Challenges of Modular Construction You Should Know
Be more sure in your decision to choose modular construction by also knowing the challenges that come with it.
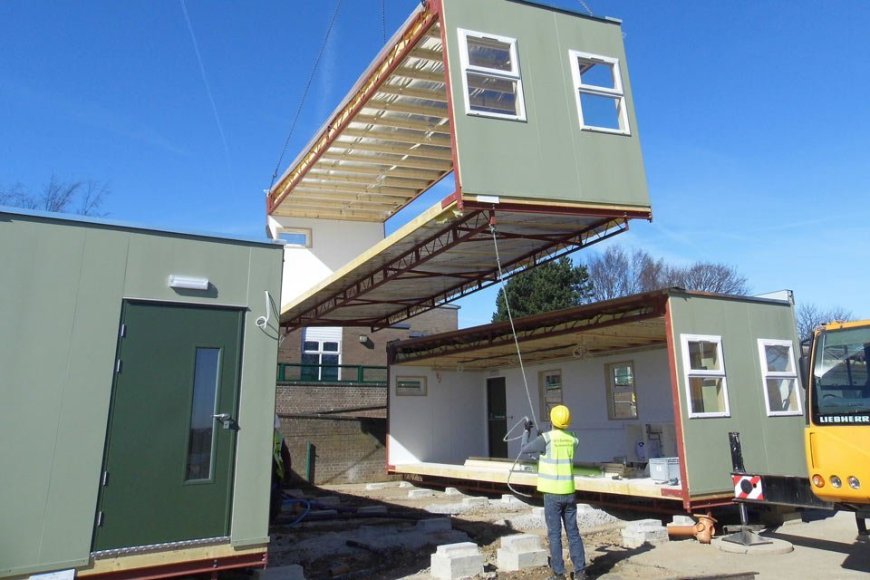
Are you considering modular construction for your next structural project? Then keep reading! Modular buildings are quite popular for being a sustainable, time-efficient and affordable form of structure that people consider–may it be for residential, storage, medical and many other purposes.
But even with a handful of benefits that come with modular construction, it also has its fair share of disadvantages. So before making any big decisions, you should know the challenges associated with modular construction–the list is below:
1 - Design Limitations
Although economical, modular construction places restrictions on design since it uses standardised pieces. The lack of flexibility and customisation resulting from this standardisation makes it difficult for architects and designers to create intricate or distinctive architectural designs.
When consistency is prioritised above originality, it might be challenging to include unique elements or unconventional forms. Module dimensions are further limited by transport size and weight restrictions, which affect spatial configurations.
Usable internal space is frequently reduced by the need for extra reinforcements to ensure structural integrity during transit. Adhering to local building requirements might complicate the design process and require thorough planning to achieve seamless integration of modules at connection points.
2 - Transportation and Logistics
There are a lot of logistics and transportation issues with modular construction. Transporting modules from the manufacturer to the building site imposes size and weight constraints that may limit the flexibility of the design.
The need for unique permissions and routes for oversized modules may raise expenses and complicate logistics. There may be more difficulties while navigating via cities or challenging terrain. Careful handling and sturdy packaging are necessary to ensure that modules arrive undamaged; any damage sustained in transportation may cause delays and additional costs.
Furthermore, careful logistical planning and administration are required to coordinate the timely supply of modules by building deadlines.
3 - Site Constraints
Site restrictions in modular construction might reduce productivity and should be carefully considered. Compact spaces, particularly in cities, can make it difficult to assemble bigger modules and need careful logistical planning for crane access and shipping.
Module installation may be complicated by site features like uneven terrain or limited access. The smooth integration of utilities and existing infrastructure necessitates coordination between site preparations and modular componentry.
Complicating matters further is making sure local laws and licences are followed. To maximise the advantages of modular construction while minimising logistical and operational challenges, overcoming these limitations necessitates careful site evaluation and strategic planning.
4 - Regulatory and Compliance Issues
Modular construction regulations and compliance concerns include strict compliance with construction codes and standards. To guarantee structural integrity and safety, each modular component needs to comply with local requirements, which call for extensive examinations and certifications.
The design and implementation of projects become more difficult when zoning rules, environmental restrictions, and fire safety requirements are followed. To successfully manage permit needs and approval procedures, coordination with regulatory agencies and stakeholders is crucial.
During the production and construction stages, careful documentation, engineering validation, and adherence to quality assurance methods are necessary to guarantee that modular designs comply with these legal frameworks.
5 - Coordination and Integration
In modular construction, integration and coordination are essential for a smooth project's completion. Architects, engineers, manufacturers, and workers in construction must communicate effectively with one another.
The first step is meticulous planning to coordinate site preparation, transit logistics, and module manufacture. To ensure structural integrity and operation, the exact positioning of modular parts during installation necessitates painstaking coordination.
To prevent conflicts and guarantee efficiency, the integration of mechanical, electrical, plumbing, and HVAC systems in modules necessitates meticulous design and installation. To maximise construction processes and provide high-quality results in modular construction projects, rapid problem-solving and modification are made easier by ongoing communication throughout the project's lifetime.
6 - Supply Chain Dependencies
Modular construction has considerable hurdles due to supply chain reliance. Project timelines rely heavily on the timely supply of supplies, parts, and completed modules. Production schedules might be impacted and expenses can rise due to disruptions like supplier delays or shortages.
Maintaining a smooth operation and guaranteeing quality standards requires coordination between many manufacturers and suppliers. Any irregularity in the logistics of the supply chain may result in delays in the assembly and installation of modules at the location.
To mitigate these issues and maximise efficiency in modular construction projects, strong contingency planning, supplier diversity, and proactive procurement process management are necessary to protect against any interruptions.
Take away
So whether you’re planning to use modular buildings as modular healthcare buildings, as storage, as a home, an office and so on, you’re still not excepted from experiencing these challenges.