From the Drawing Board to Your Desk: The WhiteeFox Design Process
White Fox | Shop High Quality White Fox Clothing at Sale Price. Get up to 30% off on hoodie, shirt and tracksuit. White Fox Boutique Australia.
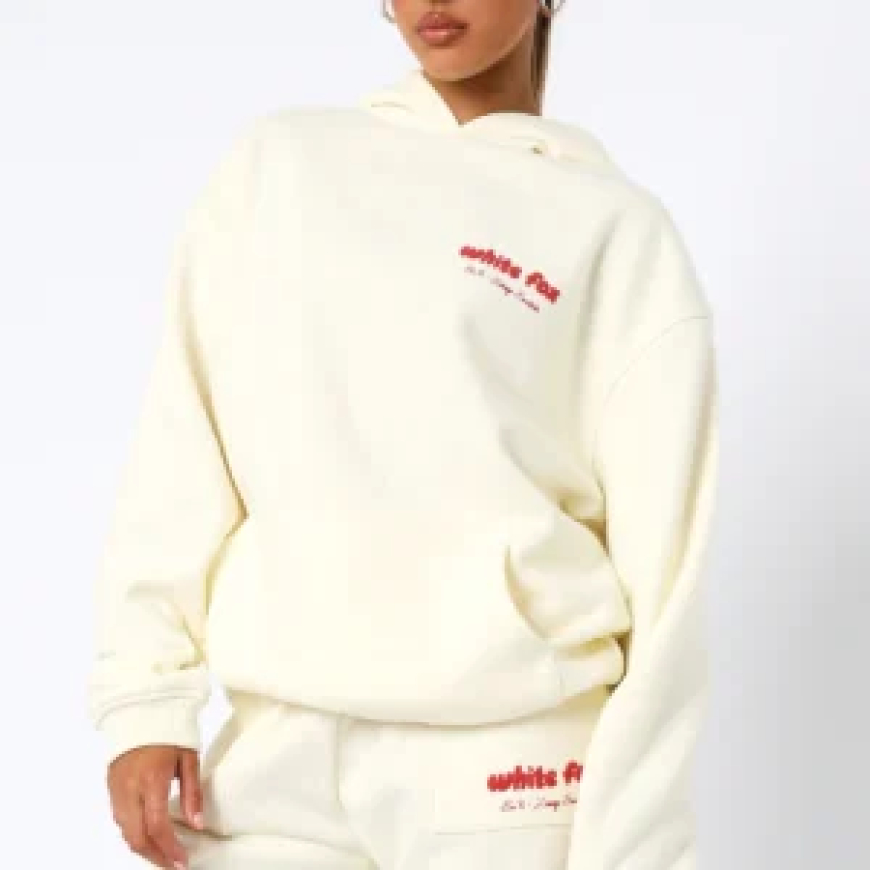
In the fast-paced world of tech accessories, white fox where style and functionality must seamlessly blend, WhiteeFox stands out for its meticulous design process. From conceptual sketches to the final product on your desk, the journey of a WhiteeFox accessory is a testament to innovation, craftsmanship, and dedication to user satisfaction. This article provides an in-depth look into the intricate design process behind WhiteeFox’s tech accessories, highlighting each phase of development and what makes their products exceptional.
Ideation:
The journey of a WhiteeFox product begins with ideation, where the foundation for innovation is laid. During this phase, the team engages in extensive brainstorming sessions, market research, and trend analysis to identify gaps and opportunities in the tech accessories market. This process involves evaluating consumer needs, emerging technologies, and industry trends to ensure that the products will meet and exceed expectations.
WhiteeFox’s design team collaborates closely with engineers, marketers, and user experience experts to generate a wide range of ideas. Each concept is carefully considered, with a focus on how it can enhance functionality, aesthetics, and overall user experience. The goal of the ideation phase is to create a product vision that aligns with WhiteeFox’s commitment to innovation and excellence.
Sketching and Prototyping:
Once a concept is approved, the design process moves into the sketching and prototyping phase. This stage is crucial for translating abstract ideas into tangible designs. WhiteeFox’s designers create detailed sketches and digital renderings to visualize how the product will look and function.
Prototyping is a key part of this phase, allowing the team to build physical models of the accessory. These prototypes are used to test the design, materials, and functionality of the product. WhiteeFox employs advanced prototyping techniques, including 3D printing and CNC machining, to create accurate and high-quality prototypes. This process helps identify potential issues and refine the design before moving on to production.
Material Selection:
Material selection is a critical step in the design process, as the choice of materials directly impacts the performance, durability, and appearance of the final product. WhiteeFox is known for its rigorous approach to material selection, ensuring that only the highest quality materials are used.
