Tips to Operate an Industrial Furnace Safely
The industrial furnace is crucial for melting and processing materials, but its high heat can cause accidents. Proper training, inspections, ventilation, and maintenance ensure its longer life.
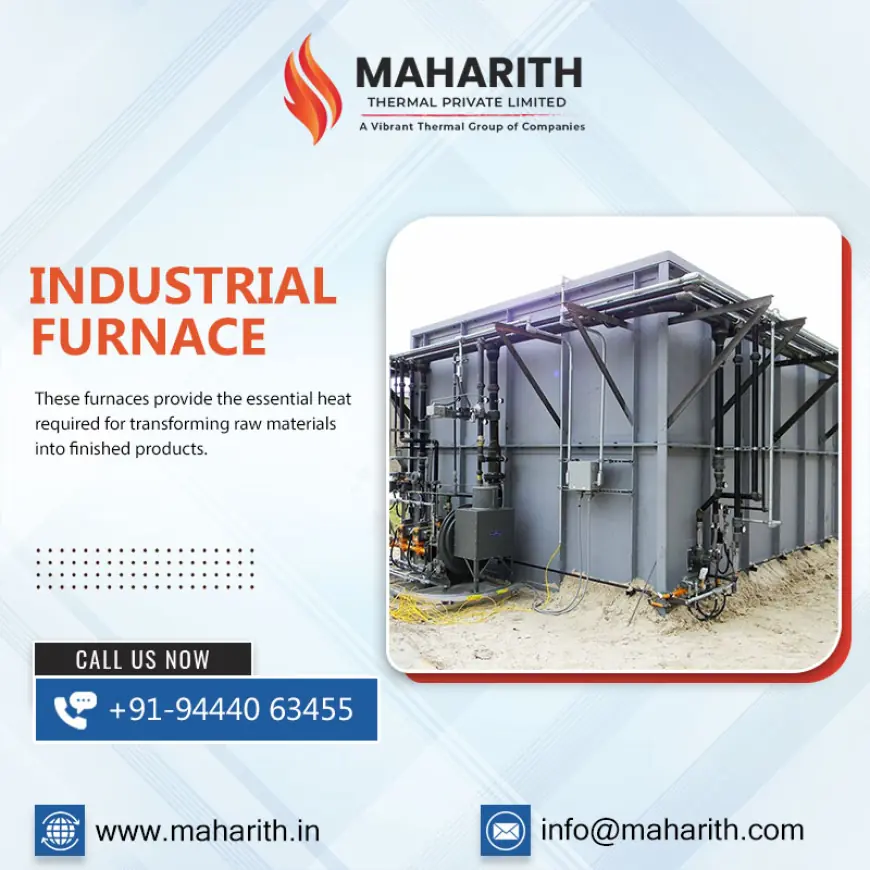
The industrial furnace is an essential device that generates heat to melt, and process various materials, including chemicals, food, and machinery parts. Its heat can reach 400 degrees Celsius. Depending on its type and purpose, the industrial furnace is a versatile product used in various industries. It operates by heating different materials to high temperatures.
There are many kinds of heating furnaces, and their heating sources can vary depending on their type and purpose. Earlier, wood and coal were the main sources of heat, but with time, electric industrial furnaces have replaced them all. They are an efficient and quick way of conducting operations. However, because they generate an extreme level of heat, it becomes essential to avoid accidents and explosions. In this post, we will list the major safety tips that must be remembered for smooth yet safe operations.
Important Tips to Use Industrial Furnaces Safely
Using Protective Gears:
For starters, it is essential to have a personal safety kit to avoid injuries while operating the industrial furnace. The heating equipment is prone to explosions and thus high-quality personal protective equipment (P.P.E) must be provided to every worker around. It consists of heat-resistant clothing, gloves, goggles, jackets, coveralls, and face shields among others. Using these precautions will decrease the chances of tragic consequences.
