The Inventory Headache: Why Most Contractors Are Still Doing It Wrong
This post highlights common inventory mistakes in construction and how the best software for construction inventory management can streamline processes, reduce costs, and improve efficiency.

Imagine this: You’re deep into a critical phase of your construction project, and suddenly, you realize you’ve run out of materials. The clock is ticking, workers are idle, and project timelines are slipping. A trip to the supplier is your only option but it’s too late.
What should’ve been a smooth operation has now turned into a time-and-money-draining nightmare. Unfortunately, this scenario happens more often than it should.
Did you know that 30% of construction project delays are caused by poor inventory management? Whether it's missing materials, overstocking, or mismanaging resources, inefficient inventory practices can seriously derail a project. The good news? You don’t have to keep making these costly mistakes.
In this post, we’ll dive into why most contractors are still struggling with inventory, the common mistakes they make, and how adopting the best software for construction inventory management can eliminate these headaches, save you time, and reduce costs.
What’s Wrong with Traditional Inventory Management?
For decades, inventory management in the construction industry has been stuck in the past. Paper logs, manual counts, and old-school tracking methods are still the norm for many contractors. While these techniques were effective in the past, they no longer cut it in the fast-paced, modern construction world.
Here’s the issue:
-
Human error and manual tracking lead to inaccurate stock counts.
-
Lost materials can result in delays and increased costs.
-
Inefficient ordering means unnecessary trips to suppliers or wasted storage space.
The real cost of continuing with these outdated methods is significant. It’s time-consuming, costly, and prevents you from making the best decisions for your projects.
Common Mistakes Contractors Make with Inventory
• Mistake #1: Relying on Paper-Based Tracking
It’s easy to see why contractors still cling to paper logs after all, they’ve worked for years. But manual tracking is prone to human error, missing materials, and incomplete records. More importantly, it takes time and energy away from more important tasks.
How it costs time and money:
Paper logs require constant updates and checks. When it’s time for inventory audits, you’ll find yourself scrambling to track down records or make adjustments. This leads to delays and mistakes that cost you both time and money.
• Mistake #2: Failing to Track Usage in Real-Time
Knowing what materials you have is half the battle. The real challenge is tracking how materials are used on-site. Without real-time monitoring, you could run out of materials halfway through the job or, worse, over-order, locking up unnecessary cash flow.
How it costs time and money:
When you don't track material usage as it happens, you risk being blindsided by shortages. This often means sending workers to pick up materials last-minute or paying premium prices for expedited deliveries.
• Mistake #3: Over Ordering and Overstocking
Contractors often overestimate how much material they’ll need, which leads to overordering. The result? You end up with excess materials that eat up storage space and waste precious resources, or worse, materials that expire or become obsolete.
How it costs time and money:
Excess materials not only tie up your cash flow but also increase your storage and management costs. You could’ve spent that money on other aspects of your business—like hiring additional labor or investing in better equipment.
• Mistake #4: Lack of Communication with Suppliers
Poor communication with suppliers is one of the biggest headaches in construction. Materials may arrive late, or worse, not at all, leading to project delays.
How it costs time and money:
When you’re out of sync with suppliers, you risk running out of materials at critical moments. This forces you to rush or source from secondary suppliers at higher prices, both of which delay your timeline and eat into your budget.
4. The High Cost of Inventory Mistakes
The financial impact of poor inventory management is staggering. From wasted materials to inefficiencies in scheduling, every mistake is costly.
Financial Impact:
-
Material shortages lead to unnecessary purchases and delays.
-
Overstocking ties up cash flow, causing storage problems.
-
Late deliveries force you to pay premium prices for expedited materials.
Operational Impact:
-
Inventory errors lead to workflow disruptions.
-
Delays due to missing materials result in frustrated teams and clients.
-
Inefficient ordering creates inventory gaps and contributes to cost overruns.
The Solution: The Best Software for Construction Inventory Management
The answer to all of these problems is simple: invest in the best software for construction inventory management. These modern tools help contractors streamline the entire inventory process, from ordering to tracking to restocking.
How it solves the problem:
-
Real-time updates: Monitor materials as they are used, ensuring you never run out unexpectedly.
-
Automated alerts: Set restock reminders and prevent reordering.
-
Better forecasting: Use historical data to predict material needs and avoid waste.
-
Streamlined communication: Easily share data with suppliers, reducing delays and ensuring timely deliveries.
Benefits:
-
Reduced Costs: Save money by reducing waste and unnecessary purchases.
-
Improved Efficiency: No more manual tracking or guesswork—everything is automated.
-
Better Decision Making: With accurate data at your fingertips, you can make informed decisions about inventory, purchasing, and project scheduling.
Conclusion
Poor inventory management isn’t just a small inconvenience, it's a silent killer of efficiency and profitability in the construction industry. Contractors who still rely on outdated practices like manual tracking, paper logs, and guesswork are setting themselves up for costly mistakes. These errors lead to wasted time, missed opportunities, and project delays, all of which ultimately drain your budget and damage your reputation.
The solution is simple: adopting the software for construction inventory management. By transitioning to a digital inventory system, you gain real-time insights into your materials, streamline communication with suppliers, and ensure your project is always on track. With modern inventory management software, you’ll save money on materials, reduce waste, and improve your team’s productivity.
What's Your Reaction?
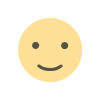
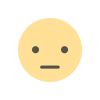
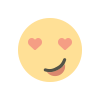
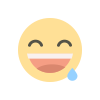
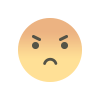
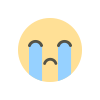
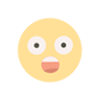