ISO 14644 GMP Cleanroom Validation: Comprehensive Guide
Explore ISO 14644 GMP cleanroom validation with this comprehensive guide, covering standards, testing, and best practices for maintaining compliant, sterile environments.
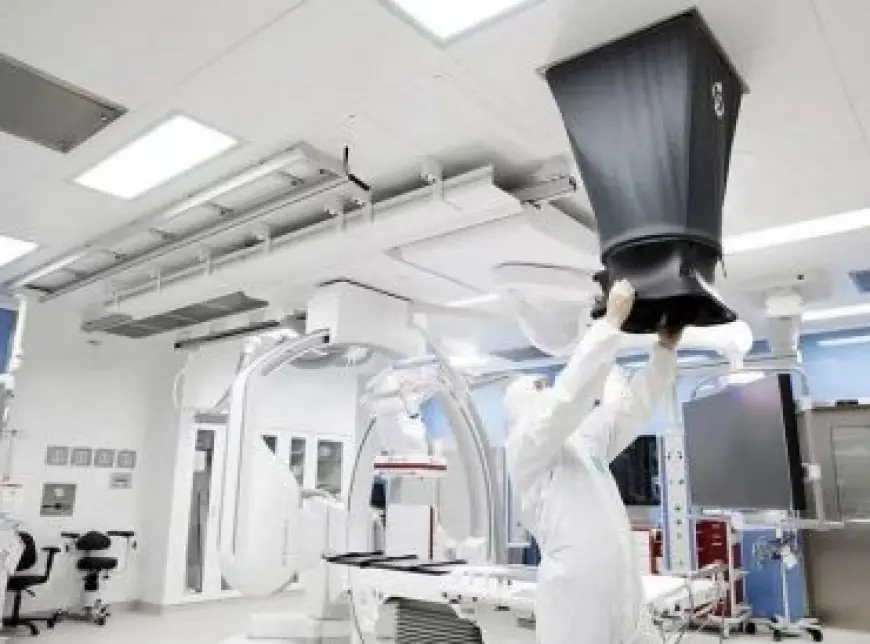
Introduction
Cleanrooms are an integral part of industries requiring controlled environments to manufacture high-quality products. Achieving compliance with ISO 14644 and GMP standards ensures these spaces meet stringent cleanliness and safety criteria. This article delves into ISO 14644 GMP cleanroom validation, covering its importance, methodology, and impact on industry practices.
Understanding Cleanrooms
What Are Cleanrooms?
Cleanrooms are specially designed spaces where environmental factors like air quality, temperature, and humidity are controlled to minimize contamination risks. These spaces are critical in sectors like pharmaceuticals, biotechnology, and electronics.
Key Features and Components of Cleanrooms
- Air Filtration Systems: HEPA and ULPA filters to maintain air quality.
- Controlled Airflow: Unidirectional or turbulent airflow for particulate control.
- Sealed Walls and Floors: Prevent contamination ingress.
Applications of Cleanrooms in Various Industries
From drug manufacturing to semiconductor production, cleanrooms ensure products meet stringent safety and quality standards.
ISO 14644 Standards
Overview of ISO 14644
ISO 14644 is the global benchmark for cleanroom design, operation, and classification. It defines cleanliness levels based on airborne particles, ensuring consistent standards.
Key Classifications in ISO 14644
- ISO Class 1: Highest cleanliness level with minimal particulate presence.
- ISO Class 9: Permits higher particle levels, suitable for less sensitive processes.
GMP Requirements for Cleanrooms
GMP standards align with ISO 14644 to enforce hygiene and safety. Adherence involves strict protocols, including personnel training and regular monitoring, ensuring the end product's integrity and safety.
Cleanroom Validation
Definition of Cleanroom Validation
Validation is a systematic process to confirm that cleanrooms meet predefined criteria for operational performance.
Steps in Cleanroom Validation
- Design Qualification (DQ): Validating the cleanroom’s design.
- Installation Qualification (IQ): Ensuring all components are correctly installed.
- Operational Qualification (OQ): Testing operational aspects of systems.
- Performance Qualification (PQ): Assessing performance under real-world conditions.
Critical Tests in Cleanroom Validation
Airflow Pattern Testing
Ensures air moves uniformly, preventing contamination.
Particle Count Testing
Confirm the number of airborne particles is within specified limits.
HEPA Filter Integrity Testing
Verifies filters effectively trap contaminants.
Best Practices for ISO 14644 GMP Compliance
- Regular Training: Keeping personnel updated on protocols.
- Documentation: Recording all validation activities.
- Periodic Audits: Identifying and correcting compliance gaps.
Conclusion
ISO 14644 GMP cleanroom validation is essential for industries reliant on contamination-free environments. It ensures product safety, regulatory compliance, and customer trust. By following proper validation protocols, organizations can uphold the highest quality standards.
FAQs: Frequently Asked Question
Q. What industries require ISO 14644 compliance?
Ans. Industries like pharmaceuticals, electronics, and aerospace depend on ISO 14644 for contamination control.
Q. How often should cleanrooms be validated?
Ans. Cleanrooms should be validated annually or whenever significant changes occur.
Q. What is the role of particle counters in cleanroom validation?
Ans. Particle counters measure and monitor airborne particulates, ensuring compliance.
Q. Can a cleanroom fail validation? If so, what happens?
Ans. Yes, failure triggers corrective measures, retesting, and process optimization.
Q. How does ISO 14644 differ from other cleanroom standards?
Ans. ISO 14644 focuses on airborne particles, while other standards may address specific contamination sources.