Proper Training:
The industrial furnace is not just for starters, so it is vital to get training to workers before they start operating the machinery. It should be the responsibility of the management to either hire the experienced workers or train the new ones. Regular training programs must be conducted for the industrial operators so that they are aware of all the safety measures like how to use the personal protective equipment (P.P.E), understand emergencies, as well as to conduct routine inspections. This way the workers will be prepared for unseen challenges and will be able to operate the industrial furnace smoothly.
Regular Monitoring:
The responsibility of industrial furnace safety operations is not just limited to the workers, there should also be a team to conduct regular inspections. Regular inspection is very helpful as it helps in assessing the industrial components, evaluating the performance as well as detecting the wear-tear at an early stage. The inspection also improves the efficiency of operations, and durability of the machinery apart from the worker's safety.
It is vital to check the industrial furnace before the operations and also talk to the operators for feedback. It will keep you aware of the situation of the industrial furnace and also be prepared for repairs if needed.
Ventilation:
The industrial furnace generates a tremendous amount of heat. The entire process of melting and process of the components can lead to the accumulation of huge amounts of dust and gases along with extreme heat. It can be a deadly combination leading to health issues as well as serious health concerns for the workers. So, it is important to have proper ventilation in the place where the machinery is installed. They play an extremely important role in evicting the polluted air and maintaining safe air quality.
Combustible Materials:
The industrial furnace is extremely prone to fire breakouts and explosions. Therefore, it is essential to ensure that any flammable product is not close to the furnace. It should be the duty of workers to ensure that such products are kept far away from the heating equipment. By continuous monitoring during the operations, the chances of accidents can be reduced, ensuring safe and smooth operations.
Temperature Monitoring:
The industrial furnace can go up to extreme temperatures of about 400 degrees Celsius. If the temperature goes out of control, it can cause a lot of damage, thus it is important to control the heat. Many advanced industrial furnaces have temperature sensors that immediately notify about the temperature increase. Apart from that cooling systems and emergency shutdowns will also ensure safe operations. The best way is to integrate temperature monitoring into the machinery for seamless coordination and better efficiency.
Parting Words….
The industrial furnace is a versatile heating equipment that is used in a wide range of industries. The materials can be efficiently heated here to get the outcome of choice. However, operating the furnace has its share of risks. So, to minimize these risks, proper safety tips must be followed. Hopefully, the tips mentioned above will be of great help.
Apart from following the above-mentioned tips, you should also invest in a leading brand of industrial furnaces like Maharith Thermal Pvt. Ltd. Engineered with precision and innovation, these furnaces provide high-level performance, reliability, and efficiency. It will also help you safeguard your work- environment as it undergoes rigorous testing and inspection for smooth and secure operations.
Frequently Asked Questions:
-
What are the applications of industrial furnaces?
The furnace is used to heat and process various raw materials. They are used in many industries like automobile, manufacturing as well as chemicals.
-
What are the safety features that an industrial furnace must have?
The industrial furnace needs to have emergency shutdowns, cooling sensors, and temperature regulators that will ensure smooth and safe operations.
-
How to pick the right industrial furnace?
When you are choosing an industrial furnace, you should consider things like the raw materials that you want to process, the production rate, and the desired temperature.
-
How much does an industrial furnace cost?
Each of the furnaces is designed to meet the specific requirements. So, the features and sizes of each heating equipment are different, thus the price also varies accordingly.
-
What is the average lifespan of an industrial furnace?
A well-maintained industrial furnace can last up to 15- 20 years.
-
What are the factors that can affect the performance of the furnace?
Many factors can affect the performance of the industrial furnace like the capacity utilization of the machinery, air- ratio as well as final heating temperature.
-
How long can an industrial furnace run in one go?
If there are no extreme temperatures involved, the furnace can run 10- 15 minutes per cycle. The furnace needs to be run 2- 3 times an hour to achieve the desired temperature and outcome of product processing.