Jute Bag Manufacturing Plant Project Report 2025: Technical, Financial, and Operational Insights
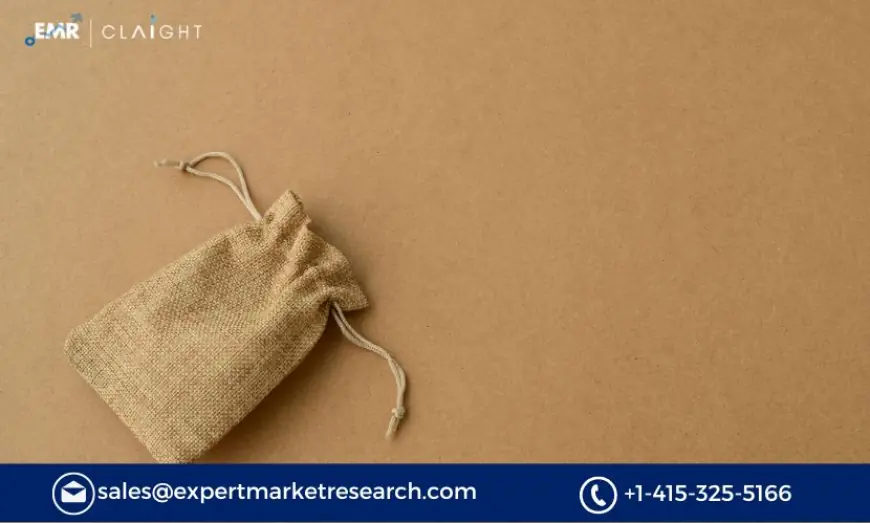
Introduction
Jute bags, often referred to as burlap bags, are sustainable, biodegradable, and environmentally friendly products made from the natural fiber of the jute plant. With growing concerns about plastic pollution and environmental sustainability, the demand for jute bags has surged. These bags are not only eco-friendly but also durable, versatile, and widely used across different sectors such as retail, agriculture, and packaging. The Jute Bag Manufacturing Plant Project Report provides an in-depth understanding of the factors involved in establishing a jute bag manufacturing unit. It outlines the complete production process, from sourcing raw jute to the final packaging of jute bags. The report also highlights market trends, cost estimates, financial planning, and the necessary regulatory standards for setting up the plant.
Given the increasing demand for eco-friendly alternatives to plastic products, establishing a jute bag manufacturing plant presents an excellent business opportunity with significant market potential.
Market Demand and Trends
The demand for jute bags is primarily driven by the global shift towards sustainability and reducing plastic waste. The following factors contribute to the growing market demand:
-
Environmental Concerns: Increasing environmental awareness and concerns over plastic pollution have pushed governments, businesses, and consumers to adopt eco-friendly products. Jute bags, being biodegradable and recyclable, are considered a green alternative to plastic bags.
-
Government Regulations: Many countries have implemented strict regulations to ban or reduce the usage of plastic bags, promoting the use of natural fiber products such as jute bags. In some regions, jute bags are even promoted as a substitute for single-use plastic bags.
-
Consumer Awareness: With growing environmental consciousness, consumers are becoming more inclined toward sustainable products. As a result, there is an increasing demand for jute bags in retail stores, supermarkets, and online platforms.
-
Versatility of Jute Bags: Jute bags are used across various sectors, including retail, grocery shopping, agriculture, and packaging. They are popular in the fashion industry for making stylish handbags, totes, and promotional bags.
-
Export Potential: Due to their environmental benefits and durability, jute bags have high export potential, especially in developed markets like the USA, Europe, and Japan, where demand for sustainable products is on the rise.
-
Branding Opportunities: Jute bags are widely used for branding and promotional purposes, with businesses printing logos, slogans, and messages on them. This offers a lucrative market for custom-made jute bags.
The growing awareness of sustainability, coupled with governmental regulations against plastic, makes jute bag manufacturing an attractive investment opportunity.
Get a Free Sample Report with Table of Contents@
Raw Materials and Sourcing
The primary raw material required for jute bag manufacturing is jute, a natural fiber obtained from the jute plant. Below are the key raw materials and their sources:
-
Jute Fiber: Jute is the main material used in the production of jute bags. It is a strong, durable, and biodegradable fiber extracted from the jute plant. Jute is cultivated primarily in tropical countries, particularly in India and Bangladesh, which are the largest producers of jute.
-
Dye and Printing Materials: To enhance the visual appeal of jute bags, dyes, and printing materials are used for coloring and printing logos, patterns, and designs on the bags. These materials must be eco-friendly to maintain the sustainability aspect of jute bags.
-
Thread and Stitching Materials: Thread is used to stitch the jute fabric into bags. The type of thread may vary based on the design and strength requirements. Polyester and cotton threads are commonly used.
-
Packaging Materials: For packaging the finished bags, materials such as paper bags, cardboard boxes, or plastic covers (for export) are required to ensure the bags are delivered in good condition.
