How to Troubleshoot Brushless DC Motors
Incorporating preventive maintenance ensures your BLDC motors remain reliable, efficient, and durable. Armed with these troubleshooting strategies, you’ll be prepared to tackle challenges and keep your systems running at peak performance.
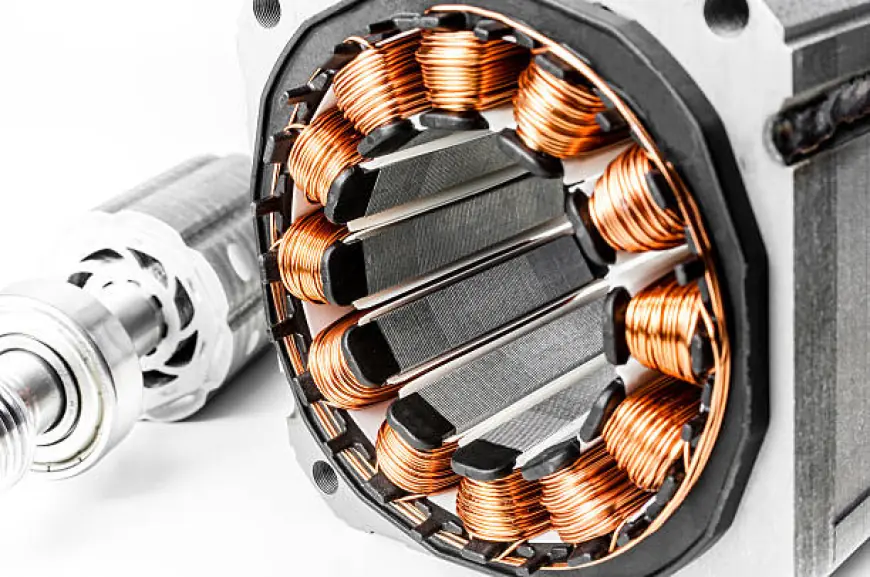
Brushless DC motors are prized their efficiency, reliability, and precision, making them a popular choice in industries ranging from robotics to electric vehicles. But even the best motors can encounter issues over time. Learning how to troubleshoot BLDC motors can help you address problems quickly and keep your systems running smoothly.
This guide covers common issues with BLDC motors, their causes, and step-by-step solutions, along with tips to maintain motor performance and longevity.
What Are Brushless DC Motors?
Before tackling troubleshooting, let’s understand the basics. Unlike brushed motors, BLDC motors use electronic commutation instead of physical brushes, making them quieter, more durable, and less prone to wear.
Key Components:
- Rotor: Houses permanent magnets and rotates.
- Stator: Contains windings that generate the electromagnetic field.
- Controller: Manages electronic commutation and operation.
This design allows for precise control of speed and torque, making BLDC motors ideal for applications demanding accuracy and efficiency.
Common BLDC Motor Issues
Here are some of the most frequent problems you might encounter:
- Motor Fails to Start: Caused by power supply issues, faulty wiring, or a damaged controller.
- Overheating: Results from excessive load, poor cooling, or electrical faults.
- Unusual Noises: Can indicate mechanical misalignment, bearing issues, or rotor imbalances.
- Speed or Torque Irregularities: Often linked to calibration problems, faulty sensors, or controller issues.
- Controller Errors: Misconfigured or damaged controllers can degrade performance or stop the motor entirely.
How to Troubleshoot BLDC Motors
1. Check the Power Supply
Ensure the motor is getting sufficient power. Use a multimeter to verify voltage matches the motor’s specifications.
Look for:
- Loose connections.
- Corroded wires.
- Blown fuses or tripped breakers.
Solution:
Tighten connections, replace damaged components, and stabilize the power supply.
2. Inspect Wiring and Connections
Damaged or improper wiring can disrupt motor function.
Look for:
- Frayed wires or exposed conductors.
- Loose terminals.
- Open or short circuits.
Solution:
Repair or replace wiring and confirm proper connections using the wiring diagram.
3. Test the Motor Controller
A faulty controller can cause erratic operation.
Look for:
- Faulty components in the controller.
- Incorrect configuration settings.
- Voltage errors.
Solution:
Reset the controller to factory settings and reconfigure it. Replace damaged controllers if necessary.
4. Examine Sensors
BLDC motors rely on sensors like Hall sensors for commutation.
Look for:
- Damaged or misaligned sensors.
- Incorrect sensor signals.
Solution:
Test sensors with a multimeter. Replace faulty ones and align them properly.
5. Inspect Mechanical Components
Mechanical issues can disrupt motor performance.
Look for:
- Vibrations or grinding noises.
- Worn bearings.
- Misaligned rotor and stator.
Solution:
Realign components, lubricate moving parts, and replace worn bearings.
6. Analyze the Load
Excessive load can overheat the motor or cause stalling.
Look for:
- High current draw.
- Sluggish operation.
Solution:
Reduce the load or upgrade to a motor with a higher torque rating.
7. Perform Thermal Checks
Overheating can lead to permanent damage.
Look for:
- Hot spots on the motor or controller.
- Blocked vents or poor airflow.
Solution:
Clean vents, improve cooling, and reduce operating cycles if needed.
8. Evaluate Software or Firmware
Outdated or misconfigured software can cause erratic behavior.
Look for:
- Incorrect motor parameters.
- Bugs or glitches in firmware.
Solution:
Update firmware and reconfigure software to match motor specifications.
Preventive Maintenance Tips
Routine maintenance can save you time and money:
- Regularly inspect and clean wiring, connections, and vents.
- Monitor bearings for wear and lubricate as needed.
- Calibrate sensors periodically.
- Check operating temperatures to prevent overheating.
Conclusion
Troubleshooting BLDC motors doesn’t have to be overwhelming. By systematically addressing issues like power supply problems, wiring faults, and mechanical wear, you can restore motor performance and prevent future breakdowns.
Incorporating preventive maintenance ensures your BLDC motors remain reliable, efficient, and durable. Armed with these troubleshooting strategies, you’ll be prepared to tackle challenges and keep your systems running at peak performance.
What's Your Reaction?
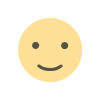
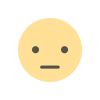
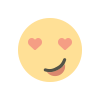
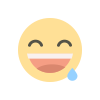
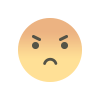
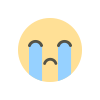
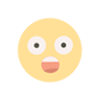