How an Integrated QMS Reduces Product Defects and Enhances Quality Control
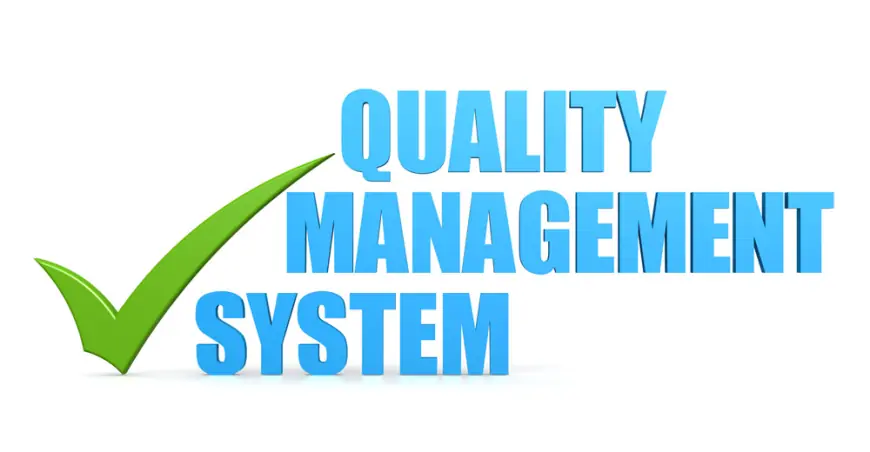
Picture this: you’re building a puzzle. If all the pieces fit perfectly, the picture comes out just right. But the whole picture looks off if even one piece is missing or doesn’t fit. Now, think of a company making products like toys, phones, or even food. If even one step in the process goes wrong, like using the wrong materials, skipping a safety check, or not testing the product properly, the final product might not work well or could even be unsafe. That’s where a quality management system (QMS) comes in. It’s a guide that helps companies make sure every piece of the puzzle fits perfectly, reducing mistakes and making better products.
A quality management system is a structured way for companies to maintain the quality of their products and services. It involves a set of processes, rules, and checks to ensure everything runs smoothly. When this system is integrated, it means all departments and processes work together as one unit instead of separate teams doing their own thing. This makes it easier to spot problems, fix them quickly, and prevent them from happening again.
How an Integrated QMS Reduces Product Defects
1. Identifies Problems Early
One of the biggest reasons products have defects is that problems go unnoticed until it's too late. An integrated QMS quality management system allows businesses to detect issues at every production stage. This means that instead of waiting until a product is finished to check for problems, companies can find and fix mistakes right away.
2. Ensures Consistency
Have you ever noticed that buying a popular snack always tastes the same no matter where you get it? That’s because of a strong QMS. When businesses follow strict quality guidelines, they ensure every product is made the same way and meets the same standards.
Different teams might follow different procedures without an integrated system, leading to inconsistencies. One batch of products could be perfect, while another might have defects. A QMS ensures that all processes are uniform, reducing the chances of defective products.
3. Improves Communication Between Teams
Many companies have multiple teams working on different parts of a product. If these teams don’t communicate well, mistakes can slip through. An integrated QMS makes sure that everyone is on the same page. If one department spots an issue, they can quickly alert the others and work together to solve it.
4. Uses Data to Prevent Future Defects
An integrated QMS quality management system doesn’t just focus on fixing current problems. It also helps prevent future defects by analyzing data. Businesses track trends and patterns to see what’s causing defects. They then make changes to avoid the same issues from happening again.
For example, if a bakery notices that their bread keeps coming out too hard, they can check their system and see what’s going wrong. Maybe the dough isn’t mixed long enough, or the ovens are too hot. By analyzing data, they can make adjustments and ensure the bread comes out perfectly every time.
5. Ensures Compliance with Regulations
Every industry has rules and regulations that businesses must follow. Be it food safety standards, manufacturing guidelines, or health regulations, companies need to comply to avoid legal trouble and keep customers safe. An integrated QMS ensures that businesses meet all these requirements.
Without a proper system in place, companies might miss important steps, leading to legal issues, fines, and even product recalls. A strong QMS helps businesses stay compliant and maintain a good reputation.
How an Integrated QMS Enhances Quality Control
Reducing defects is just one part of the equation. An integrated QMS also enhances overall quality control, making sure every product is up to standard before it reaches customers.
● Standardized Processes – Quality remains consistent across all products when everyone follows the same steps.
● Training and Development – Employees are properly trained to maintain high-quality work.
● Customer Satisfaction – Fewer defects mean happier customers who trust the brand.
● Cost Savings – Fixing defects early prevents expensive recalls and wasted materials.
No one wants to buy a defective product. Businesses that fail to focus on quality control risk losing customers and damaging their reputation. An integrated QMS helps companies detect problems early, improve communication, ensure consistency, and follow regulations. This reduces defects, builds customer trust, and improves overall efficiency.