Industrial Insulators: Advancing Electrical Safety and Efficiency in Manufacturing Environments
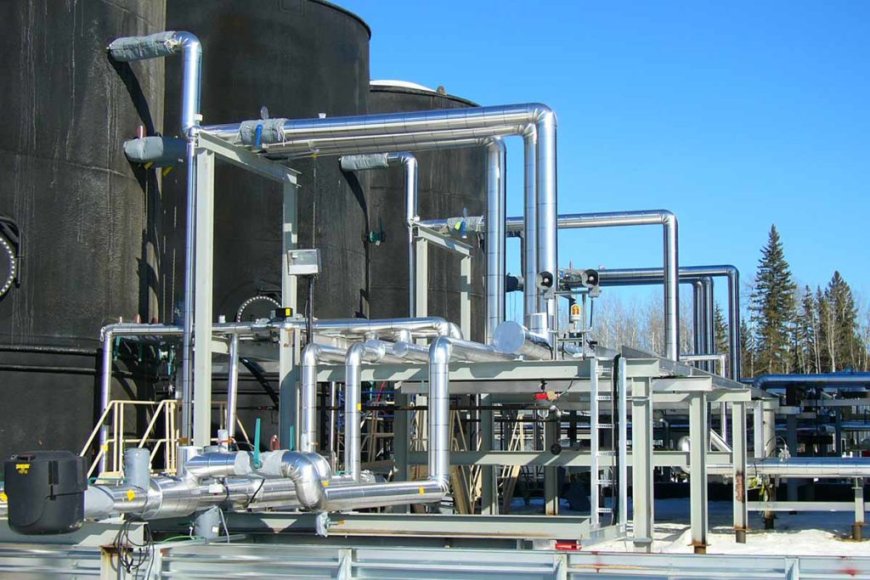
Types of Insulation Materials
There are various materials that are used for insulation in industries based on the application and operating conditions. Some of the commonly used insulation materials are:
Ceramic and Concrete Insulation: Ceramic and concrete insulations are usually used in high temperature applications above 1000°C due to their high heat resistance. They include materials like fireclay, silicon carbide, aluminum silicate, and calcium silicate. Ceramic fiber and bio-soluble fiber reinforced concrete are also used as insulation materials.
Mineral Wool Insulation: Mineral wool is one of the widely used insulation materials and is made from basalt rock and slag. It has high fire resistance and sound absorption properties. Mineral wool comes in the form of fiber, boards, and blankets based on density and application needs. Some common types are fiberglass wool, rock wool, and slag wool.
Foamed Insulation: Foamed plastic Industrial Insulators are synthetic polymer foams that provide good thermal insulation and have low density. Common varieties include polyurethane (PUR/PIR), phenolic foam, polystyrene foam. Foamed plastic insulations find applications where lightweight insulation is required.
Calcium Silicate Insulation: Calcium silicate is another widely used insulation material that is derived from furnace slag. It is durable and fire resistant. Calcium silicate provides good thermal insulation up to 1000°C. It is available as boards, blocks, and loose-fill insulation.
Perlite and Vermiculite Insulation: Perlite and vermiculite are naturally occurring mineral-based insulation materials expanded by heat treatment. They have high insulation efficiency, moisture resistance, and are lightweight. Both are used as loose-fill insulation for cavity walls and ducts.
Applications of Insulation in Various Industries
Power Industry: Thermal insulation plays a vital role in the power industry for steam and flue gas systems, boiler and pipe insulation, and insulating electrical equipment. It helps reduce heat loss, prevent condensation, protect personnel from high surface temperatures. Mineral wool, calcium silicate, and foamed plastics are commonly used here.
Petrochemical Industry: Refineries, oil pipelines, storage tanks require high temperature insulation against heat, fire, and corrosion. Ceramic fiber, calcium silicate, perlite are suitable for operating temperatures up to 650°C. Mineral wool finds usage from ambient to 400°C temperature range.
Iron and Steel Industry: Blast furnaces, coke ovens, reheating furnaces generate high heat that needs to be contained. Fireclay brick, mineral wool, calcium silicate insulation materials endure the demands of these equipment and processes.
Cement Industry: Kilns, preheaters, ducts, stacks have surface temperatures up to 1600°C. Fireclay, lightweight concrete, insulating concrete, ceramic fiber, vermiculite are suitable insulators.
Automotive Industry: Insulation is needed for exhaust manifolds, turbochargers, catalytic converters which see 300-800°C. Fibrous ceramic mats, boards withstand high heat in tight spaces.
Building Industry: Wall, floor, and pipe insulation helps regulate temperatures indoors for thermal comfort and energy efficiency. Common materials used are mineral wool, foam boards, fiberglass batts.
Refrigeration Industry: Thermal insulation helps refrigerators, freezers maintain temperatures below freezing point by preventing heat infiltration. Polyurethane, polystyrene are generally used for their good insulation values.
Challenges in Industrial Insulation Systems
The working conditions and environments in process plants are harsh with issues like high temperatures, moisture, dust, vibration that degrade insulation performance over time. Following are some key challenges for insulation systems:
Thermal Conductivity: Insulation materials lose thermal resistance when exposed to moisture, dust, chemicals over prolonged usage. This increases heat transfer defeating the insulation purpose.
Mechanical Strength: Vibration from machinery and movements can damage insulation parts leading to premature failure. Materials require sufficient compression strength, resistance to impacts.
Ageing Degradation: High temperatures, moisture cause insulation like mineral wool, polymers to structurally degrade losing density, loft over years reducing effectiveness.
Contamination: Process leaks, spillages can contaminate insulation rendering it ineffective if not chemically compatible material. Periodic cleaning is needed.
Maintenance Access: Insulating industrial vessels, ducts in congested areas is difficult. Access for repairs, retrofitting new sections is a logistical challenge.
Fire Protection: Using insulation with adequate fire resistance as per codes and standards minimize fire risks in high risk processes and areas.
With proper material selection, installation methods addressing local conditions and regular maintenance inspections, longevity and performance of insulation systems can be optimized to support reliable industrial operations over the design life.
In Summary, the use of industrial insulators is paramount in industrial settings where electrical systems are omnipresent, ensuring the safety and reliability of electrical infrastructure. These insulators act as barriers, preventing the unintended flow of electricity and mitigating the risks of electrical faults, short circuits, and fires. With advancements in materials science and engineering, industrial insulators are now available in a variety of configurations, offering high dielectric strength, thermal resistance, and mechanical durability. By incorporating robust insulator designs into their electrical systems and adhering to stringent maintenance practices, industrial facilities can minimize the likelihood of electrical incidents, safeguard personnel and equipment, and maintain uninterrupted operations.
Get more insights on Industrial Insulators
For Deeper Insights, Find the Report in the Language that You want
About Author
Vaagisha brings over three years of expertise as a content editor in the market research domain. Originally a creative writer, she discovered her passion for editing, combining her flair for writing with a meticulous eye for detail. Her ability to craft and refine compelling content makes her an invaluable asset in delivering polished and engaging write-ups.
(LinkedIn: https://www.linkedin.com/in/vaagisha-singh-8080b91)