Barrel Pumps: Revolutionizing the Chemical Industry
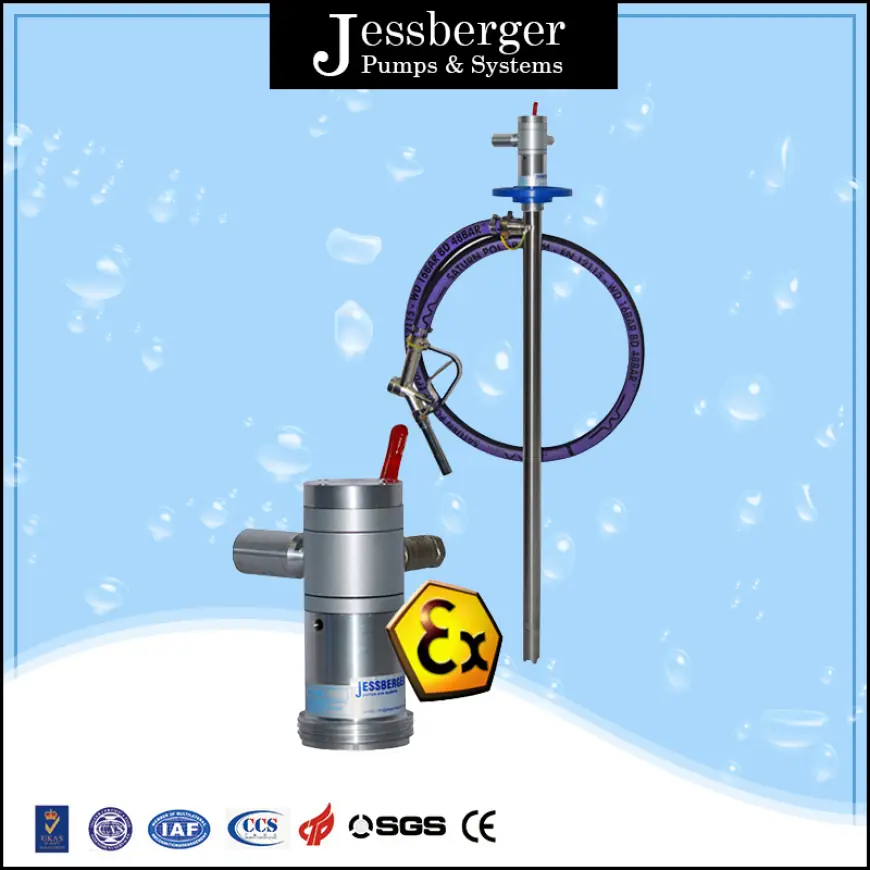
It is hazardous to handle chemicals by hand. Highly volatile chemicals can cause huge damage and injury. So, for security reasons, chemicals are transferred in industries using special equipment called the barrel pump. This pump tool can easily handle aggressive and flammable chemicals and pump them from one container to another. You must be curious about how this pump works and why it is the most preferred tool in the chemical industry. Well, this post will answer all your questions.
Understanding Barrel Pump and Its Operating Principles
These pumps are designed for the safe and easy transfer of chemicals from one container to another. They are also known as drum pumps and are available at various tube lengths and as accessories for diversifying industry requirements.
They are centrifugal or displacement pumps with axis control. They consist of a drive shaft, a helical rotor, or a worm screw which is placed in the extremity of the tube, with a motor at the opposite end. When the machinery is started, the pump begins to move and so does the tutor of the screw pump. The rotation of the impeller leads to fluid moving along the axis to the parallel side of the shaft leading to the evacuating of fluid.
These barrels consist of tubes that are designed depending on the size of the container in which the fluid will be pumped. The tool must always be immersed in the fluid to facilitate the priming and operating efficiently.
Characteristics of the Pump
This pump tool offers a huge flow rate and pressure. The high-pressure ones should be preferred viscous liquids (that are thick and have high- resistance to flow like honey and chocolate). The pumping tool can function efficiently with a speed variation, which allows for adjustment of the motor speed.