The design team evaluates a variety of materials, including premium leathers, durable metals, and advanced polymers. Each material is assessed for its properties, such as strength, flexibility, and aesthetic appeal. WhiteeFox also considers sustainability, opting for eco-friendly materials whenever possible. This careful selection process ensures that the final product not only meets high standards of quality but also aligns with the brand’s commitment to environmental responsibility.
Engineering and Technical Development:
With the design and materials in place, the focus shifts to engineering and technical development. This phase involves translating the design into a fully functional product by addressing technical challenges and ensuring that all components work together seamlessly.
WhiteeFox’s engineering team works closely with designers to refine the product’s technical specifications, including dimensions, tolerances, and performance criteria. This stage involves extensive testing to ensure that the accessory meets industry standards and performs reliably under real-world conditions. WhiteeFox employs state-of-the-art testing equipment and methodologies to validate the functionality and durability of each product.
User Experience Testing:
User experience testing is a crucial part of the design process, as it provides valuable insights into how the product performs in everyday use. WhiteeFox conducts rigorous testing with real users to gather feedback on the accessory’s functionality, comfort, and overall usability.
During this phase, prototypes are distributed to a select group of testers who use the product in their daily routines. Their feedback is collected through surveys, interviews, and usage data to identify any issues and areas for improvement. This user-centered approach ensures that the final product is not only aesthetically pleasing but also practical and user-friendly.
Refinement and Iteration:
Based on the feedback received during user experience testing, WhiteeFox enters the refinement and iteration phase. This stage involves making adjustments to the design, materials, and functionality to address any issues identified during testing.
The design team works closely with engineers to implement changes and improvements, often creating several iterations of the product before finalizing the design. This iterative process is essential for achieving the highest standards of quality and performance. WhiteeFox’s commitment to perfection ensures that each product is meticulously refined to meet the brand’s exacting standards.
Production Planning:
Once the design is finalized, WhiteeFox moves into production planning. This phase involves preparing for large-scale manufacturing by establishing production workflows, sourcing materials, and setting up quality control processes.
WhiteeFox partners with experienced manufacturers and suppliers to ensure that the production process runs smoothly and efficiently. The brand’s production planning team coordinates all aspects of manufacturing, including assembly, quality checks, and packaging. By carefully managing this phase, WhiteeFox ensures that each product is produced to the highest standards and meets the expectations of its customers.
Quality Control:
Quality control is a critical component of the production process, ensuring that every WhiteeFox accessory meets the brand’s high standards of excellence. The quality control team conducts thorough inspections at various stages of production to identify and address any defects or inconsistencies.
WhiteeFox employs a range of quality control measures, including visual inspections, functional tests, and material analysis. Each product undergoes rigorous testing to verify that it meets the required specifications and performs as intended. This commitment to quality ensures that customers receive products that are not only stylish and functional but also durable and reliable.
Launch and Distribution:
With production complete and quality control checks in place, WhiteeFox prepares for the product launch and distribution. This phase involves coordinating marketing efforts, setting up distribution channels, and ensuring that the product reaches customers in a timely manner.
WhiteeFox’s marketing team develops comprehensive launch strategies, including promotional campaigns, product releases, and partnerships with retailers. The distribution team ensures that the product is available through various channels, including online stores, physical retailers, and direct sales. By carefully managing the launch and distribution process, WhiteeFox ensures that its products are successfully introduced to the market and reach customers effectively.
Customer Feedback and Continuous Improvement:
The design process doesn’t end with the product launch; WhiteeFox is committed to continuous improvement based on customer feedback and market trends. After the product is in the hands of consumers, the brand actively seeks feedback to identify areas for enhancement and to inform future design efforts.
WhiteeFox monitors customer reviews, conducts surveys, and analyzes sales data to gain insights into how the product is performing and how it can be improved. This ongoing feedback loop allows the brand to make informed decisions about product updates and new designs, ensuring that it remains responsive to customer needs and market demands.
The design process at WhiteeFox is a comprehensive and meticulous journey that transforms innovative ideas into high-quality tech accessories. From ideation and sketching to production and distribution, each phase of the process is carefully managed to ensure that the final product meets the highest standards of design, functionality, and user experience.
WhiteeFox’s commitment to excellence is evident in every aspect of its design process, from the selection of materials and technical development to quality control and customer feedback. This dedication to innovation and craftsmanship sets WhiteeFox apart as a leading brand in the tech accessories market, making it a true standout in the industry.
As technology continues to evolve and consumer expectations shift, WhiteeFox’s design process will continue to adapt and grow. By maintaining a focus on quality, user experience, and continuous improvement, WhiteeFox is well-positioned to remain at the forefront of the tech accessories market and deliver products that elevate the tech game for its customers