How Do Mobile Compactor Manufacturers Work?
Discover top- quality solutions with Mobile Compactor Manufacturers who specialize in designing and producing innovative, space-saving storage systems.
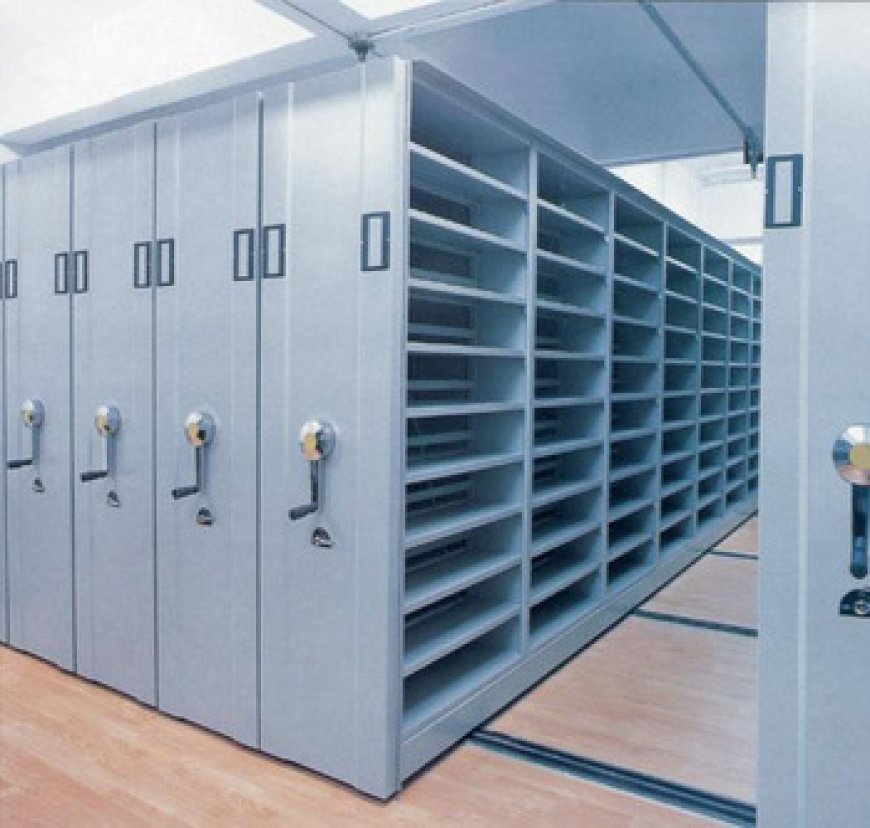
Mobile compactors are smart ways of increasing space utilization and organization in places such as offices, warehouses, libraries, and archive centers, and these compacting systems are built to be portable along specified tracks for easy reach as well as maximum utilization of the space. But, we will look at the procedures that Mobile Compactor Manufacturers use in creating efficient storage facilities. By so doing, we shall be able to unravel how these manufacturers go about creating mobile compactors.
Understanding Mobile Compactors
Before we start making, let's be sure that we really understand what Mobile Compactor Manufacturers are. This is also important because they are very useful in different ways. Mobile compactors refer to portable storage units that move back and forth floor tracks hence dispensing off the requirement for more than one aisle. This design significantly increases storage capacity by allowing units to be compacted together when access is not needed and then moved apart when items need to be retrieved.
Benefits of Mobile Compactors
- Space Efficiency: By eliminating fixed aisles, mobile compactors maximize the use of available space.
- Organization: They provide a neat and organized storage solution, making it easier to locate items.
- Security: Many mobile compactors come with locking mechanisms, ensuring the safety of stored items.
- Versatility: They can store a wide range of items, from documents and books to tools and equipment.
The Manufacturing Process
Creating mobile compactors involves several key steps, each ensuring that the final product is durable, efficient, and tailored to meet specific needs. Here’s a detailed look at how Mobile Compactor Manufacturers work:
1. Design and Planning
Design and planning are the first stages in the manufacturing process. This step is all about knowing the exact storage needs and area restrictions of a client. The producers closely collaborate with customers in order to arrive at the best sizes, structures, and characteristics of the mobile compactor system.
