Mastering Alloy Steel CNC Machining: A Comprehensive Guide for Precision Parts丨Jucheng Precision
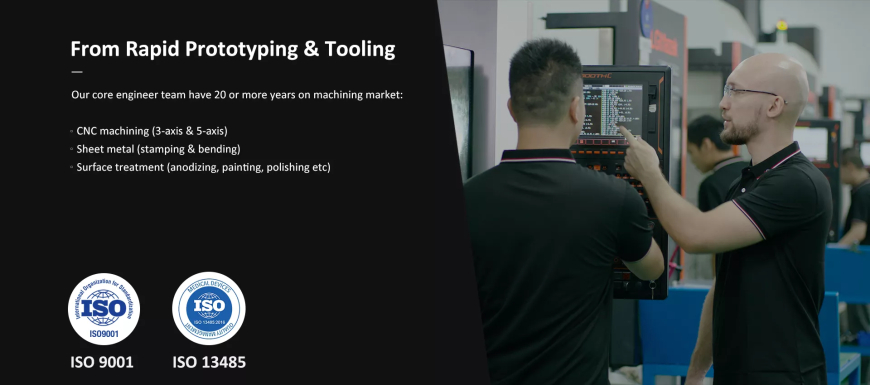
Alloy steel is a versatile and widely used material in various industries due to its enhanced mechanical properties, including strength, toughness, and wear resistance. Mastering Alloy Steel CNC Machining: A Comprehensive Guide for Precision Parts丨Jucheng Precision requires a deep understanding of material characteristics, machining techniques, and quality control measures. This comprehensive guide by Jucheng Precision aims to provide insights into mastering alloy steel CNC machining for producing precision parts.
1. Understanding Alloy Steel
Alloy steel is composed of carbon and various alloying elements such as chromium, nickel, molybdenum, and vanadium. These elements impart specific properties to the steel, making it suitable for a wide range of applications:
- Chromium: Enhances hardness, wear resistance, and corrosion resistance.
- Nickel: Improves toughness, strength, and impact resistance.
- Molybdenum: Increases strength at high temperatures and enhances hardenability.
- Vanadium: Contributes to strength, toughness, and wear resistance.
2. Material Grades and Applications
Different grades of alloy steel are used based on their specific properties and applications:
- 4140 Alloy Steel: Known for its high strength, toughness, and good fatigue resistance. Commonly used in automotive, oil and gas, and industrial machinery.
- 4340 Alloy Steel: Offers excellent toughness, strength, and fatigue resistance. Ideal for aerospace, heavy-duty shafts, and high-stress components.
- 6150 Alloy Steel: Known for its high strength, toughness, and good abrasion resistance. Used in springs, shafts, and high-strength fasteners.
- 8620 Alloy Steel: Features good toughness and wear resistance, with a balance of strength and ductility. Commonly used in gears, crankshafts, and high-wear applications.
3. CNC Machining Techniques for Alloy Steel
Machining alloy steel requires specific techniques to achieve precision and optimal results:
- Cutting Tools: Utilize high-speed steel (HSS) or carbide tools with appropriate coatings (e.g., TiN, TiAlN) to enhance tool life and performance. Carbide tools are preferred for their hardness and wear resistance.
- Cutting Parameters: Adjust cutting speed, feed rate, and depth of cut based on the hardness and toughness of the alloy steel grade. Lower cutting speeds and higher feed rates are often recommended to reduce heat generation and tool wear.
- Coolant and Lubrication: Use appropriate coolants and lubricants to dissipate heat, reduce friction, and prevent tool wear. Flood coolant or high-pressure coolant systems are effective in machining alloy steel.
- Toolpath Optimization: Optimize toolpaths to minimize cutting forces, reduce tool deflection, and ensure even material removal. Adaptive machining strategies can enhance efficiency and precision.
- Chip Control: Implement effective chip control strategies to manage chip formation and evacuation, preventing tool damage and workpiece surface defects.
4. Challenges and Solutions in Alloy Steel Machining
Machining alloy steel presents several challenges, but with the right strategies, these can be effectively managed:
- Tool Wear and Breakage: Use high-quality cutting tools, proper tool coatings, and optimize cutting parameters to minimize tool wear and breakage.
- Heat Generation: Employ adequate cooling and lubrication techniques to manage heat generation and prevent thermal deformation of the workpiece.
- Surface Finish: Achieve desired surface finishes by selecting appropriate cutting tools, optimizing cutting conditions, and using finishing operations like grinding or polishing.
- Dimensional Accuracy: Maintain tight tolerances and dimensional accuracy through precise toolpath programming, rigid fixturing, and regular tool inspection.
5. Quality Control and Inspection
Ensuring the quality of machined alloy steel parts is critical for their performance and reliability:
- Dimensional Inspection: Use precision measuring instruments such as calipers, micrometers, and coordinate measuring machines (CMM) to verify dimensional accuracy.
- Surface Finish Inspection: Employ surface roughness testers to measure surface finish and ensure it meets the required specifications.
- Material Testing: Conduct material testing, including hardness testing, tensile testing, and chemical analysis, to verify the properties of the alloy steel.
- In-Process Monitoring: Implement in-process monitoring systems to detect tool wear, machine vibrations, and other anomalies during machining operations.
6. Conclusion
Mastering alloy steel CNC machining involves understanding material properties, employing appropriate machining techniques, and implementing rigorous quality control measures. By leveraging advanced CNC technology and industry expertise, manufacturers can produce high-precision alloy steel parts that meet stringent performance and quality standards. At Jucheng Precision, we are committed to excellence in alloy steel machining, providing reliable and precise solutions for various industrial applications. With our state-of-the-art facilities and skilled team, we ensure the highest level of precision and quality in every part we produce.
What's Your Reaction?
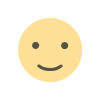
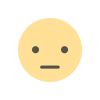
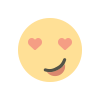
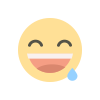
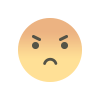
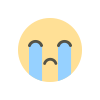
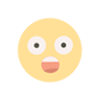