The Importance of Coalescing Filters in Industrial Filtration
Coalescing Filters
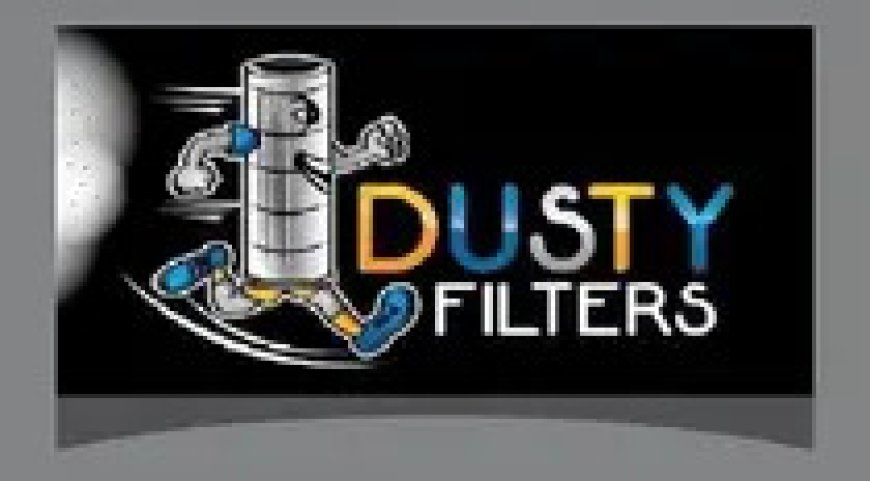
Various manufacturing processes require industrial filtration systems, and within these systems, coalescing filters have a significant role to play. They are designed for separating liquids from gases as well as isolating them into different chambers thus making them suitable in the oil, gas and petrochemical industries.
How Do Coalescing Filters Work?
Coalescing filters work on two different stages: one is where they separate liquids and gases while the other purifies the gas of any impurities. When the mixture enters the filter, liquid separates from gas as they go through it, with the liquid flowing along fine fibers of an inner layer forming larger drops. These big drops are then gotten rid of by gravity flow, resulting in pure dry gas. The second stage involves purification where impurities are removed from this gas leading to a clean and dry final product.
Benefits of Coalescing Filters
Industrial filtration systems enjoy numerous advantages derived from using coalescing filters. Liquids and gases can be removed from products prior to storage thus protecting equipment against corrosion. Moreover, coalescing filters can remove impurities and contaminants hence improving quality of the final product. Also, these devices lower maintenance costs by prolonging equipment lifespans due to less repair’s necessity.
Applying Coalescing Filters
Coalescing filters are regularly used in the oil, gas and petrochemical industries. In the oil business, coalescing filters are used to take out water from an oil/water mix. They take away fuel from a fuel/water mix in the fuel industry. Gas coalescence filters are for separating gases from gas/fuel or gas/water mixes. Another use of coalescing filters is in petrochemical industry where water vapor is removed from the product before storage.
Choosing The Correct Coalescing Filter
To select a suitable coalescing filter, you have to consider what your application wants specifically. The design should be one that can handle both flow rate and pressure drop within system; material should also be compatible with material under filtration while simple cleaning and maintenance is crucial as well as low-pressure drops but high-efficiency ratings for this filter type.