What are Different Types of Gear Coupling and How to Choose It?
Gear couplings link any two shafts. The type of coupling chosen is heavily influenced by the intricacy of the connection, the power to be conveyed, and the application region.
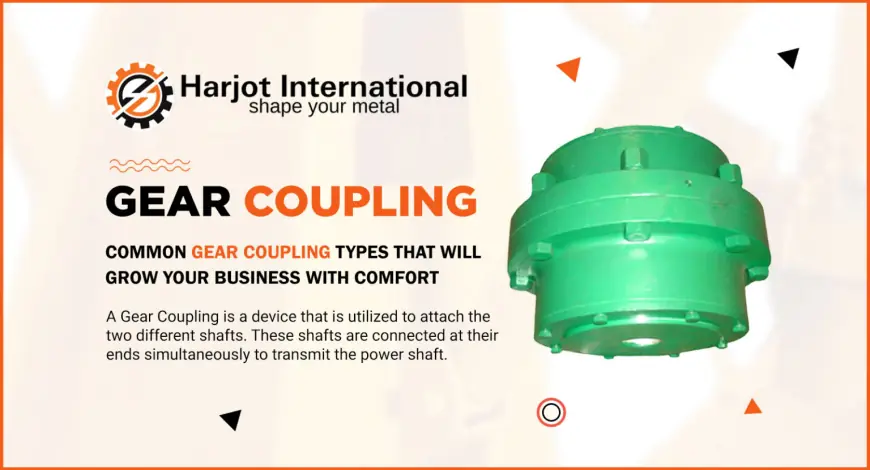
Gear couplings are devices that link the ends of two shafts to convey power. Couplings do not often disengage or allow couplings to disconnect from shafts during operation; nevertheless, there are a few torque-limiting couplings that slide or disconnect when a torque limit is exceeded or if a problem arises.
The basic function of couplings is to unite two spinning objects while allowing for some degree of misalignment or movement at one or both ends.
Carefully selecting the connection based on the requirements, together with good installation, can result in much lower maintenance costs and downtime.
There are two types of coupling: mechanical and material flexing. Flexible materials gain their flexibility by compressing and stretching robust materials such as rubber or bending thin metallic discs or grids.
Material-flexing couplings do not require lubrication. There are a few exceptions to grid coupling. All metal mechanical flexing couplings require lubrication.
About Gear Coupling
A coupling is a mechanical device used to link the ends of nearby pieces or items.
Gear couplings link any two shafts. The type of coupling chosen is heavily influenced by the intricacy of the connection, the power to be conveyed, and the application region.
Couplings are flexible couplings that can transmit extremely high torques. Gear engineering plays an important part in using the benefits of gear coupling. In practical use, the coupling is a full-gear unit.
Construction of the Gear Coupling
The gear couplings are made of a forged sleeve with teeth cut on the inside. Sleeves are typically made up of two pieces, each with inner gears.
In most circumstances, the created sleeve will remain a single piece.
Two center points with outer teeth comprising an equal number of teeth as in the inner apparatus are provided, with each being installed on the determined and driven shafts individually.
The tooth profile of the exterior teeth is frequently delegated in order to take up larger loads.
Lubrication attachments are provided at strategic spots to grease the couplings throughout predetermined periods of time.
There are three types of external teeth used in gear couplings, with the sole variation being the manufacturing methods.
Crowning with varying radius
The exterior teeth are barrel-shaped, having a differential radius rather than a relatively uniform radius. In comparison to constant radius crowning, this greatly increases the contact area.
Crowning at a fixed radius
The exterior teeth are barrel-shaped with a set radius to improve the area of contact and bring it closer to the middle of the teeth.
Straight teeth.
The exterior teeth of the hub are straight. If the coupling becomes misaligned, the contact pattern between the external and internal gears tends to be in a line of contact.
How to Buy the Right Gear Coupling?
Choosing the best coupling for the project at hand necessitates asking the right questions before specifying a specific form. There are several options, and using multiple types of coupling might be suitable for any specific application.
Here are several things to look for when selecting the correct gear coupling:
Do not let habit or price be a determining factor.
Companies frequently pick a coupling style based on having used the same type in a prior project. However, because not all couplings are established on the same level, it is always necessary to combine coupling competence with equipment based on expertise. Another source of the issue is the ability to couple based on price rather than output criteria. Engineers, motivated by a desire to save machinery costs, might abbreviate the application by being overly frugal in their coupling selection. Although this method reduces the initial cost of components, protracted and costly backend warranty claims can hurt the OEM's bottom line and the commodity's reputation.
Identify the correct way to mount the gear coupling on the shaft.
The mechanism by which the coupling is placed on the shaft can decide the success or failure of the coupling, independent of whether the coupling is adequate for operation. Common buttons, keyways, and taper bushes work well in unidirectional applications with minimal shock or reversal stresses.
Keyless locking systems are the best mounting technique for reversing loads and shock installations since they have no backlash. For example, installing a torsionally stable, backlash-free, high-speed disc coupling with a keyway and a set screw undermines the coupling's backlash-free characteristics. A keyless locking mechanism would assist the coupler perform its intended function. However, given the coupling's rough and flexible construction, attaching a highly flexible jaw coupling with a keyless locking mechanism may be overkill.
Determine the requirements of the gear coupling.
Perhaps the most crucial question is, "What does this coupling need to do?"
Other concerns include if it needs to transmit high or low torque. Is the procedure performed at high or low speed? Do you need to be maintenance-free? How about some free backlash? Are there any discrepancies between the elements to be paid for and how much? Will the programming require coupling in order to survive the shock? How high is the cost? What is the weight? What about environmental circumstances, such? What about external factors such as air temperature, humidity, and corrosion?
Knowing the answers to these questions in relation to the application, as well as cross-referencing the relevant couplings, will assist in determining the most appropriate coupling for the application. Remember that more than one type of coupling can operate.
Proper installation is crucial.
Choosing the appropriate pairing for an application might be a dynamic activity, but it does not need much time. The ideal strategy is to pay careful attention to all design criteria. This often includes pressure, shaft misalignment, stiffness, RPM, inertia, volume requirements, and shaft mounting. Finally, a coupling that addresses all of these difficulties will function well in the application.
Conclusion
With our comprehensive guide, choosing the appropriate gear coupling has never been easier! Simply follow the instructions, and you will undoubtedly find the finest quality coupling that will endure for years.