-
Glue and Adhesives: Eco-friendly adhesives may be used in the manufacturing process to bond the fabric or components together in specific designs.
Sourcing high-quality jute and other raw materials is essential to ensure that the finished products meet industry standards and customer expectations.
Manufacturing Process
The manufacturing process of jute bags involves several steps, including raw material preparation, weaving, stitching, dyeing, and packaging. Below is a breakdown of the key stages:
1. Preparation of Raw Jute Fiber
The raw jute fibers are processed to remove impurities such as dirt, dust, and plant residues. This process includes:
- Cleaning: The jute fibers are cleaned using water to remove impurities.
- Carding: The fibers are carded to separate and align them, making them ready for spinning.
2. Spinning
The clean, carded fibers are spun into yarn. The yarn is then wound into spools and is ready to be used in the weaving process.
- Spinning Machines: Spinning machines are used to convert jute fibers into yarn of desired thickness and strength.
3. Weaving or Knitting
The yarn is woven into fabric using a loom or knitting machines. The fabric's thickness and texture depend on the specific design requirements of the jute bags.
- Weaving Loom: Weaving machines are used to produce jute fabric of the required length and width.
4. Dyeing and Printing
The woven jute fabric is then dyed to achieve the desired color. Eco-friendly dyes are used to maintain the sustainability aspect of the product. The bags are also printed with logos, patterns, and designs if required by the customer.
- Dyeing Tanks: Dyeing machines are used to achieve uniform color throughout the fabric.
- Printing Machines: Printing is done using screen printing or digital printing methods, depending on the design complexity.
5. Cutting and Stitching
Once the fabric is ready, it is cut into the required sizes for making the bags. The pieces are then stitched together using industrial sewing machines to form the shape of the jute bags.
- Cutting Machines: Automatic cutting machines are used for precise cutting of the fabric.
- Sewing Machines: Heavy-duty industrial sewing machines are used to stitch the pieces into bags.
6. Finishing and Quality Control
After stitching, the bags are finished with additional features such as handles, zippers, or pockets. A final quality control check is done to ensure the bags meet the required standards for strength, stitching, and finishing.
- Inspection: A thorough quality check is conducted to identify defects or inconsistencies in stitching, size, or design.
7. Packaging
Finally, the finished jute bags are packed for distribution. Depending on the requirements, the bags are either packed in bulk or in retail-ready packaging.
- Packaging Machines: Automatic packaging machines are used for wrapping and sealing the bags for storage and shipping.
Infrastructure and Equipment
Setting up a Jute Bag Manufacturing Plant requires the following infrastructure and equipment:
- Production Facility: A clean and spacious production facility with adequate lighting, ventilation, and storage areas for raw materials and finished products.
- Weaving Looms: Automatic or semi-automatic looms for weaving the jute fibers into fabric.
- Spinning Machines: Machines for spinning raw jute fibers into yarn.
- Dyeing and Printing Machines: Equipment for dyeing the jute fabric and printing designs or logos on the bags.
- Cutting Machines: Automated cutting machines for precise cutting of the fabric into the required size for the bags.
- Sewing Machines: Industrial sewing machines for stitching the bags.
- Packaging Machines: Machines for packing the bags into bulk packaging or retail packaging.
- Quality Control Laboratory: A laboratory for testing the strength, durability, and quality of the jute bags.
Cost Analysis and Financial Planning
The costs involved in setting up a Jute Bag Manufacturing Plant can be broken down into two main categories:
-
Capital Investment:
- Land and facility construction or rental.
- Purchase of machinery and equipment (weaving looms, spinning machines, dyeing machines, etc.).
- Setup of a quality control laboratory.
- Licensing and regulatory approvals.
-
Operating Costs:
- Raw material costs (jute fiber, dyes, threads, etc.).
- Labor costs for workers, supervisors, and quality control staff.
- Utility costs (electricity, water, fuel).
- Maintenance costs for machinery and equipment.
- Packaging and shipping expenses.
-
Revenue Generation:
- The primary source of revenue will be from the sale of jute bags to wholesalers, retailers, and businesses looking for eco-friendly packaging solutions.
- The profitability will depend on production capacity, market demand, and pricing strategies.
Regulatory Compliance and Environmental Considerations
- Regulatory Compliance: The manufacturing plant must adhere to local and international standards for textile manufacturing, including environmental regulations and worker safety guidelines.
- Environmental Impact: The facility must implement sustainable practices, such as recycling water used in dyeing and ensuring that waste materials are properly disposed of or repurposed.
- Waste Management: A robust waste management system should be in place to handle any waste generated during production, including fiber dust and packaging waste.
Media Contact
Company Name: Claight Corporation
Contact Person: Lewis Fernandas, Corporate Sales Specialist — U.S.A.
Email: sales@expertmarketresearch.com
Toll Free Number: +1–415–325–5166 | +44–702–402–5790
Address: 30 North Gould Street, Sheridan, WY 82801, USA
Website: www.expertmarketresearch.com
Aus Site: https://www.expertmarketresearch.com.au