- Needs Assessment: Manufacturers assess the type of items to be stored, the weight capacity required, and any special features needed, such as adjustable shelves or locking mechanisms.
- Space Measurement: Accurate measurements of the storage area are taken to ensure the compactors fit perfectly within the available space.
- Custom Design: Based on the needs assessment and space measurements, a custom design is created. This design includes detailed drawings and specifications for the compactor units.
2. Material Selection
The choice of materials is crucial in manufacturing durable and long-lasting mobile compactors. Mobile Compactor Manufacturers typically use high-quality materials to ensure the strength and durability of the storage units.
- Steel: Steel is commonly used for its strength and durability. It provides a sturdy frame that can support heavy loads.
- Finishes: Manufacturers apply finishes such as powder coating to protect the steel from rust and wear, ensuring a long lifespan.
- Special Materials: Depending on the client's needs, manufacturers may use special materials like stainless steel for environments where hygiene is a priority, or wood for a more aesthetic appeal.
3. Fabrication
Fabrication is the process of converting raw materials into mobile compactor parts. It includes numerous stages to make sure that everything is done with accuracy and to a high quality.
- Cutting and Shaping: The raw materials are cut and shaped according to the design specifications. This includes creating the frames, shelves, and other components.
- Welding and Assembly: The cut pieces are welded and assembled to form the basic structure of the compactor units. Welding ensures the joints are strong and can withstand heavy loads.
- Track Installation: Tracks are a crucial part of the system, allowing the compactor units to move smoothly. Manufacturers install tracks on the floor or within the storage units as per the design.
4. Quality Control
Quality control is an essential step to ensure that mobile compactors meet the highest standards of durability and functionality. Mobile Compactor Manufacturers conduct rigorous testing and inspections at various stages of the manufacturing process.
- Structural Integrity: The compactor units are tested for structural integrity to ensure they can support the specified weight.
- Smooth Operation: The movement of the compactor units along the tracks is tested to ensure smooth and easy operation.
- Safety Features: Any safety features, such as locking mechanisms, are thoroughly tested to ensure they function correctly.
5. Customization and Finishing
Following the establishment and assessment of the mobile compactors for performance, they can be further tailored and completed. Such enhancements give the units a desired design and result.
- Adjustable Shelves: If adjustable shelves are required, they are installed at this stage, allowing for flexible storage options.
- Locking Mechanisms: Any locking mechanisms or security features are installed to ensure the safety of stored items.
- Aesthetic Finishes: The compactor units are finished with the desired colors, textures, or additional aesthetic features as per the client’s preferences.
6. Delivery and Installation
After the mobile compactors are manufactured and customized, they are prepared for delivery and installation. Mobile Compactor Manufacturers often offer professional installation services to ensure the units are set up correctly and function efficiently.
- Packaging: The compactor units are carefully packaged to prevent any damage during transportation.
- Delivery: The units are delivered to the client’s location as per the agreed schedule.
- Professional Installation: A team of skilled installers sets up the mobile compactor system, ensuring it operates smoothly and efficiently. They also provide training on how to use and maintain the system.
7. Ongoing Support and Maintenance
A good relationship with Mobile Compactor Manufacturers doesn’t end with the installation. Manufacturers often provide ongoing support and maintenance services to ensure the system continues to function optimally.
- Regular Maintenance: To prevent the compactor units from being damaged, the manufacturers may provide maintenance services. The services will also involve lubricating the moving parts and looking for tear and wear.
- Technical Support: Clients can contact manufacturers for technical support if any issues arise with the compactor system.
- Upgrades and Modifications: As storage needs change, providers of such services might offer their consumers enhancements or alterations in the current infrastructure so that they can keep pace with what they demand.
Conclusion
The activities of mobile compactor manufacturers contribute significantly to the development of effective and compact storage systems. Prior to actual designing, through to construction, modification, and installation, every stage of manufacturing takes place with top levels of notice placed to eventual product ensure perfection in terms of quality and use. By understanding the needs of their clients and using high-quality materials, manufacturers create durable and versatile mobile compactor systems that optimize storage space and improve organization.
If this is your very first introduction to industrial storage or an upgrade is what you need, then receiving insight on how mobile compactor manufacturers operate can enable you to make better judgment calls when selecting from among available alternatives that suit your requirements.