Top Tips for Reducing Lumber Costs Through Efficient Estimation
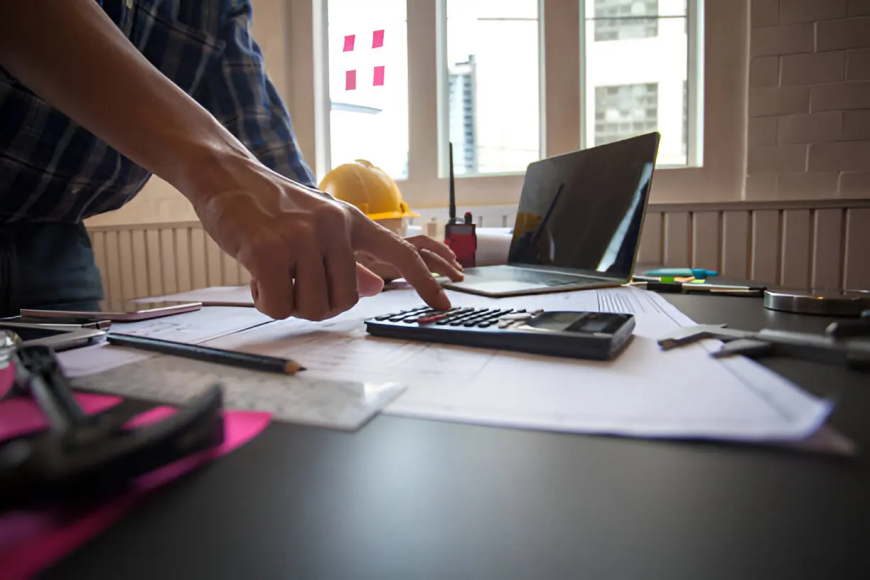
In the area of construction, managing the costs for building materials is vital for ensuring that projects remain on budget and are completed within the stipulated time. Lumber is one of the primary materials utilized for construction that are of any kind; however, the expense associated with it could have a significant influence on cost. Through the utilization of effective estimation techniques, contractors and supervisors of construction can reduce unnecessary expenses and make the most effective use of these resources. In this post, we'll discuss how to lower the price of lumber using efficient estimation methods, which result in more efficient and profitable construction projects that have a positive.
1. Accurate Takeoff Measurements
The initial step towards an efficient and effective management of wood is to carry out a thorough takeoff for lumber. The process is about determining the amount of lumber required in any given construction project, as well as ensuring those figures are as accurate as they can be. small errors of measurement could result in huge variations in the price of building, because of the over- or under-purchase of materials. A precise measure of takeoff can help avoid the waste of materials and ensure each piece of lumber is used efficaciously during the construction process.
The latest technology, comprising digital takeoff software, can benefit the precision of your job. This software lets contractors determine the exact amount of wood required while minimizing the possibility of mistakes made using hands. Through the utilization, and use of such technologies, construction managers can monitor the use of the materials and prevent costly mistakes.
2. Prioritize Reusability and Leftover Lumber Management
The control of the remaining lumber takeoff is essential to cutting expenses. The construction process usually produces more material if they aren't controlled and they could improve costs overall. Instead of discarding lumber that's not used, builders must be thinking about the possibility of reusing it in the future through the use of it in different construction projects, or by recycling it to use the other elements that form an integral part of construction.
The plan to deal with the remainder of the materials needs to be developed before starting any construction work. It can incorporate adjustments to the plan for the best utilization of small parts in addition to arranging the materials not being utilized to be stored in the future for use in the repair or other requirements associated with the construction. Recycling materials can not only lower costs but also promote sustainable construction practices that are increasingly important within the construction industry of today.
3. Choose the Right Type of Lumber for Each Project
There are a variety of types of wood that are readily available. All woods are not equally appropriate, so choosing the best kind of wood for your requirements can have a significant impact on your cost. There is a wide range of kinds of wood available that come with diverse qualities, and strengths in addition to prices. Particularly in the case of hardwood, it is a good choice in certain frame construction projects. However, in other aspects of construction, softwood could be a more affordable option without compromising top-quality quality.