The discharge height of this type of tool is not high. The type of fluid, dimensions of the container, and the drum are the factors that determine the diameter of the hose, as well as the length of the hose and tube.
Tips to Choose Barrel Pump for Chemical Transfer
The barrel pump has a wide range of applications including food processing, and the oil & fuel industry among others. However, they are the most preferred choice in the chemical industry. They can efficiently transfer the most volatile and toxic chemicals from one container to another. Here are the things that need to be kept in mind while choosing the apt pump for chemical industry.
-
For neutral or slightly volatile liquids, the polypropylene pumps are apt.
-
The PVDF (polyvinylidene fluoride) pump is suitable for highly volatile chemicals or pure acids.
-
For the more viscous liquids, it is best to go for the stainless steel and PTFE (polytetrafluoroethylene).
-
For the highly- corrosive and flammable chemicals, certain barrel pumps meet the ATEX (explosive atmospheres) standards.
When using the pumping tool, it is essential to consult the safety data sheet (SDS) of the chemical products to ensure compatibility of the pump materials and pump fluids.
Benefits of Barrel Pump in the Chemical Industry
There are not one but so many benefits of barrel pumps in the chemical industry. Here are the top 5 listed below.
-
Better Efficiency and Speed of Operations:
These pumps lead to fluent and quick chemical transfer, which increases the speed of the production process. It not only helps keep up with the tight schedules and demands of the customers but also enhances the customers' satisfaction level. In an environment where the demands are constantly on the rise, the ability of the pump to quickly transfer the chemicals from one container and another smoothly.
-
Portable and Reliable:
These barrel pumps are designed to be highly portable, allowing the operators to easily move and even perform the operations outdoors if needed. Apart from that, the barrel pumps are versatile and can easily fit various sizes and ranges of containers, making them a reliable tool for handling different kinds of hostile chemicals.
-
Reduced Labor Cost:
Using the barrel pumps can reduce the cost of hiring labor to execute the task. The laborers have to manually lift and pour the heavy containers. The pumps not only enhance the worker's comfort but also decrease the chance of injuries. The electric ones further elevate the process by increasing the speed of production.
-
Noise Reduction:
This is one of the major overlooked benefits of the barrel pump. This equipment is quiet compared to other pumping operations, leading to a comfortable and peaceful working environment. Noise pollution can also lead to hearing loss among the workers. It will also enhance focus and productivity while promoting the well-being of the employees.
-
Safe Handling of Volatile Chemicals:
Last, but not least, the major benefit of barrel pumps is that they can safely transfer chemicals, which is why they are heavily used in this industry. This industry reduces the chances of chemical spills and accidents. It is essential for maintaining a safe work environment. By investing in a barrel pump, the companies can reduce the chances of accidents to a great extent. The pump is essential for compliance with health and safety regulations in the chemical industry.
Final Words…
The barrel pump is of utmost importance in the chemical industry because it plays a critical role in enhancing operations' safety, efficiency, and productivity. Its ability to efficiently handle toxic and volatile chemicals makes it the most reliable equipment in the chemical processing industry. If you can invest in a high-quality pump from Ceracin, do so. They have a robust body and advanced features, underscoring their importance for safe and reliable operations.
Frequently Asked Questions:
-
What are the kinds of liquids that are barrel pump can handle?
The barrel pumps can handle viscous as well as non-viscous (thin and can easily flow) and semi-viscous fluid (thick) fluids such as oil, diesel, and chemicals.
-
What material is the barrel pump made of?
The pump is made of robust materials like polypropylene (PP), polyvinylidene fluoride (PVDF), stainless steel, and polytetrafluoroethylene (PTFE). It allows the pump to withstand harsh and volatile chemicals easily.
-
How to Choose the Barrel Pump?
Keep these factors in mind while choosing the barrel pump.
-
The type of fluid that will be pumped, its viscosity, temperature, and combustibility.
-
Type of pump you need, be it manual, electric, or pneumatic diaphragm based on the production needs.
-
The size of the container that you are pumping from.
-
The type of motor you need be electric, explosion-proof electric, or air motor depending on the need for efficiency.