A Guide to Load Cells and Its Various Types!
load cell is a force gauge that uses a transducer to generate an electrical signal whose magnitude is proportional to the measured force.
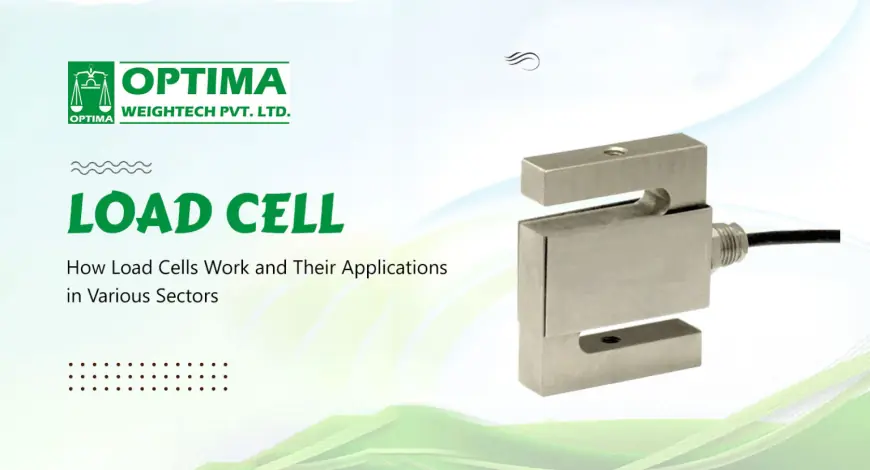
Many people have a morning ritual that includes getting on a scale to check their weight. Most individuals are unaware they use a basic "load cell" to measure their weight.
Weights were employed on old scales to try to level off the two sides of the scale; presently there are techniques that measure weight automatically. The first thing we need to understand about a load sensor is its definition.
A load cell is a force gauge that uses a transducer to generate an electrical signal whose magnitude is proportional to the measured force.
What are the different types of load cells?
These sensors are often classified into four types:
- Pneumatic
- Hydraulic
- Strain Gauge
- Capacitance
Pneumatic load cells.
Let's start by looking at how a pneumatic load cell operates.
Because it is pneumatic, we know it can handle with air pressure. A pneumatic load sensor is made out of an elastic diaphragm attached to a platform surface on which the weight will be measured.
An air regulator will be installed to regulate the flow of air pressure into the system, as well as a pressure gauge. Thus, when an object is put on a pneumatic load sensor, the weight of the object is balanced using pressured air or gas.
The amount of air necessary to balance the weight determines how much the thing weighs. A pressure gauge may translate air pressure readings into electrical signals.
Hydraulic load cells.
The term hydraulic should indicate that this sensor will operate with a fluid, such as water or oil. These load sensors are similar to pneumatic load sensors, except that instead of air, they employ pressurized liquid.
Hydraulic load cells are composed of:
- An elastic diaphragm.
- A piston has a loading platform on top of the diaphragm.
- Oil or water will be within the piston.
- A Bourdon tube pressure gauge.
When a weight is put on the loading platform, the piston exerts pressure on the liquid within it. The liquid's pressure increases in proportion to the supplied force or weight.
After calibrating the pressure, you may precisely measure the force or weight delivered to the hydraulic load sensor. Pressure readings can be viewed as analog gauges or translated into electric signals using a pressure sensor.
Strain Gauge Load Cells
The strain gauge is the next form of load cell. A strain gauge is a transducer that changes electrical resistance in response to stress or strain.
The electrical resistance is proportional to the stress or strain put on the cell, making it simple to calibrate and obtain an accurate result. And, the strain gauge's electrical resistance is linear, so it may be transformed into a force and subsequently, a weight as needed.
A strain gauge load cell consists of four strain gauges arranged in a "Wheatstone" bridge design.
A Wheatstone bridge is an electrical circuit used to measure unknown electrical resistance by balancing two bridge circuit legs, one of which contains the unknown component.
The "Wheatstone Bridge" circuit produces extremely accurate readings. The Wheatstone Bridge's strain gauges are attached to a beam that deforms underweight.
Capacitive load cells.
The last type is a capacitive load sensor. They operate on the idea of capacitance, which is a system's ability to store charge.
This load sensor consists of two flat plates parallel to each other. A current is provided to the plates, and once steady, the charge is stored between them.
Capacitance, or the amount of charge held, is determined by the size of the gap between the plates. When a load is applied on the plate, the gap reduces, resulting in a change in capacitance, which may be calculated into a weight.
Load Cell Applications:
Load sensors are utilized in various industries. Some of these are:
Scales Applications:
Scales are the most typical use for load sensors. These might be any form of scale, including home or bathroom scales, industrial scales, hopper scales, conveyor belt scales, tabletop scales, Motorsport, and many others. A single-point load cell is often utilized in this application.
Marine Applications:
Marine applications demand load sensors that are waterproof and hermetically sealed. Towing, anchor force measurement, line tension on fishing boats and nets, various forms of marine cranes, and dam force measuring are all possible applications for load sensors.
Aerospace Applications:
Load cells are often utilized in aerospace applications for several testing and monitoring purposes, including pre-flight fatigue testing, Aeron force monitoring, flight data recorder applications, and refueling load tests.
Onboard weighing
This is the procedure of weighing the weight of a vehicle while it is already on board. Vehicles that may require this are heavy-duty vehicles including tipper trucks, articulated lorries, agricultural machinery, vans, and automobiles.
Medical Applications:
Load cells can be used for hygiene and other medical purposes, in addition to scales and testing equipment. They must meet a variety of medical requirements before they may be employed in this application.
-
Hydraulics for medical gadgets, beds, and chairs
-
Optical testing measures blood pressure in the human eye.
-
Rehabilitation Equipment: Instrumentation and Force Monitoring
Civil & Infrastructure Applications
Waterproof, flush-mounted designs for the convenience of mounting, most force ranges possible, and to monitor forces in structural projects, such as;
-
Office Buildings and Viaducts
-
Flyovers
-
Transportation infrastructure includes bridges, tunnels, and telemetry.
Conclusion
In this article, we reviewed the four types of load cells. They were:
- Pneumatic
- Hydraulic
- Strain Gauge
- Capacitive.
We also reviewed how a load cell may be utilized in different industrial applications. Finally, keep in mind that the most important element to consider when selecting a load sensor is how accurate and sensitive your application is.