Upgrading Your Conveyor System: When to Switch to a Custom Solution
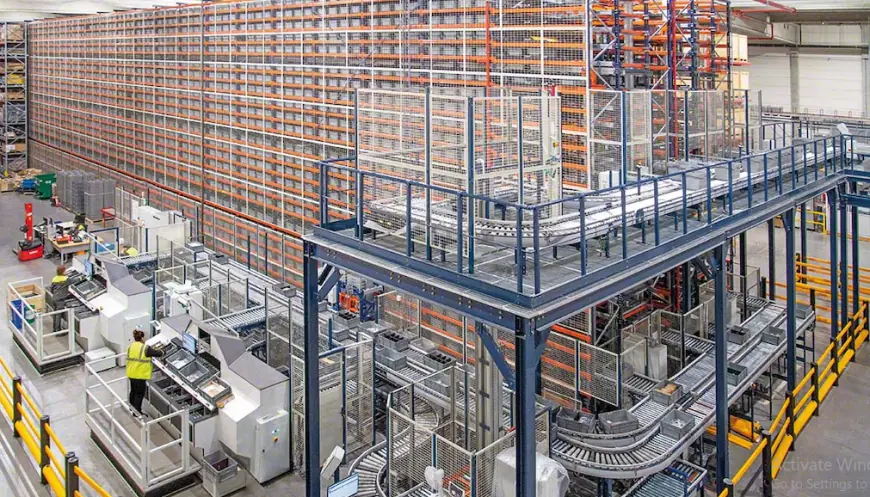
When your conveyor system is constantly breaking down, slowing down production, or struggling to keep up with new materials and order volumes, it’s more than just a minor inconvenience but a bottleneck that could be costing you money. If you're spending more time fixing your system than using it, it might be time to consider a custom conveyor solution.
Signs That Your Current Conveyor System Is No Longer Efficient
Over time, conveyor systems wear down, become outdated, or fail to meet changing operational demands. Here’s how to know when it’s time for an upgrade:
1. Frequent Breakdowns and High Maintenance Costs
If your maintenance team constantly replaces parts, adjusts belts, or troubleshoots unexpected stoppages, your conveyor is costing more than it's worth. The more time spent on repairs, the less time your system spends moving products efficiently. A custom warehouse conveyor system designed for your workload and materials reduces downtime and extends the lifespan of critical components.
2. Bottlenecks and Slow Throughput
Conveyors should speed up operations, not slow them down. If products are backing up, waiting to be sorted, or moving inconsistently, your system may not be designed for your current capacity. A custom conveyor solution optimizes flow and eliminates unnecessary delays, ensuring products move efficiently through the system.
3. Inability to Handle New Products or Materials
Standard conveyors are built for general applications, but what happens when your business introduces heavier products, fragile materials, or unique packaging? If your conveyor struggles with product stability, spacing, or handling, a custom solution with adjustable speeds, specialized surfaces, or different belt types can prevent product damage and improve efficiency.
4. Lack of Flexibility in Workflow
A rigid conveyor system can limit your ability to scale. If you’re expanding operations, changing warehouse layouts, or increasing production, you need an adaptable warehouse conveyor system. Modular custom conveyors allow for future adjustments, giving you the flexibility to grow without replacing your entire system.
5. Safety and Compliance Concerns
Older conveyors often lack updated safety features, putting workers at risk. An upgrade becomes essential if your system is missing emergency stop mechanisms, proper guarding, or OSHA-compliant safety measures. A custom conveyor system can be designed with built-in safety mechanisms to reduce risks and meet compliance standards.
Advantages of Switching to a Custom Conveyor System
A custom warehouse conveyor system is built around your specific operational needs, not just a one-size-fits-all approach. Instead of forcing an outdated system to work harder than it should, a well-designed upgrade improves efficiency, accuracy, and long-term cost savings.
Beyond increasing speed and reducing maintenance costs, custom conveyors are built for your products, space, and automation requirements. A custom setup ensures everything runs smoothly if you need a system that integrates with AI, robotics, or warehouse management software. It also improves energy efficiency, using optimized motors and belt materials to lower power consumption.
Before upgrading, analyze your current system’s weak points. Where is it failing? What processes need improvement? A custom solution should solve specific challenges, reducing manual labor, improving throughput, or accommodating new product lines.
Working with experienced conveyor belt manufacturers is key. They’ll assess your warehouse layout, production requirements, and future expansion plans to ensure the right materials, components, and system design are chosen to optimize your entire workflow.
Integration with existing technology is another important consideration. A custom conveyor should work properly with automation, inventory tracking, and sorting systems to create a fully connected, high-efficiency operation. Investing in a solution that supports growth ensures long-term scalability and cost-effectiveness.
Even the best conveyor system won’t perform well if it’s poorly designed or installed incorrectly. A professionally planned system considers weight distribution, belt tension, and operational efficiency to ensure everything runs smoothly from day one. Poor installation leads to misalignment, excessive wear, and frequent breakdowns, defeating the purpose of an upgrade.
High-quality materials and engineering matter just as much as the layout. Durable rollers, energy-efficient motors, and reinforced frames help extend the system’s lifespan and reduce maintenance costs. Choosing trusted conveyor belt manufacturers ensures that every part of the conveyor is built to last and designed for maximum efficiency.
Proper installation also ensures compliance with OSHA and industry safety standards. A well-installed conveyor system reduces workplace hazards, minimizes accidents, and keeps employees safe while improving productivity.