Chips Packing Machine: Revolutionizing the Snack Industry
In today's fast-paced world, the snack industry is booming, and one of the most critical components driving this growth is the chips packing machine. These machines play an essential role in ensuring that chips are packed efficiently, hygienically, and in a way that preserves their quality for consumers. With the increasing demand for snacks, investing in the right packing machinery is crucial for manufacturers aiming for both profitability and customer satisfaction. In this article, we will delve into the various aspects of chips packing machines, their types, benefits, working mechanisms, and how they contribute to the snack packaging industry.
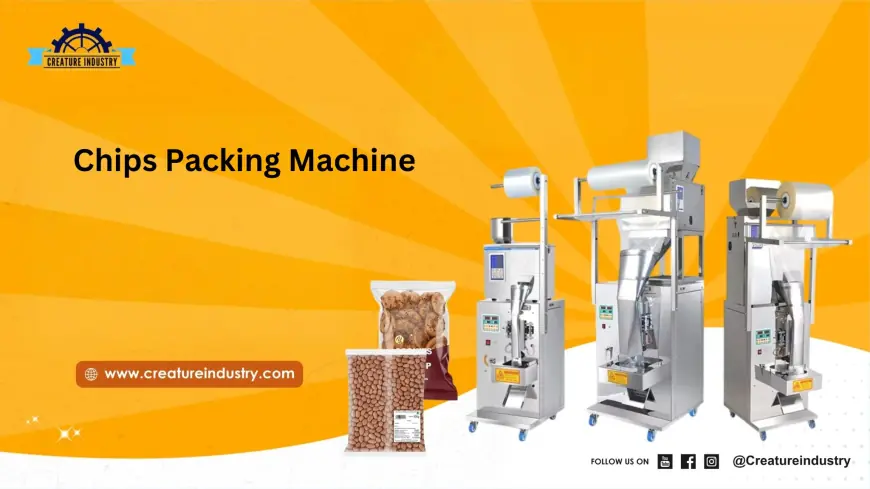
What is a Chips Packing Machine?
A chips packing machine is an automated system designed to pack chips into various types of containers, such as packets, pouches, or bags. These machines are engineered to handle chips with care, preserving their fragile nature while ensuring that the packaging is both efficient and attractive. With the rise in demand for ready-to-eat snacks, chips packing machines have become indispensable in the production process, offering manufacturers a way to increase production speed, reduce labor costs, and improve consistency in packaging.
Types of Chips Packing Machines
There are several types of chips packing machines available in the market, each tailored to meet specific needs and production capacities. Below are some of the most popular types:
1. Vertical Form Fill Seal (VFFS) Machines
The VFFS chips packing machine is one of the most common types used in the snack industry. It is highly efficient and versatile, capable of packing chips into bags or pouches of various sizes. The VFFS machines operate by forming a bag from a roll of film, filling it with chips, and then sealing it. This type of machine is ideal for manufacturers that require high-speed packing with minimal operator intervention.
2. Horizontal Form Fill Seal (HFFS) Machines
Unlike VFFS machines, the HFFS chips packing machine forms the package horizontally. This machine is typically used for premium packaging, where the appearance of the product plays a significant role. HFFS machines are perfect for packing chips into bags or trays in a way that maintains the product’s integrity and prevents breakage.
3. Horizontal Flow Wrapping Machines
These machines are often used for packing individual snack pieces such as chips bars or single-serving chips packs. The horizontal flow wrapping machine works by wrapping a continuous film around the chips and sealing it, ensuring the product stays fresh and protected from contaminants.
4. Tray Sealing Machines
For companies that package chips in trays, tray sealing machines are an excellent option. These machines seal chips in pre-formed trays, creating a tight seal that ensures the product remains fresh for an extended period. Tray sealing is especially popular in retail packaging for more premium snack products.
