Understanding Boiler System Components and Troubleshooting Common Problems
These are the top 5 most common problems with boilers. We discuss many component that are found in water boilers.
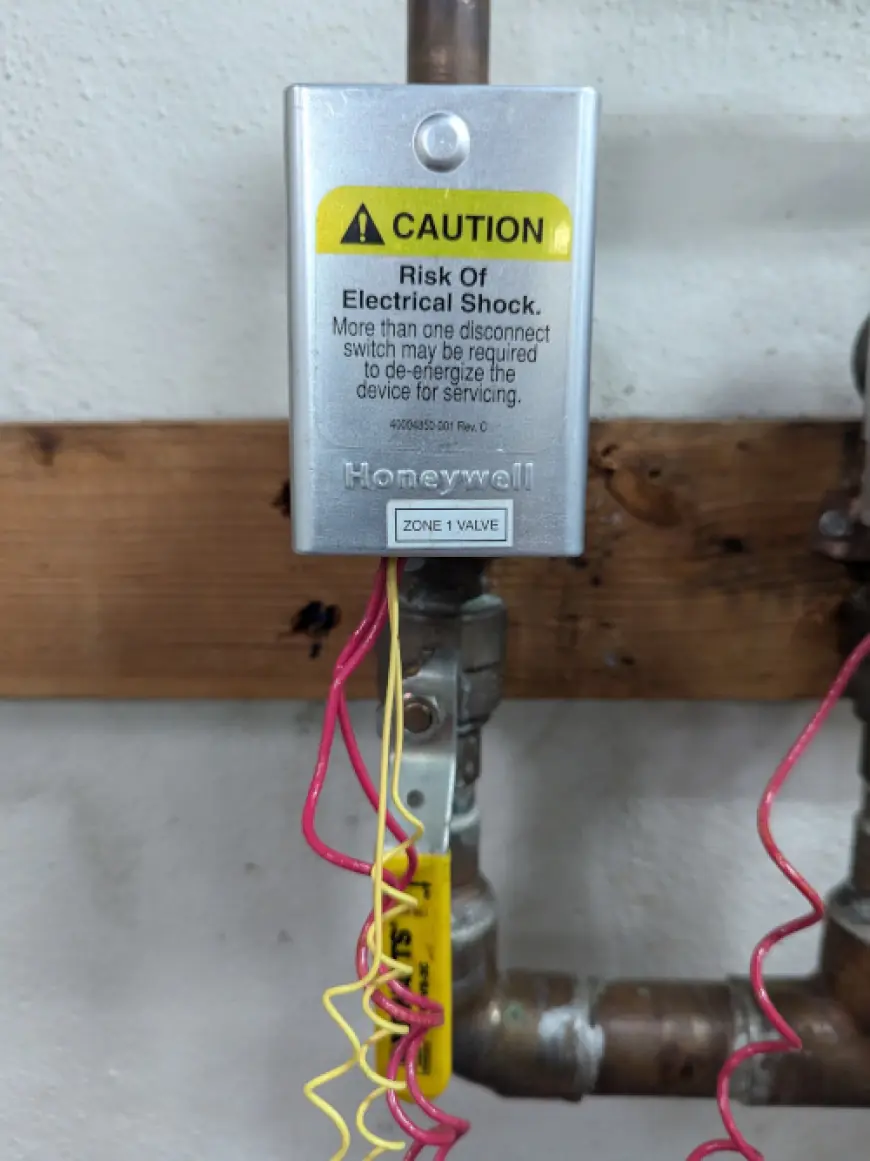
As the cold mid-November embark to the Northeast, keeping your home warm is a must. For households with boiler systems, understanding the essential components and recognizing potential issues is vital for maintaining both comfort and efficiency. With over 20 years of HVAC experience in Northern NJ these are the 5 top common issues we face.
Whether you're troubleshooting or scheduling boiler repair, this guide provides practical advice to help you address common problems effectively. Below, we highlight five frequently encountered boiler issues, focusing on the components involved and offering actionable solutions.
1. Zone Valves: The Key to Targeted Heating
Zone valves play a pivotal role in directing heat to specific areas or “zones” in your home. They function by:
- Regulating Hot Water Flow: When a thermostat signals a need for heat, the zone valve opens, allowing hot water to circulate to the designated area.
- Signaling the Boiler: The End Switch within the zone valve activates the boiler's aquastat relay, starting the ignition process and powering the circulation pump.
Common Zone Valve Issues
- Non-Responsive Zones: A faulty valve may fail to open, leaving some zones without heat. This can be particularly frustrating in multi-zone systems where multiple areas might experience heating disruptions.
- Stuck End Switch: When the End Switch malfunctions, the boiler may run continuously, leading to wasted energy and unnecessary wear.
Maintenance and Replacement Tips
- Thorough Inspection: Before replacing a zone valve, check related components to rule out cascading failures, such as blockages in ball valves.
- Proactive Replacement: If your zone valves were installed simultaneously, consider replacing all of them at once. Honeywell valves, for example, have an average lifespan of about 14 years.
