Why CNC Machines Are Essential for High-Quality Production
CNC machines provide unparalleled precision, ensuring that every part produced is consistent and meets strict tolerances.
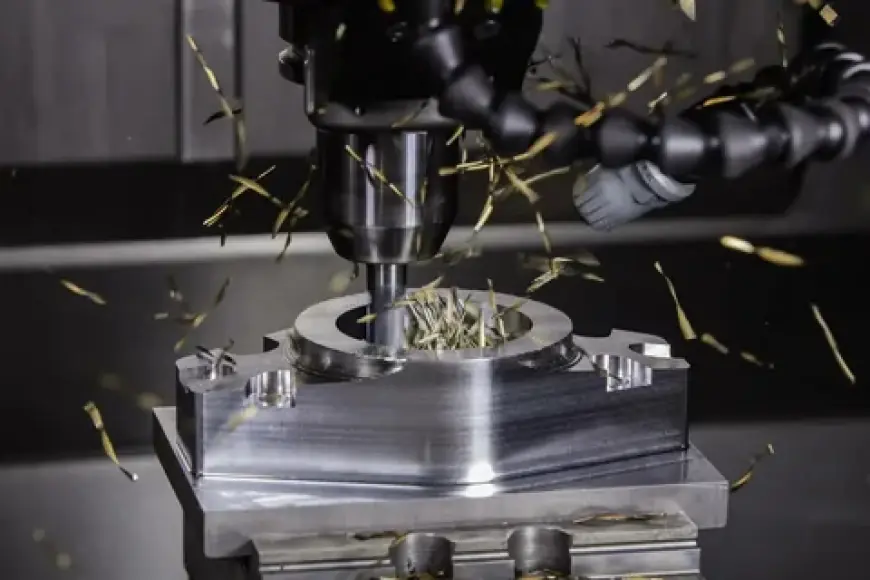
In today's fast-paced manufacturing landscape, quality and precision are paramount. CNC (Computer Numerical Control) machines have revolutionized the production process by ensuring that components and products are crafted to the highest standards. These machines automate the machining process, reducing human error, increasing consistency, and enhancing the overall quality of the output. The demand for high-quality production in industries ranging from automotive to aerospace, medical devices, and electronics has driven the adoption of CNC machines across various sectors. This article explores why CNC machines are indispensable in high-quality production and the key benefits they offer.
Precision and Accuracy in Manufacturing
CNC machines provide unparalleled precision, ensuring that every part produced is consistent and meets strict tolerances. These machines use computer programming to control the movement of tools and machines, allowing for exact replication of designs. Unlike manual machining, where the operator's skill and judgment play a significant role, CNC machines rely on computer algorithms to dictate the exact positioning and movements of tools. This leads to a level of accuracy that is difficult to achieve through traditional methods. Whether it's creating intricate parts for aerospace or medical devices, CNC machines ensure that each piece conforms to the required specifications with minimal variation.
The ability of CNC machines to perform high-precision operations is essential for industries that rely on tight tolerances. For example, in the aerospace industry, even a tiny deviation from the design can result in catastrophic failures. CNC machines mitigate these risks by offering high repeatability, ensuring that each part is identical to the last. This level of precision helps companies maintain product quality, reduce waste, and improve the overall efficiency of their production processes. The precision offered by CNC machines also minimizes the need for post-production adjustments, which further contributes to their importance in high-quality production.
Increased Efficiency and Productivity
One of the key advantages of CNC machines is their ability to boost production efficiency. CNC machines operate automatically, requiring minimal human intervention once the program is set up. This automation significantly reduces the time required to produce parts compared to traditional methods. The machines can work 24/7, without the need for breaks or shifts, which increases throughput and productivity. Furthermore, CNC machines are capable of performing multiple operations simultaneously, reducing the time needed to complete complex tasks. For example, a CNC machine can drill, mill, and tap a single part in a single cycle, which would traditionally require several machines and manual handling.
