Types of Rolling Mill Rolls and Their Applications in Steel Manufacturing
In this article, we will explore the various types of rolling mill rolls and their applications in steel manufacturing.
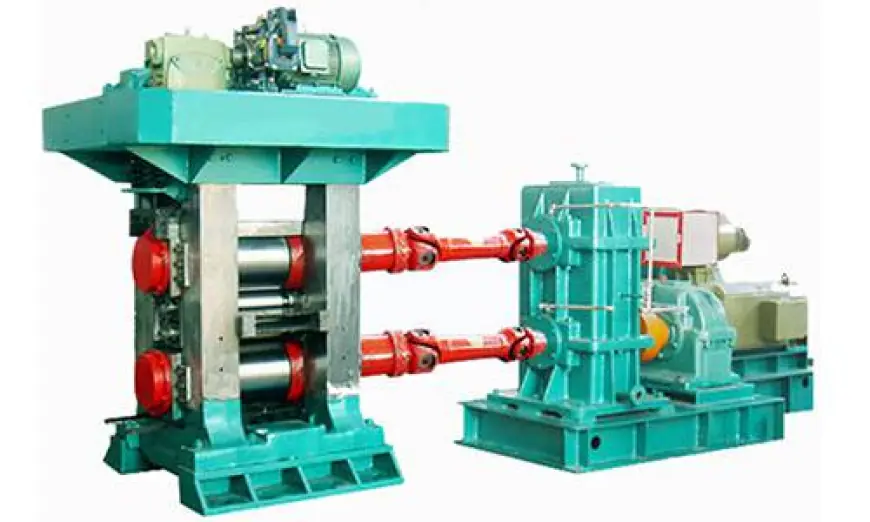
In steel manufacturing, rolling mills are essential for shaping and processing steel into various products such as sheets, strips, bars, and rods. At the heart of any rolling mill is the rolling mill roll. These cylindrical tools apply pressure to the steel to reduce its thickness, elongate it, and modify its shape. The type of roll used in the mill is critical for the quality, efficiency, and cost-effectiveness of the production process. In this article, we will explore the various types of rolling mill rolls and their applications in steel manufacturing.
1. Overview of Rolling Mill Rolls
Rolling mill rolls are used in the metal forming process, where steel billets or slabs are passed through a set of rotating rolls to reduce their thickness and modify their shape. The rolls play an essential role in controlling the material's dimensions, surface finish, and mechanical properties. These rolls must withstand high forces, extreme temperatures, and intense wear, making material selection and design crucial for optimal performance.
There are different types of rolls used in rolling mills, each designed for specific functions within the rolling process. The most common types include work rolls, backup rolls, feeder rolls, and support rolls. Understanding each roll's function and the materials used for their construction helps ensure that the right type of roll is selected for each task.
2. Work Rolls
Work rolls are the primary rolls in a rolling mill that directly interact with the material being processed. These rolls are responsible for applying the compressive forces that reduce the thickness of the steel as it passes through the mill. Work rolls are subjected to high levels of stress, friction, and temperature, so their design must ensure both strength and durability.
Applications of Work Rolls:
- Hot Rolling: Work rolls are essential in hot rolling mills, where steel billets are heated to high temperatures (typically 1,000°C to 1,200°C) and passed through the mill to produce plates, sheets, or coils. The work rolls must withstand thermal stresses and wear during this process.
- Cold Rolling: In cold rolling, the steel is processed at or near room temperature. Work rolls are crucial in producing thin, high-precision sheets or strips of steel, with applications in automotive parts, electrical appliances, and other industries requiring precise material properties.
Materials Used for Work Rolls:
Work rolls are generally made from high-carbon steel, alloy steels, or composite materials that combine the benefits of different metals. Alloying elements such as chromium, molybdenum, and vanadium are commonly used to increase wear resistance, strength, and heat resistance. Work rolls also often undergo heat treatment processes to enhance their hardness and performance.
