Key Factors to Consider When Choosing Inconel 718 Round Bars for Your Projects
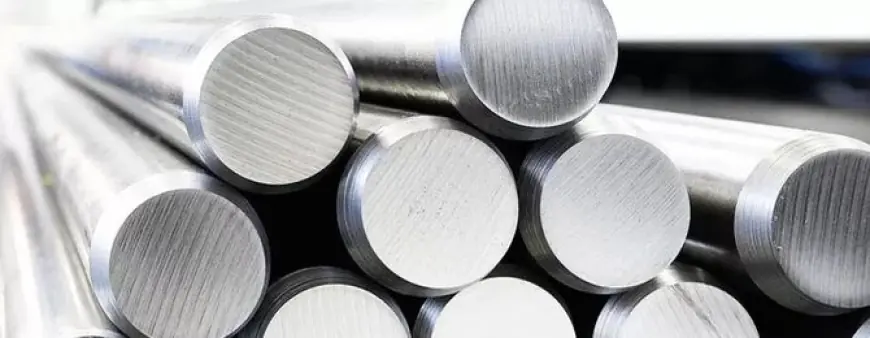
When it comes to selecting materials for high-performance applications, 718 Inconel round bars often emerge as a top choice due to their unique properties and versatility. Used across various industries, these bars are celebrated for their strength, corrosion resistance, and ability to endure extreme temperatures. However, selecting the right Alloy 718 round bars requires careful consideration of several factors to ensure they align with the requirements of your specific project. Below, we’ll explore the critical aspects you need to know to make an informed decision.
What is Inconel 718?
Inconel 718, also known as UNS N07718, is a nickel-based superalloy designed to provide exceptional performance under extreme conditions. Its remarkable combination of strength, corrosion resistance, and heat resistance makes it an ideal material for critical engineering applications. This alloy contains a balanced composition of nickel, chromium, iron, and other elements, delivering superior mechanical properties.
One of the standout features of 718 Inconel round bars is their ability to maintain high tensile, creep, and rupture strength at temperatures up to 700°C (1290°F). Additionally, they remain highly resistant to oxidation, pitting, and stress-corrosion cracking, making them a dependable choice for rigorous environments.
Properties and Benefits of 718 Inconel Round Bars
1. High Strength and Durability
Inconel 718 round bars are renowned for their exceptional strength. Thanks to precipitation hardening, these bars maintain excellent mechanical integrity, even under high-stress or high-temperature conditions.
2. Outstanding Corrosion Resistance
The nickel-chromium combination in Alloy 718 round bars makes them resistant to a wide range of corrosive environments, including oxidizing and reducing conditions. This property is particularly crucial for applications exposed to chemicals, saltwater, or high humidity.
3. Thermal Stability
718 Inconel round bars retain their structural integrity at extreme temperatures. Unlike many other materials, they do not deform, weaken, or fail under thermal stress, which is a critical requirement in industries such as aerospace and power generation.
4. Ease of Workability
Despite being a tough alloy, Alloy 718 round bars offer excellent workability. They can be welded, machined, or formed with relative ease compared to other nickel-based alloys, providing flexibility during fabrication.
Applications of Inconel 718 Round Bars in Various Industries
Given their impressive combination of properties, 718 Inconel round bars find extensive use in industries that demand reliability and performance. These include:
Aerospace
The aerospace sector heavily relies on Alloy 718 round bars for engines, turbines, and other critical components that require high strength, heat resistance, and corrosion resistance.
Oil and Gas
Inconel 718 round bars are integral to the oil and gas industry, particularly in downhole tools, subsea components, and piping systems that operate under highly corrosive and high-pressure environments.
Power Generation
Turbines, reactor cores, and other power generation equipment benefit from the thermal and mechanical stability of 718 Inconel round bars, ensuring long-term performance with minimal maintenance.
Marine Engineering
Saltwater environments are highly corrosive, but Alloy 718 round bars excel in such conditions, making them a dependable material for offshore and marine applications, such as propeller shafts and fasteners.
Automotive and Chemical Processes
High-temperature and corrosive conditions in chemical plants and automotive exhaust systems necessitate the use of durable materials like 718 Inconel round bars, ensuring safety and longevity.
Factors to Consider When Choosing 718 Inconel Round Bars
When selecting 718 Inconel round bars for your project, it’s vital to evaluate the following factors:
1. Application Requirements
Understand the specific needs of your project. Consider whether the application involves exposure to extreme temperatures, corrosive chemicals, or high mechanical stress. Alloy 718 round bars are versatile, but identifying your requirements helps ensure optimal material performance.
2. Bar Dimensions and Specifications
Accurate dimensions, such as diameter and length, are critical for the seamless integration of 718 Inconel round bars into your project. Ensure the supplier provides bars that meet your exact specifications and tolerances.
3. Material Certification
To guarantee the authenticity and quality of the Alloy 718 round bars, check for certifications such as ASTM B637 or EN 10088-2 standards. Genuine materials certified by reliable organizations ensure consistent performance and safety.
4. Supplier Reputation
Partnering with a trusted supplier is essential. Evaluate the supplier’s track record, customer reviews, and quality assurance processes to ensure you receive premium-grade 718 Inconel round bars.
5. Price and Budget
While 718 Inconel round bars may seem costlier upfront compared to other alternatives, their long-term reliability and reduced maintenance costs often justify the investment. However, always balance quality with budget constraints.
6. Customization Options
Some projects may require custom sizes, finishes, or treatments for Alloy 718 round bars. Ensure the supplier offers customization services to cater to these unique needs.
Summing Up
What's Your Reaction?
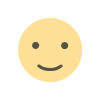
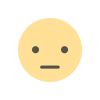
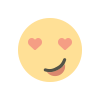
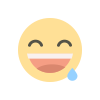
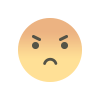
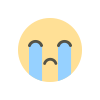
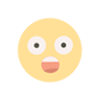