The efficiency of CNC machines also helps manufacturers save on labor costs. With the automation of tasks such as tool changes, measurements, and machining operations, there is less need for skilled labor to oversee each step of the production process. This reduction in human involvement not only lowers labor costs but also minimizes the risk of human error, leading to more consistent and accurate production. The ability to complete complex tasks quickly and accurately makes CNC machines a crucial asset in high-volume manufacturing, where speed without compromising quality is essential for meeting market demands.
Flexibility and Versatility in Production
CNC machines offer remarkable flexibility and versatility in manufacturing, making them essential for high-quality production. These machines can handle a wide range of materials, including metals, plastics, and composites, and are capable of performing a variety of machining operations. This adaptability allows manufacturers to produce different types of parts and products with minimal reconfiguration. For example, a CNC machine can easily switch from creating intricate parts for a medical device to producing structural components for an automotive manufacturer. This flexibility makes CNC machines suitable for various industries and applications.
Additionally, CNC machines can quickly adapt to changes in production requirements. Manufacturers can modify the program to alter the design of the part, adjust production speeds, or change the tools used, all without the need for major changes to the machine itself. This level of adaptability is particularly useful in industries where product designs evolve frequently, as it allows manufacturers to respond quickly to market demands and new customer requirements. The versatility of CNC machines not only enhances the quality of production but also ensures that manufacturers can stay competitive in a rapidly changing marketplace.
Reduced Waste and Material Savings
CNC machines play a crucial role in reducing waste and maximizing material efficiency. Traditional machining methods often involve a significant amount of material wastage due to manual handling and the limitations of the tools being used. In contrast, CNC machines are designed to minimize waste by optimizing tool paths and cutting techniques. The precise control of the machine ensures that materials are used efficiently, with minimal waste produced during the machining process. This is particularly important in industries that work with expensive or scarce materials, such as aerospace or medical device manufacturing.
Furthermore, CNC machines are capable of executing complex cutting patterns that reduce the need for excess material. For example, CNC routers can cut intricate shapes with high precision, ensuring that only the required amount of material is used. This not only reduces waste but also lowers the overall cost of production. By minimizing waste and maximizing the use of raw materials, CNC machines contribute to a more sustainable production process. This is an essential consideration for manufacturers aiming to meet environmental standards and reduce their carbon footprint while maintaining high-quality production.
Enhanced Quality Control and Consistency
The integration of CNC machines into production lines significantly improves the consistency and quality control of manufactured parts. CNC machines are programmed to follow exact instructions and are capable of performing multiple tasks with a high degree of accuracy. This results in a uniform output, with each part meeting the same high standards of quality. For industries where product consistency is critical, such as electronics and medical devices, CNC machines provide the reliability needed to ensure that every part is identical to the last. This consistency reduces the need for frequent quality checks and rework, leading to faster production times and lower costs.
In addition to consistent output, CNC machines are equipped with advanced sensors and feedback systems that enable real-time monitoring and adjustments during the manufacturing process. This allows for continuous quality control, with the machine automatically detecting and correcting deviations from the desired specifications. For example, if a tool becomes dull or a part is slightly out of tolerance, the machine can make adjustments on the fly to ensure the part meets the required standards. This proactive approach to quality control helps manufacturers maintain high-quality production throughout the entire production cycle, from the initial setup to the final product.
Conclusion
CNC machines are indispensable for high-quality production in modern manufacturing. Their ability to deliver precision, increase efficiency, and enhance flexibility makes them essential tools in industries ranging from aerospace to medical devices. By reducing waste, improving material utilization, and ensuring consistent output, CNC machines help manufacturers meet the growing demand for high-quality products. Moreover, the integration of CNC machines into production lines fosters greater sustainability, reduces operational costs, and strengthens quality control. As industries continue to evolve, the role of CNC machines in shaping the future of high-quality production will only become more pronounced.