Praseodymium Neodymium Alloy Production Process with Cost Analysis
The Praseodymium Neodymium Alloy Production Process with Cost Analysis offers a comprehensive look into the production of one of the most crucial materials used in the manufacturing of high-performance magnets.
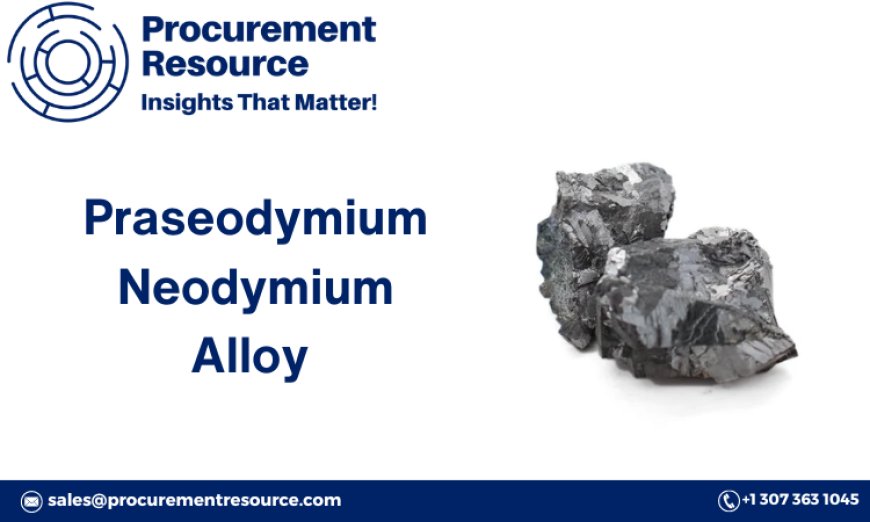
Introduction
The Praseodymium Neodymium Alloy Production Process with Cost Analysis offers a comprehensive look into the production of one of the most crucial materials used in the manufacturing of high-performance magnets. These magnets are widely employed in industries such as renewable energy, electric vehicles, and consumer electronics. This report explores the key stages involved in the production of praseodymium neodymium alloys, the procurement of resources, market drivers, raw material requirements, costs, and other critical process information. A personalized report tailored to your business can help in optimizing production efficiency and controlling costs.
Request For Free Sample: https://www.procurementresource.com/production-cost-report-store/praseodymium-neodymium-alloy/request-sample
Procurement Resource Assessment for Praseodymium Neodymium Alloy Production Process
The procurement of resources is a fundamental part of producing praseodymium neodymium alloys. This assessment involves analyzing the supply chain, sourcing rare earth elements, and ensuring regulatory compliance while maintaining cost-efficiency in production.
1. Sourcing Rare Earth Elements (REEs)
Praseodymium and neodymium are two rare earth elements (REEs) that are primarily sourced from mining operations. The most prominent sources of these elements are in regions like China, which dominates the global supply chain for REEs. A successful procurement strategy must account for geopolitical factors, potential supply chain disruptions, and competitive pricing from suppliers.
2. Supply Chain Management
Effective supply chain management ensures a consistent flow of rare earth elements into the production process. Efficient logistics are critical for minimizing delays, ensuring continuous production, and maintaining cost control. Partnerships with trusted mining companies and distributors are crucial for securing high-quality raw materials.
3. Process Optimization Technologies
Implementing advanced technologies such as automated refining and material separation can help improve yield and reduce waste during the production process. Optimized processes lead to better quality alloys and lower production costs, contributing to enhanced profitability.
4. Regulatory Compliance
The extraction and refinement of rare earth elements are subject to strict environmental regulations. Ensuring compliance with international environmental and safety standards is crucial. Non-compliance can result in production delays, fines, and damage to the company's reputation.
5. Cost Control Strategies
Optimizing procurement strategies by securing long-term contracts, negotiating bulk purchase discounts, and diversifying suppliers can help in controlling costs. A focus on cost-effective shipping and handling is also important to avoid escalating logistics expenses.
Understanding Praseodymium Neodymium Alloy
Praseodymium neodymium alloy, commonly referred to as NdPr alloy, is a critical material used in producing high-strength permanent magnets. These magnets, made from neodymium, iron, and boron (NdFeB), are widely regarded as the strongest commercial magnets available and are used in numerous applications such as electric motors, wind turbines, and various electronic devices.
Praseodymium and neodymium, being part of the lanthanide series, exhibit strong magnetic properties, which make them ideal for producing NdFeB magnets. The alloying of these two rare earth elements enhances the performance of these magnets, especially in terms of heat resistance and magnetic field strength.
Praseodymium Neodymium Alloy Production Process
The production of praseodymium neodymium alloy involves several key stages:
-
Extraction of Rare Earth Oxides: The first step in producing praseodymium neodymium alloy is the extraction of praseodymium and neodymium from rare earth ores. These ores undergo beneficiation processes, such as flotation, to increase the concentration of the rare earth elements. Following beneficiation, the ore is roasted and leached to separate the desired elements.
-
Separation of Praseodymium and Neodymium Oxides: The separated oxides of praseodymium and neodymium are further purified using solvent extraction techniques. The resulting oxides are of high purity and are used in the alloying process.
-
Reduction and Alloying: The purified oxides are reduced to their metallic form using reducing agents like calcium or magnesium in a high-temperature furnace. The metals are then alloyed by melting them together in an induction furnace under a controlled atmosphere to prevent oxidation.
-
Casting and Processing: The molten alloy is cast into ingots or blocks, which can then be processed further depending on the application. This may involve shaping, machining, or surface treatments.
