
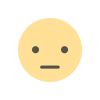
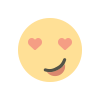
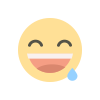
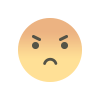
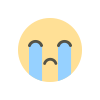
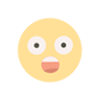