Exploring the Technological Evolution of CNC Machining
One of the most significant advancements in the evolution of CNC machining came in the 1970s with the development of microprocessors.
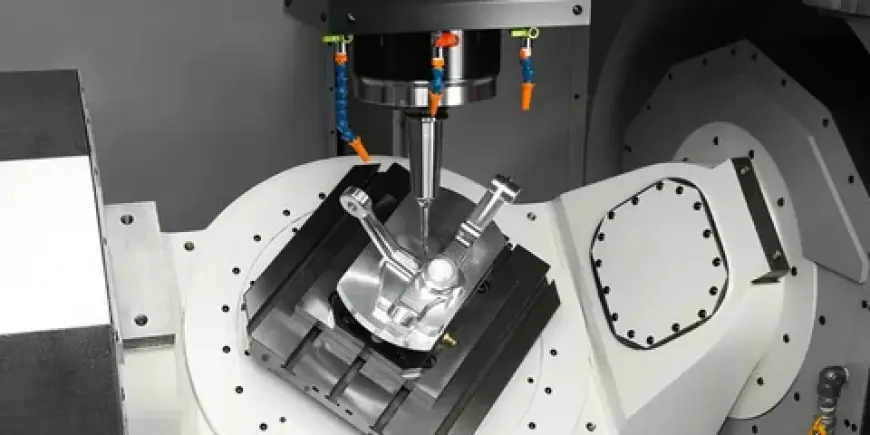
The manufacturing industry has undergone tremendous changes over the past century, largely driven by the evolution of technology. One of the most pivotal technological advancements that have shaped the industry is the development of CNC (Computer Numerical Control) machining. Initially seen as a futuristic concept, CNC machining has transformed the way industries approach manufacturing, bringing about more precision, efficiency, and cost-effectiveness. In this article, we will explore the evolution of CNC machining, highlighting its historical development, key technological advancements, current applications, and the potential future trajectory.
The Birth of CNC Machining: From Manual to Automated Processes
The concept of CNC machining is rooted in the early days of automation and numerical control (NC) systems. In the 1940s and 1950s, engineers began experimenting with using punched paper tapes to control machines. These early systems, known as numerical control machines, were primitive but laid the foundation for what would later become the modern CNC machining systems. Before this innovation, machining was done manually, which required skilled operators to control machine tools by hand, often leading to human error and inefficiencies.
In the 1960s, the advent of digital computers marked a significant milestone in the evolution of CNC machining. Researchers developed machines that could be programmed using punch cards and computers, which drastically improved the speed and precision of operations. The first CNC machines were introduced, offering a more automated process with enhanced accuracy compared to manual methods. These systems could execute a series of commands with minimal human intervention, setting the stage for the rapid development of CNC technology over the next few decades.
The Rise of Microprocessors: A Game-Changer for Precision and Control
One of the most significant advancements in the evolution of CNC machining came in the 1970s with the development of microprocessors. Microprocessors allowed machines to become even more precise and versatile, opening the doors for more complex and intricate machining tasks. This development not only improved the accuracy of the machines but also reduced the size and cost of CNC systems, making them more accessible to a broader range of industries.
The integration of microprocessors into CNC machines meant that programs could be stored and retrieved more easily, offering significant improvements in operational efficiency. CNC machines could now handle more complicated geometries and produce complex parts with greater repeatability. This development also made CNC machining systems more user-friendly, as operators could store and modify programs without having to reprogram them manually for each part. These advancements paved the way for CNC machines to become the backbone of modern manufacturing across industries such as aerospace, automotive, and medical devices.
The Advent of 3D Modeling and CAM Software
As technology continued to advance, so did the capabilities of CNC machines. In the 1990s, the introduction of Computer-Aided Design (CAD) and Computer-Aided Manufacturing (CAM) software revolutionized the way CNC machines were programmed. CAD software allowed engineers and designers to create detailed 3D models of the parts they wanted to manufacture, while CAM software translated these designs into machine-readable code, optimizing the manufacturing process.
The integration of CAD and CAM systems into CNC machining allowed for greater design flexibility and improved accuracy. Previously, creating a prototype or part involved labor-intensive manual processes or simple drawings that could not easily be modified. With CAD and CAM software, design changes could be made in real-time, streamlining the production process and reducing the likelihood of errors. This evolution significantly reduced the lead time for product development and allowed manufacturers to produce parts with highly complex geometries that were previously impossible to achieve with traditional machining methods.
The Role of Automation and Robotics in CNC Machining
The evolution of CNC machining has been closely tied to the rise of automation and robotics, which have further expanded the capabilities of CNC systems. By the late 1990s and early 2000s, automation became a significant trend in the machining industry. Robotic arms were integrated into CNC machines, enabling the automation of material handling, part loading and unloading, and even the inspection of finished products.
The integration of robotics into CNC machining systems allowed for 24/7 production capabilities, reducing human labor and the risk of errors. Robots could perform tasks such as moving parts between different stages of the production process without the need for manual intervention. This automation also resulted in higher throughput, lower labor costs, and the ability to produce high volumes of parts in a shorter time frame. As robotic systems became more advanced, they were further integrated with CNC machines, resulting in highly automated and efficient manufacturing processes.
The Future of CNC Machining: AI, IoT, and Beyond
Looking ahead, the future of CNC machining promises even greater advancements with the integration of Artificial Intelligence (AI) and the Internet of Things (IoT). These technologies are set to enhance the performance, efficiency, and versatility of CNC systems even further. AI algorithms will enable CNC machines to learn from past operations, making real-time adjustments and predictions to optimize machining processes. This could lead to significant improvements in predictive maintenance, reducing downtime and extending the lifespan of CNC equipment.
The integration of IoT into CNC systems will also enable real-time monitoring of machine performance, allowing manufacturers to track key metrics such as tool wear, temperature, and power consumption. With the ability to collect and analyze data from various machines, manufacturers will have a wealth of insights at their disposal to enhance production efficiency. Furthermore, IoT-connected CNC machines will allow for remote monitoring and control, enabling operators to make adjustments from anywhere in the world. As these technologies evolve, CNC machining will continue to play a pivotal role in shaping the future of manufacturing, driving innovation and improving production capabilities across industries.
Conclusion
The evolution of CNC machining has been a journey of continuous technological advancements that have transformed the manufacturing landscape. From its humble beginnings as a manually controlled process to the sophisticated, automated systems we have today, CNC machining has reshaped the way we design, produce, and deliver products. As we look to the future, emerging technologies such as AI, IoT, and robotics promise to take CNC machining to new heights, further enhancing precision, efficiency, and innovation.
As industries continue to embrace these advancements, the role of CNC machining in modern manufacturing will only become more central. By providing faster turnaround times, improved product quality, and cost savings, CNC machines are enabling manufacturers to meet the increasingly complex demands of today's market. The continued evolution of CNC machining will not only drive progress within the manufacturing sector but also push the boundaries of what is possible in product design and production, shaping the future of industries worldwide.