Advantages of Using Chips Packing Machines
The use of chips packing machines provides numerous benefits for snack manufacturers. Below are some of the key advantages:
1. Increased Efficiency
Chips packing machines significantly enhance the efficiency of the packaging process. Automated systems work much faster than manual labor, which can lead to higher production outputs in a shorter time. This is particularly beneficial for manufacturers dealing with high-demand products or those aiming to scale up operations.
2. Consistency and Precision
In the food industry, consistency and precision are critical. Chips packing machines ensure that each packet or pouch contains the exact quantity of chips, maintaining uniformity across production batches. This is especially important for brands aiming to offer a consistent consumer experience.
3. Reduced Labor Costs
With a chips packing machine in place, manufacturers can reduce their reliance on human labor for the packaging process. This not only reduces operational costs but also minimizes the risk of human error, ensuring higher product quality and fewer packaging defects.
4. Improved Hygiene and Safety
Food safety is a top priority in the snack industry, and chips packing machines help maintain high hygiene standards. These machines are designed with food-grade materials, preventing contamination during the packaging process. They are also easy to clean and maintain, further ensuring that they meet the stringent hygiene requirements set by regulatory bodies.
5. Enhanced Packaging Flexibility
Modern chips packing machines offer flexibility in terms of packaging styles and sizes. Whether you need to pack chips in small snack-sized bags or larger family-sized pouches, these machines can accommodate a wide range of packaging formats, allowing manufacturers to cater to diverse consumer preferences.
How Does a Chips Packing Machine Work?
The working mechanism of a chips packing machine is relatively straightforward but involves several precise steps to ensure that the final product is packed correctly. Below is a breakdown of the typical process:
1. Film Unwinding
The process begins with the unwinding of a roll of packaging film, which forms the outer layer of the chip packet. The film is typically made of materials such as polyethylene or laminated plastic, designed to keep the chips fresh.
2. Bag Formation
Once the film is unwound, the machine forms it into the desired shape, either as a pouch or bag, depending on the type of machine used. This is usually achieved by folding the film into a tube and then sealing the edges to create a bag.
3. Filling the Bag
After the bag is formed, the machine fills it with a predetermined amount of chips. This is done using a variety of filling systems, such as volumetric fillers, weighers, or auger fillers, depending on the type of chips being packed and the desired weight per pack.
4. Sealing the Bag
Once the chips are dispensed into the bag, the machine seals the top to prevent the contents from spilling out. The sealing process is crucial to maintaining the freshness of the chips and ensuring that they stay protected during transportation and storage.
5. Cutting and Packaging
After sealing, the machine cuts the bags to the required size and prepares them for the next stage of the production process, such as labeling, boxing, or shipping.
Factors to Consider When Choosing a Chips Packing Machine
Choosing the right chips packing machine is critical for maximizing production efficiency and product quality. Here are some factors to consider when making your decision:
1. Production Volume
Consider your production volume and choose a machine that can handle your output requirements. High-speed machines are ideal for large-scale operations, while more compact machines may be suitable for smaller production runs.
2. Packaging Type
Different machines are designed for different types of packaging. If you need a specific bag shape, size, or material, make sure the machine you choose can accommodate those needs.
3. Budget
While high-end chips packing machines offer advanced features, they may come with a higher price tag. It’s essential to balance your budget with the functionality and capacity you need.
4. Maintenance and Support
Choose a machine that offers easy maintenance and reliable after-sales support. Regular maintenance ensures that your machine operates efficiently, while a strong support network can help with troubleshooting and repairs.
Conclusion
The chips packing machine is an essential investment for manufacturers in the snack industry. By increasing efficiency, ensuring consistency, and maintaining high hygiene standards, these machines play a critical role in the production process. With various types available, each designed to meet specific needs, manufacturers can select the most suitable machine to enhance their packaging operations. Whether you are looking to improve production speed, reduce labor costs, or boost the quality of your packaging, a chips packing machine is an indispensable tool that can help propel your business forward.