-
Quality Control: The final alloy undergoes rigorous testing to ensure that it meets the required standards for purity, composition, and magnetic properties. Quality control is essential to guarantee the alloy's performance in industrial applications.
Market Drivers for Praseodymium Neodymium Alloy
Several market drivers contribute to the growing demand for praseodymium neodymium alloy:
-
Increasing Demand for Electric Vehicles (EVs): The global push towards electric vehicles is a significant driver for praseodymium neodymium alloy demand. NdFeB magnets are essential components in the motors of electric vehicles due to their high power density and efficiency. As the adoption of EVs accelerates, so does the need for praseodymium neodymium alloy.
-
Renewable Energy Expansion: Wind turbines, particularly those utilizing direct-drive systems, rely on powerful NdFeB magnets for efficient energy conversion. With the global emphasis on transitioning to renewable energy sources, the demand for praseodymium neodymium alloy in the wind energy sector is set to grow.
-
Consumer Electronics Growth: The increasing production of smartphones, laptops, and other electronic devices that use high-performance magnets further drives the demand for praseodymium neodymium alloys. These magnets are used in speakers, hard drives, and other critical components due to their superior strength.
-
Government Initiatives for Sustainable Energy: Various governments around the world are providing incentives and support for industries that contribute to reducing carbon emissions. The use of praseodymium neodymium alloy in clean energy technologies such as electric vehicles and wind turbines aligns with these initiatives, boosting market demand.
-
Technological Advancements in Magnet Production: Innovations in magnet production, such as 3D printing of NdFeB magnets and the development of stronger, lighter alloys, are creating new opportunities for the praseodymium neodymium alloy market.
Raw Materials Requirements for Praseodymium Neodymium Alloy Production
The production of praseodymium neodymium alloy requires several critical raw materials:
-
Praseodymium Oxide (Pr₂O₃): Praseodymium oxide is a primary raw material for alloy production. It is extracted from rare earth ores and purified before being reduced to its metallic form for alloying.
-
Neodymium Oxide (Nd₂O₃): Similar to praseodymium, neodymium oxide is a key raw material. Its magnetic properties make it the backbone of NdFeB magnets. Neodymium oxide is separated and purified before alloying.
-
Reducing Agents: Reducing agents like calcium or magnesium are used to reduce praseodymium and neodymium oxides to their metallic forms. These agents are consumed in the reduction process and play a critical role in the overall production cost.
-
Energy: High amounts of energy are required to power the furnaces used in the reduction and alloying processes. Maintaining efficient energy use is essential to keep production costs in check.
-
Protective Gases: Inert gases, such as argon, are used to maintain a controlled atmosphere during alloying to prevent oxidation, ensuring the purity and quality of the final product.
Costs and Key Process Information
The production of praseodymium neodymium alloy involves several cost components that contribute to the overall cost structure:
1. Raw Material Costs
The cost of rare earth elements, particularly praseodymium and neodymium oxides, represents a significant portion of the production cost. The price of these oxides fluctuates based on supply and demand factors, geopolitical issues, and the availability of rare earth ores. Securing a reliable and cost-effective supply of raw materials is essential for controlling production costs.
2. Energy Costs
Energy consumption during the reduction, alloying, and casting stages is substantial. High-temperature furnaces are required to convert oxides to metal and to melt the alloy. Efficient energy use and employing renewable energy sources where possible can help reduce costs.
3. Labor and Equipment Costs
Skilled labor is necessary to operate and monitor the production processes. In addition, the production of praseodymium neodymium alloy requires specialized equipment such as furnaces, casting machines, and purification units. The costs associated with purchasing, maintaining, and upgrading this equipment must be accounted for.
4. Regulatory Compliance and Environmental Costs
Mining, refining, and processing rare earth elements come with strict environmental regulations due to their environmental impact. Companies must ensure compliance with environmental laws, waste management practices, and occupational safety standards, all of which add to production costs.
5. Logistics and Transportation Costs
Transporting rare earth elements from mining locations to production facilities and delivering the final alloy to customers incurs logistics costs. Securing efficient and cost-effective transportation solutions is crucial to minimizing overall expenses.
Looking for an Exhaustive and Personalized Report?
If you're looking for an exhaustive and personalized report on the Praseodymium Neodymium Alloy Production Process with Cost Analysis, we offer comprehensive insights tailored to your specific business requirements. Our customized reports provide detailed information on procurement strategies, cost-saving opportunities, market trends, and the latest technological advancements. Whether you're involved in manufacturing, raw material procurement, or supply chain management, our report will help you make informed decisions that significantly substantiate your business.
About Us:
Procurement Resource is an invaluable partner for businesses seeking comprehensive market research and strategic insights across a spectrum of industries. With a repository of over 500 chemicals, commodities, and utilities, updated regularly, they offer a cost-effective solution for diverse procurement needs. Their team of seasoned analysts conducts thorough research, delivering clients with up-to-date market reports, cost models, price analysis, and category insights.
By tracking prices and production costs across various goods and commodities, Procurement Resource ensures clients receive the latest and most reliable data. Collaborating with procurement teams across industries, they provide real-time facts and pioneering practices to streamline procurement processes and enable informed decision-making. Procurement Resource empowers clients to navigate complex supply chains, understand industry trends, and develop strategies for sustainable growth.
Contact Us:
Company Name: Procurement Resource
Contact Person: Benking sley
Email: sales@procurementresource.com
Toll Free Number: USA & Canada - Phone no: +1 307 363 1045 | UK - Phone no: +44 7537 132103 | Asia-Pacific (APAC) - Phone no: +91 1203185500
Address: 30 North Gould Street, Sheridan, WY 82801, USA