Contractors should collaborate alongside engineers and designers when reviewing the requirements of the construction. They need to decide what kinds of wood give an optimal mix of cost, long-term endurance, and high-top quality. By selecting the right material, they can reduce unneeded costs and boost the efficiency of their overall project.
4. Build a Solid Supplier Relationship
Establishing a trustworthy partnership with a lumber business can result in savings over the long term. Suppliers who know about your business and your needs for the project are more likely to offer you a discount as well as bulk discounts, or access to top-quality materials with lower costs. In addition, they will grant you with details on trends in the market that will help you estimate prices for the purchases you make, and plan your purchases in a timely fashion.
The communication with the supplier will allow you to better coordinate timetables for delivery. This decreases the risk of delays or hours spent at the site. Through fostering good relationships with suppliers, contractors increase their purchasing ability and will be able to obtain higher pricing on lumber, which will result in cost savings.
5. Leverage Technology in Estimation
The significance of technology in estimating the costs of building continues to increase with the advancement of software. Software such as Building Information Modeling (BIM) and cost estimation software could reduce estimation time by giving exact estimates of the requirements for labor as well as lumber costs and timings. These technologies allow contractors to create specific plans for projects, which lowers the likelihood of over-runs about costs.
Incorporating the tools into your estimations and procedures, you'll be able to monitor the utilization of your material, immediately make changes according to the need, and ensure that you stay within the budget you have set. This degree of precision gives you more control and lessens the possibility of underestimating or exaggerating the amount of wood you will need.
6. Optimize Framing Techniques
One of the most important factors to cut down on the price of lumber is the framing techniques used during building. Modern framing methods such as spaced framing or continuous load path framing can significantly reduce the amount of lumber required, yet maintain the structural qualities. With together small studs or any other framing elements, contractors can cut down on costs of building materials, while not affecting the overall performance of the project.
Employing the expertise of estimates of framing can benefit you in reducing the amount of wood, without affecting the durability or quality of the building. These services provide specific information on the accurate ways to boost the framing estimating services so that materials are used effectively. definitely as possible.
7. Monitor Market Prices Regularly
Prices for lumber change due to various factors, such as disruptions to supply chains or market demand. Contractors who monitor the price of lumber can organize their purchases alike so that they can benefit from cheaper costs. Being aware of trends in the industry helps to avoid buying at times of high demand as well as save you cash by purchasing in large quantities during price cuts.
Participating in the most recent industry news and staying on top of communications with your suppliers could help keep track of price trends. In addition, making purchases earlier in the process of planning when the prices are lower will help in obtaining lower costs during working.
8. Improve Waste Management Practices
Management of waste is one of the most important factors in the reduction of costs associated with building. If they adopt better waste management practices contractors can be sure that less material is used on site. This means correctly storing the wood to warrant it doesn't suffer any damage caused by the elements or improper handling of the lumber precisely to limit the number of cuts, and ensure that employees are competent to work with the materials effectively.
Furthermore, outsourcing millwork estimating services could benefit to maximize the use of timber to design custom or more complex components of a structure. The services can be specialized to determine how much lumber is required for intricate millwork. This reduces waste and offers more precision when designing and executing.
Conclusion
Utilizing efficient estimation strategies plays an important role in reducing the cost of lumber in construction projects. By incorporating exact measurements of takeoffs of the lumber, improving the framing process, managing surplus materials and making use of the latest technologies, builders can cut down on the amount of garbage they generate and keep in line with budget. In addition, having a good relationship with their suppliers and being up to date with current fashions in the market can reduce costs and raise profits of construction projects. By implementing these strategies, the construction crew will be able to make considerable savings in funds and be more efficient, which will result in a successful payoff on every construction venture.