3. Backup Rolls
Backup rolls are larger, stronger rolls that support the work rolls and help maintain their position and alignment. These rolls do not come into direct contact with the steel but are crucial for providing the necessary pressure to ensure that the work rolls do not deflect under load. Backup rolls are especially important in tandem rolling mills, where multiple rolls are used in sequence.
Applications of Backup Rolls:
- Support for Work Rolls: Backup rolls support the work rolls and prevent excessive deflection, ensuring uniform pressure on the steel and minimizing any deformation during the rolling process.
- Improved Dimensional Control: By maintaining proper alignment, backup rolls help achieve precise thickness control and consistent product quality.
Materials Used for Backup Rolls:
Backup rolls are typically made from high-strength cast steel or cast iron, which offers excellent durability and resistance to wear. While the materials are not subjected to the extreme temperatures seen by the work rolls, they must still withstand significant mechanical forces.
4. Feeder Rolls
Feeder rolls, sometimes called entry rolls, are used to guide the steel material into the rolling mill. These rolls control the material's entry speed and ensure that it is properly aligned before it reaches the work rolls. Feeder rolls are essential in maintaining the flow of material through the mill and ensuring consistent processing.
Applications of Feeder Rolls:
- Material Entry: Feeder rolls direct the incoming steel billets or slabs into the rolling mill, ensuring a smooth entry without misalignment.
- Material Speed Control: These rolls help regulate the speed at which the material enters the mill, allowing for better control over the final dimensions and surface quality.
Materials Used for Feeder Rolls:
Feeder rolls are typically made from high-carbon steel or high-strength alloys that offer good wear resistance and strength. The material used must be able to withstand the abrasive nature of steel and the friction involved in feeding the material into the mill.
5. Support Rolls
Support rolls are used in rolling mills to support the overall structure of the mill and hold the work and backup rolls in place. These rolls do not engage directly with the steel but provide the necessary structural support to keep the rolls aligned and ensure consistent performance. Support rolls are found in various configurations depending on the type of rolling mill.
Applications of Support Rolls:
- Roll Alignment: Support rolls ensure that the work and backup rolls remain properly aligned during the rolling process, preventing issues like uneven material thickness or roll deflection.
- Structural Support: These rolls also contribute to the overall stability of the rolling mill, which is vital for maintaining product quality and efficiency.
Materials Used for Support Rolls:
Support rolls are typically made from cast iron or high-strength steel. The material must be able to withstand the weight of the rolls and provide adequate stability to prevent vibrations or misalignment during the rolling process.
6. Other Specialized Rolls
In addition to the common types of rolls discussed above, various other specialized rolls are used in specific applications within the steel industry. These include:
- Coating Rolls: Coating rolls are used in mills that produce coated steel products, such as galvanized steel. These rolls apply coatings such as zinc or paint to the steel surface to improve corrosion resistance.
- Sizing Rolls: Sizing rolls are used in the final stages of the rolling process to fine-tune the steel's dimensions, ensuring that it meets precise thickness requirements.
- Stretching Rolls: Stretching rolls are used in mills designed to elongate steel to achieve the desired length, especially for products like wire and rods.
7. Conclusion
Rolling mill rolls are essential components in the steel manufacturing process. Each type of roll, including work rolls, backup rolls, feeder rolls, support rolls, and specialized rolls, plays a critical role in shaping and processing steel to meet the required specifications. The materials used to manufacture these rolls must offer exceptional strength, wear resistance, heat resistance, and durability to ensure consistent performance under extreme conditions.
Choosing the right type of roll for each application is crucial to achieving the desired product quality, dimensional accuracy, and efficiency in the rolling process. As technology advances and the demand for higher-quality steel products continues to grow, the role of rolling mill rolls will remain central to the success of steel manufacturing operations worldwide. Understanding the various types of rolls and their applications ensures that manufacturers can select the best tools for each job, optimizing their production processes and delivering high-quality steel products.
Tinvo is a professional sourcing and service company specializing in accessories for steel rolling mills. The company primarily focuses on providing various types of mill rolls, metallurgical steel rolling blades, and other essential components for the industry.