Comparing Furnace and Boiler Zoning
Unlike furnaces, which use dampers for zoning, boiler systems rely on zone valves. This distinction means that furnace repair requires different diagnostic approaches and tools compared to boiler systems.
Popular Zone Valve Models
- Honeywell V8043 (4-wire): A user-friendly and reliable choice for zoning.
- Taco 571-2: Another durable option trusted by professionals and homeowners alike.
Proper zoning enhances comfort while optimizing your heating system’s energy efficiency.
Since Honeywell spun off Resideo, Honeywell and Resideo zone valves and dampers are interchangeable and offer the same reliability.
2. Aquastat Relay:
Key Functions
- Temperature Regulation: The aquastat relay monitors water temperature, ensuring it stays within optimal limits for efficient heating.
- Safety Management: It works with the low-water cutoff switch to protect the boiler from damage in case of water depletion.
- System Coordination: The relay ensures that all components, from thermostats to pumps, work in harmony to deliver consistent heating.
Common Aquastat Issues
- Temperature Fluctuations: If the aquastat is malfunctioning, the boiler may overheat or fail to reach the desired temperature, affecting overall performance.
- Electrical Failures: Loose or corroded wiring can disrupt the relay's operation, potentially causing the boiler to shut down unexpectedly.
Maintenance Tips
- Regular Inspections: Periodically check the wiring and terminals for corrosion or damage to prevent sudden failures.
- Professional Calibration: Ensure that the aquastat is correctly calibrated by a certified technician for optimal performance.
Replacing an aquastat can seem daunting, but with models like the Honeywell 8148, the process is streamlined for HVAC contractors familiar with the system's wiring layout.
3. Circulator Pumps:
The circulator pump is essential for distributing hot water from the boiler to radiators or baseboards throughout your home. Without it, the system cannot effectively transfer heat.
Key Roles
- Ensuring Flow: The pump maintains a steady flow of water, ensuring even heating across all zones.
- Preventing Stagnation: By keeping water in motion, it reduces the risk of sediment buildup and corrosion within the system.
Common Circulator Pump Problems
- Noisy Operation: Unusual noises often indicate air trapped in the system or worn-out bearings in the pump.
- Leakage: A leaking pump could signal a failing seal or excessive pressure in the system.
- Failure to Start: Electrical issues or a burned-out motor may prevent the pump from operating.
Maintenance and Replacement Tips
- Bleed the System: Regularly bleed the boiler system to remove trapped air, which can strain the pump.
- Inspect Seals and Wiring: Look for leaks or frayed wires that could compromise performance.
- Upgrade When Necessary: Modern circulator pumps, such as high-efficiency models, can reduce energy consumption while enhancing reliability.
4. Low-Water Cutoff: A Critical Safety Feature
The low-water cutoff is a safety device designed to protect your boiler from running dry, which could lead to overheating and severe damage. Importantly, a low-water cutoff is required by code in most jurisdictions and is not optional, underscoring its critical role in ensuring the safe operation of your heating system.
Functionality
- Monitoring Water Levels: It detects when water levels drop below a safe threshold and shuts down the boiler to prevent overheating.
- Enhancing Longevity: By preventing damage caused by dry firing, it extends the lifespan of the boiler.
Common Issues
- False Tripping: Dirt or debris in the sensor can cause the cutoff to shut down the boiler unnecessarily.
- Sensor Malfunction: Wear and tear over time can impair its accuracy, leaving your boiler vulnerable.
Maintenance Advice
- Clean the Sensor: Periodic cleaning prevents false readings and ensures accurate operation.
- Test Regularly: Perform routine tests to confirm the cutoff responds correctly when water levels are low.
5. Expansion Tank: Managing Pressure
The expansion tank is a vital component that accommodates the natural expansion of water as it heats. It prevents pressure buildup that could damage the boiler or pipes.
How It Works
- Absorbing Excess Pressure: The tank contains a bladder or diaphragm that absorbs water's expansion, maintaining consistent pressure in the system.
Signs of a Problem
- Pressure Spikes: A failing expansion tank can lead to fluctuating system pressure, potentially triggering the pressure relief valve.
- Waterlogged Tank: If the bladder inside the tank ruptures, it can become waterlogged, compromising its ability to regulate pressure.
Maintenance and Troubleshooting
- Check the Air Charge: Use a pressure gauge to ensure the tank has the correct air pressure, typically around 12–15 psi for residential systems.
- Inspect for Leaks: Replace the tank if it shows signs of leaking or internal damage.
Proactive Maintenance for Boiler Longevity
Keeping your boiler in peak condition involves regular inspections, timely repairs, and understanding the interplay between its components. Here are some additional tips:
- Annual Servicing: Schedule a professional tune-up before the heating season to identify and address potential issues.
- Monitor System Pressure: Keep an eye on the pressure gauge to ensure it stays within the manufacturer’s recommended range.
- Bleed Radiators: Remove trapped air from radiators for consistent heat distribution.
- Upgrade Strategically: Consider replacing aging components, such as zone valves or circulator pumps, with modern, energy-efficient alternatives.